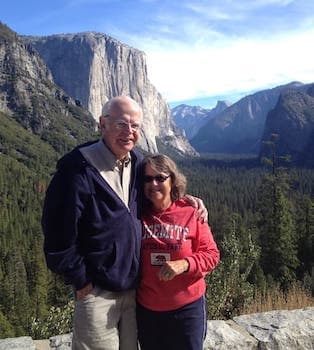
Curated with aloha by
Ted Mooney, P.E. RET
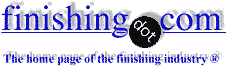
The authoritative public forum
for Metal Finishing 1989-2025
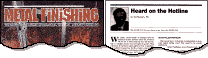
-----
Problems & Solutions in Powder Coating of Steel Tubing
Q. At our company we are having a problem with some of our powder coated steel frames leaking some sort of oily fluid from the weld joints. Our supplier claims they are baking the welded frame (size varies from 3ft cube to 10ft cube) at 400 °F for one hour, letting it cool, and then applying white powder coat. They ship the frames to our facility and most are fine. Last week though, we had two of them dump a dark brown oily fluid down the side of the frame coming from the welded seam.
I inspected the welds and they are not that good but what is coming out? It must be the oily residue from the mill on the tube, but it should happen on all of them. Is there an industry standard on pre-cleaning tubing before welding? I would appreciate any help on this problem. Thanks, Kenny Dillard Value Engineering
- Austin, Texas
2003
A. The only time I have experienced this on my line was when the maintenance crew cranked up the Lube Con and oil overflowed out of my inverse monorail conveyor. Otherwise, if it happens exclusively at the weld there is most definitely a breach of cutting/milling oils penetrating the weld and pooling inside of the "tubular" cavities of the finished part. It may not be visible with incoming inspection, but dry off and cure oven temperatures may reduce the viscosity of these oils allowing them to flow all over the painted surface and staining the cured film. I would recommend investigating inside the cavity where it looks like the "runs" originated and see if there is a glob of oil or a defined outline of a pool of oil near the source of the defect. If this is the problem, hire a new welder.
Andy PealAutomotive Components - Grand Rapids, Michigan, USA
2003
Iron tubing fence is rusting in 6 months despite powdercoating
Q. We put up a fence late April. Powdercoating was offered at an extra cost. We had the powdercoating done. Now six months later we have rust spots coming thru at various locations through out the fence. How is this possible? I thought powdercoating should have put a longer life on the fence than six months.
Joseph Caseybuyer - Las Vegas, Nevada
2007
![]() |
A. I fear that you have been a little misled. Powdercoating is just another way of applying a paint-like finish. Its a corrosion protection only as long as the layer is unbroken, initially, but as virtually all paint systems (including PC) are partially porous, moisture will eventually get in. ![]() Geoff Crowley Crithwood Ltd. Westfield, Scotland, UK ![]() 2007 A. Dear Joseph, Birmingham, United Kingdom 2007 A. It's not the paint, it's the pretreatment. It must've been inadequate for the end use. That's not to say that the pretreatment was bad, it's saying that there are different pretreatments for powder coating and the one used probably wasn't resilient enough for the environmental conditions that the fence was installed in. ![]() Sheldon Taylor supply chain electronics Wake Forest, North Carolina 2007 |
Powder Coat Spotting
Q. We are a producer of steel tubing. The tubes are powder coated to a thickness of 2-3 mils and are sent through an IR oven to cure. Recently we have noticed "spots" on our tubes. The defect is a circle on the handle that has no powder, just bare metal, and has a radius of 1.5 - 3.0mm. I have looked at some of these spots under magnification and it looks like the edge of the "spot" has had all of the powder removed, while the center of the spot still has a slight covering. Would this be considered a pinhole defect and if so what is the best way to solve the issue.
Jon FranklinPlating Shop Employee - Champaign, Illinois
September 21, 2009
A. It's not a pinhole, it's a fisheye. Fisheyes are caused by a contaminate on the substrate. Usually a drop of oil from somewhere in the system. The cause is very hard to find for someone that is searching for it in the facility let alone a third party that is just guessing. Good luck with it.
