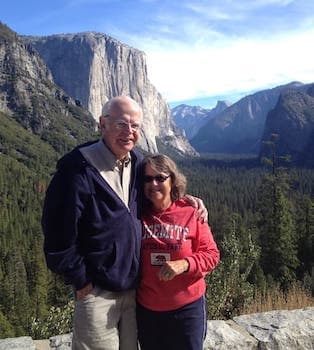
Curated with aloha by
Ted Mooney, P.E. RET
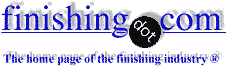
The authoritative public forum
for Metal Finishing 1989-2025
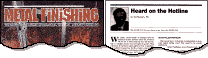
-----
How to qualify a metallic plating-substrate system regarding its diffusion properties?
2003
Dear all,
We want to qualify a new bath (cyanide free) for Ag (or Sn) electroplating on a Cu substrate (electrical device parts). I should mention that this new bath impede the Ni underplating, which is harmful in my opinion. But I need to prove it to people responsible for this project. Furthermore I want to have an in-depth look at the ways of characterizing platings regarding solid-solid diffusion properties. In a first approach, I distinguish two problems at least.
DETERMINING THE CONSTANTS EXPERIMENTALLY
For the case of two semi-infinite media in a planar configuration, the following formula well applies thickness of the "diffusion affected area"= squareroot (diffusionconstant*time).
Temperature enters through the diffusion constant which obeys an Arrhenius law. This provides the basis for a time-temperature correlation. Possibility for this prediction relies on the knowledge of the two constants involved in the Arrhenius law: the pre-exponential factor and the activation energy. Either one trusts values in the tables, if available, or one performs measurements. If one does the latter, one can let the samples in the furnace (inert atmosphere), with different temperatures and/or different times of exposure and then determine the concentration profiles by using a profilometric technique: SIMS or GDS, for what I know. Then, two situations have to be distinguished.
1- The elements are not miscible in every proportion
According (more or less!) to the phase diagram, some new layers are grown. The thickness predicted by the above fundamental formula is the overall thickness of these new layers. In the connector industry, it is this way the growth of intermetallic compounds is mitigated to reasonable low thickness by choosing the mating surfaces according to their diffusion constants and the required "mean" operating temperature during the timelife.
2- The elements are miscible in every proportion (e.g. Cu-Ni
The concentrations of the elements are continuous functions of the distances from the interfaces. Here it is much more tricky. Indeed, experimental curves are noisy or do not look like a "beautiful" theoretical one obtained with simple assumptions. Then fitting them is not straightforward. This is a first problem.
TAKING INTO ACCOUNT THE NON TRIVIAL BOUNDARY CONDITIONS
A second problem, and the most critical in my opinion, is the following: with the case of layers a few microns thick or less on a substrate, the physics is more intricate than with two semi-infinite bodies. However predicting the behavior during the lifetime of the system requires formulas as well as an experimental measurement of the diffusion constants! (Even likely less simple than the fundamental one quoted above!). One faces the first problem also!...
Does someone know guidelines to use diffusion-accelerating assessments and to exploit them for predicting the behavior during the lifetime of a system of a plated metallic substrate? Or may be a simple-minded approach, that is a rough criterion, putting aside any theoretical considerations?
NB: I am aware that diffusion is not the only phenomenon involved in the aging of platings. It is on purpose I put aside corrosion problems on the surface. Diffusion considerations are intended to ensure that the material chosen from corrosion considerations to be on the surface will not be replaced by an other one.
Sincerely yours,
Pierre LAURAT, PhDLEGRAND S.A. - Limoges, Haute-Vienne, FRANCE
2003
Your question is very deep and rather complex, but perhaps a few ideas may help you.
