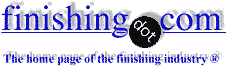
-----
Acid Copper over Zinc Die-cast cut through during buffing
I would like to know how to process a specific rework of cutting through Heavy Acid copper plating during a copper buff that cuts through to the Zinc die-casting. The specific problem is blistering at the exact interface of the copper plate to the Zinc base metal around the entire rim of the cut through.
Bob Campbell- Milwaukee, Wisconsin
2003
To rework exposed zinc a cyanide strike must be used. The copper strike should thicker than the usual copper strike, i.e. about 100 micro inches or more, followed by acid copper plate to the desired thickness for buffing. There will be a thickness difference where the cut through occurred, perhaps it can be made not noticeable by careful buffing.
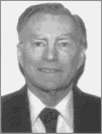
Don Baudrand
Consultant - Poulsbo, Washington
(Don is co-author of "Plating on Plastics" [on Amazon or AbeBooks affil links]
and "Plating ABS Plastics" [on Amazon or eBay or AbeBooks affil links])
2003
At the edge you may be seeing poor results due to an immersion deposit of copper. Keep the preps for the zinc as short as you dare, make sure any acid prep is fairly fresh, and if possible use a shower nozzle hose to wash the area as it is removed from each prep tank. Also try going in "live"(power on and a jumper cable on the rack before immersion to the strike) I use to plate custom chrome on diecast, hate the stuff.
Jon Quirt- Minneapolis, Minnesota
2003
Q, A, or Comment on THIS thread -or- Start a NEW Thread