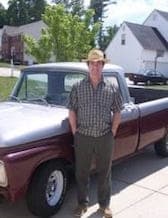
Sheldon Taylor
supply chain electronics
Wake Forest, North Carolina
September 25, 2009
Scratch-like defect on powder coated steel tubes
December 30, 2013Q. Hello guys, I make bicycles in low volume and today I found a horrible "defect" on the top tube of a new bicycle model I am launching (my demo unit). The frame is made of 1,6 mm thick cold drawn steel (low carbon) that has been TIG welded.
The frame was painted 3 weeks ago and the bike was assembled without any hassle.
The fully assembled bicycle has been staying in my shops window and has been suffering intense heat and sun exposure in the last 10 days (I am in Argentina and temperatures here are 35 °C these days).
How can this defect appear after so many days?
Bicycle builder - Buenos Aires, Argentina
A. Something strange here.
Powdercoating isn't likely to develop a crack like that on its own.
I winder if this is the seam weld opening (perhaps not fully welded). You did say cold drawn tube, so presumably ERWelded tubing. Sometimes can have seam weld faults?
There appears to be another issue too. In the images there seem to be streaks of lighter colour. That doesn't look right either.
Thin coats sometimes have defects showing through, where thinness causes lack of opacity, but not typically in long narrow lines like that.
Sorry that hasn't been very helpful!
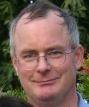
Geoff Crowley
Crithwood Ltd.
Westfield, Scotland, UK
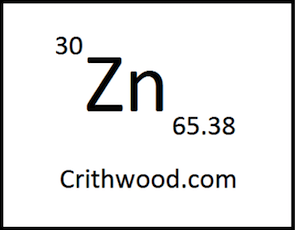
January 3, 2014
on AbeBooks
or Amazon
(affil links)
Hi Geoff. I had bigger and higher resolution photos, and I think the streaks of lighter color are just reflections. I believe Eduardo's complaint is those long splits in the paint. You may be right about the tubing; thanks.
Regards,
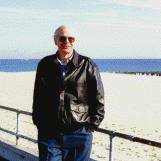
Ted Mooney, P.E.
Striving to live Aloha
finishing.com - Pine Beach, New Jersey
January 2014
Hello guys, thanks a lot for the help.
Geoff, as Ted said, the lighter color areas are just reflections. The color is very homogeneous.
We are also suspecting on a crack on the tube itself (worst situation...).
Will let you know how it goes as we find it.
Regards.
- Buenos Aires, Argentina
January 4, 2014
A. Eduardo
Thanks for clarification about the reflections. I could see that some lines were that, but some I wondered about.
One way to tell if this is the weld seam is to look at the inside of the tube. (if you can).At the seam you will see a raised line, perhaps as much as the wall thickness of the tube. If that runs along the same line as the "crack", then for sure this is faulty seam weld.
If the crack is not truly parallel to the tube (if it spirals at all), then maybe not seam weld.
There's a distant possibility of a slag inclusion in the sheet the pipe was made from. Slag inclusions get rolled into elongated faults, which sometimes are not so visible until some other treatment, then they're obvious.
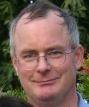
Geoff Crowley
Crithwood Ltd.
Westfield, Scotland, UK
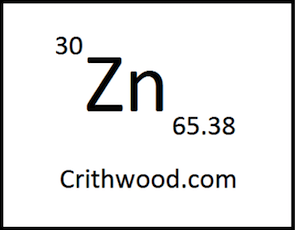
January 6, 2014
January 7, 2014
Thanks Geoff, I probably will take it to the painters this week and they will make some investigation on it.
Unfortunately it is in the top tube of a bicycle frame so it is impossible to explore inside (ends closed).
Will let you guys know how it develops...
Regards!
- Buenos Aires, Argentina
January 10, 2014
A. I totally agree with Geoff on this fault.
I doubt whether the Coater will add to the solution.
Faulty tube is back to the Tubemaker.
Is it imported Tube?
Does it comply with First World Standards?
These are questions for the Tube Supplier.