Firstly, many years ago I found that the diffusion of one metal (tin) into another (steel) follows Fick's Third Law of Diffusion. Secondly, I suggest you plate your substrate with a suitable diffusion barrier of known thickness. You could do this with a Hull Cell, so the diffusion barrier thickness will vary across the width of the plate. Then overplate the barrier layer with a known thickness of the diffusing metal. Heat treat the plate under known (and various) conditions and then take metallurgical sections. The distribution of the diffusing metal can then be determined by using EDAX on a convenient Scanning Electron Microscope. This will give you an idea of the effectiveness of the barrier layer and its relationship to temperature. If you repeat the technique with no barrier layer, it will tell you a lot about the kinetics of inter-metallic diffusion. As a rule of thumb, I would not consider a barrier layer to be satisfactory if it is less than 4um thick.
Also, do not believe the diffusion rate is related to the atomic concentration on the surface - when I looked at the Sn-Fe system, I found that whilst there was free tin available on the surface, the only alloy formed was FeSn2, but as soon as the tin had been depleted, the FeSn2 became FeSn, Fe2Sn3 and finally Fe3Sn2, all of them having different rates of formation and activation energies. (This work was never published - perhaps one day I might get round to it!). The whole subject is quite complicated, but great scientific fun.
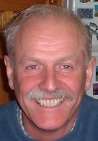
Trevor Crichton
R&D practical scientist
Chesham, Bucks, UK
2003
Trevor,
I agree: it is a complex subject. I guess this is the reason why you have been the only one to risk a reply up to now!
"The effectiveness of the barrier layer and its relationship to temperature" is related to a time of exposure and this is precisely the problem: what is of interest for us is what will really happen during the lifetime at the true temperature of the product.
If I demonstrate that, at a given temperature, an absence of barrier results in intermetallic diffusion and the presence of a barrier avoids that, one can always say: "Right, but the "cumulated" time-temperature effect on the system during its lifetime is by far less than during the heat treatment. So, we do not need a diffusion barrier."
The correlation time-temperature is really the core problem here. And to make it, one needs a solution where both the time and the diffusion constant appear. After that, you feel better because you can always make the assumption of an Arrhenius behaviour for the diffusion constant, even if you do not know precisely the regime: grain boundaries, bulk or surface.
Thickness of a barrier: 4microns
From my own experience, it seems a lot. Between 1micron and 2 microns is usual. Beyond, delamination may occur.
EDAX as a tool
I feel uncomfortable when using EDAX for diffusion studies. The resolution is quite poor. If intermetallic layers are grown, I do not know if it is possible to determine the composition of a layer less than one micron thick. And if the composition is a continuous function of one lateral dimension, you need to do it slab by slab (as thin as possible because you make an average). Problems of resolution again. Do you have some better tricks?
Pierre LAURAT- Limoges, Haute-Vienne, FRANCE
There is a lot to cover here. Firstly, Ficks Law of diffusion is x^n = kT, where x is the diffusion distance, T is the temp and n is the growth law exponent and K is a constant. Hence the rate of growth will be exponential to the temperature. The time-temperature relationship is therefore parabolic for x=2. This will explain why accelerated diffusion testing is valid by increasing the test temperature.
Secondly, I stand by my 4um thickness for a barrier layer. If you are having delamination problems, it is not due to the thickness of the barrier layer because most common metals will be adherent for an electrodeposit of only 4um; I would suggest you have problems with activating its surface and resulting in the loss of adhesion. Using thin barrier layers results in a discontinuous layer, leaving some substrate exposed. I would suggest that your improved adhesion due to a thinner barrier layer is actually due to the top plating adhering to the substrate.
Thirdly, I agree that EDAX is not very precise, but it is widely available. To improve the resolution, you can take a tangential microsection of the substrate/barrier layer/top layer and use a very low beam energy to minimise electron penetration. By taking a tangential section, you magnify the thickness by the tangent of the angle at which you mount the sample. There are other techniques available, such as scanning Auger and ESCA, but both are rather sophisticated and not always readily available. You could also take replica of the tangential section for transmission electron microscopy analysis and at the same time do a bit of X ray crystallography. I am sure other surface analysts could think of other methods.
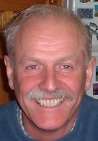
Trevor Crichton
R&D practical scientist
Chesham, Bucks, UK
2003
Q, A, or Comment on THIS thread -or- Start a NEW Thread