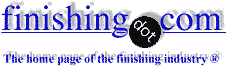
-----
Medium vs. high phoshorous electroless nickel plating
I want to get a wear resistant Electroless Nickel plating on Aluminum. What will be the difference between med phos and high phos pretreatment in my case, please? Which one is better? Is the difference significant or not? What kind of literature can you recommend?
Thank you,
Andrei Tchougounov- Ligonier, Indiana, US
2003
First of two simultaneous responses
Pretreatment is the same for medium or high phosphorous. The medium phos. is harder as plated and can have an as plated hardness of as high as 60 RC without heat treatment.
Todd Osmolski- Charlotte, North Carolina, USA
2003
Second of two simultaneous responses
Mid or high phos as undercoat is really a toss up, however, if EN is the final coating, I'd go with HIGH PHOS as it is more corrosion resistant in most environs, it's more ductile, and less likely to give the plater problems with adhesion. It is slightly more in cost but on aluminum, it's worth the $$.
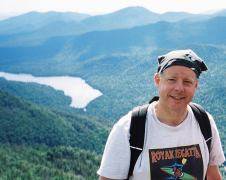
Milt Stevenson, Jr.
Syracuse, New York
2003
For your literature question, get a copy of Electroless Nickel Plating ⇦[this on Amazon affil links] by Wolfgang Riedel. There is a section in that book that deals with your question. From my reading, heat treating helps a great deal and low phos is preferred to high phos.
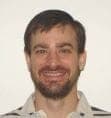
Jon Barrows, MSF, EHSSC
Kansas City
2003
For WEAR resistance the LOW phos EN is recommended and for Corrosion resistance the High phos is recommended.


Sara Michaeli
Tel-Aviv-Yafo, Israel
2003

Q, A, or Comment on THIS thread -or- Start a NEW Thread