Bill
Trainer - Salamander Bay, Australia
January 16, 2014
Hello Guys, today I took the frame to the painter's and after removing some paint we found the "crack" on the tube.
Pictures:
We will probably have to build a new frame or replace the faulty tube.
Thanks for all the help and let me know in the case I can help anybody with the experience.
-Eduardo
- Buenos Aires, Argentina
Powder Coating Peels from concrete-filled tubing
Q. Hi concern,
We are manufactures of Machine where it frame are made up of CR square Pipe. We fill in concrete to gain machine weight. Afterward we weld complete frame and send it for Powder Coating. Now we are facing Peel Off problem even after we complete seven tank process.
Our supplier admit that due to having concrete in the frame this problem of peel off arises.
Please suggest how to avoid this problem?
Buyer - Surat, Gujarat, & India
October 29, 2015
A. Does your powdercoater do any tests on the coating (or on sample panels) after each coating? If not how do they know they have done it properly.
It seems likely that the concrete before coating makes the material react differently to heat for curing the powder. It will take longer to cure the powder with this "heat sink" inside the tube.
You mention pretreatment. 7 tank process sounds good, but it depends what's in those tanks? On such steel is this iron phosphate?
For the powder to "peel off" either it's not cured, or not adhered. Curing is a temperature issue. Adhesion is a pretreatment issue.
Have you tried one without concrete to see if that's different?
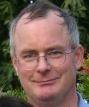
Geoff Crowley
Crithwood Ltd.
Westfield, Scotland, UK
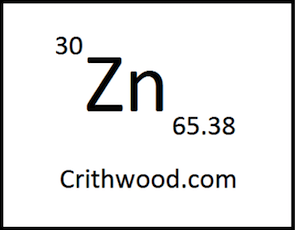
October 29, 2015
November 7, 2015
A. Totally agree with Geoff on this one.
How can you possibly expect such a heat sink to achieve a cure?
I can imagine it would take hours to reach an acceptable cure and unless the temperature was moderated possibly even an overbake surface temperature would be achieved.
This is definitely an amateur attempt to achieve an impossible objective.
Regards,
Bill
Trainer - Salamander Bay
Tube Coating
Q. Hi all, I am working in an sheetmetal press parts manufacturing company. We are facing a continuous rejection of parts after powder coating and almost 20% rejection. We are trying our best in all ways by changing the powder, water, ... still we incur rejections and woos out issue from the tube. Kindly need your suggestions in order to reduce the loss.
Shriram Navani- Chennai, tamilnadu, India
August 1, 2020
? Hi Shriram. People would like to help, but how can anyone know where to begin? Please start with a careful description of what "woos out" means, some photos of defective parts, and a brief summary of your process. Thanks.
Luck & Regards,
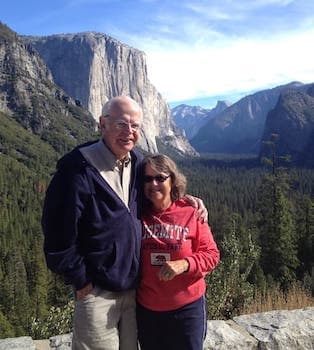
Ted Mooney, P.E. RET
Striving to live Aloha
finishing.com - Pine Beach, New Jersey
August 2020
A. Shriram,
Agree with Ted's response.
On this site there's people who would like to help, and who quite possibly can help, but we're engineers, coaters, and manufacturers. We're not mind readers, or prophets!
All we know about your situation is what you tell us, and nothing more.
If you ask a question that doesn't help us to answer; doesn't give the background, then all we can answer is that "You're doing it wrong".
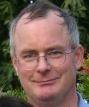
Geoff Crowley
Crithwood Ltd.
Westfield, Scotland, UK
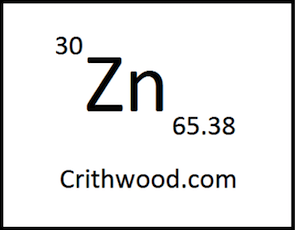
September 9, 2020

Q, A, or Comment on THIS thread -or- Start a NEW Thread