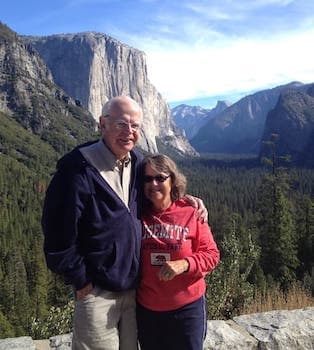
Curated with aloha by
Ted Mooney, P.E. RET
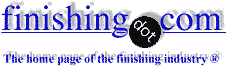
The authoritative public forum
for Metal Finishing 1989-2025
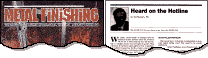
-----
Looking for answers on Phos and Oil
I am looking for information on Phos & Oil as a method for metal finishing. What types of parts most often call out this finish and what types of industry uses this finish as well? Also, what is the cost comparison to zinc plating, e-coating, and powder coating? What limitations exist with using this finish? How much is spent yearly throughout the US and rest of the world on this finish?
Kevin Johnsrud- Brillion, Wisconsin, United States
2003
Phosphate & oil offers only very moderate corrosion protection and is, of course, not dry to the touch. It could be used on machine parts, chain, gears, sprockets, etc. Sometimes it is used for temporary protection. It is probably cheaper than any of the processes you mentioned. You can order the SFMRB Reports from the SFIC group at AESF or NAMF and you will find SOME market data on metal finishes. But detailed information of this sort is not published and can only be obtained by retaining a market specialist to research it for you.
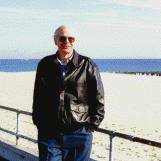
Ted Mooney, P.E.
Striving to live Aloha
finishing.com - Pine Beach, New Jersey
2003
Ted is 100% correct, would like to note 1 additional thing and that is that you can use a "dry touch" oils or lubricants, some will give a slightly longer life.
Chris Snyderplater - Charlotte, North Carolina
2003
Q. Hello All,
We currently zinc phosphate a small gauge steel component, but at the final stage have problems drying our parts to the required dry to touch standard after they have been immersed in DTTO.
We are confident the phosphate is correct with high coating weights and uniform grain structure from abrasive blasting pre-treat. We are happy the oil has emulsified correctly and diluted to the acceptable concentration of 20%.
So far we have tried oven drying, heating the oil at 60 °C when immersing and currently spin drying in a centrifuge. Parts continue to look and feel oily, sticky on the surface and not dry to the touch.
Would application of the oil at room temperature make any difference? Any ideas? would be greatly appreciated
Many thanks
- Birmingham, U.K.
January 14, 2013
A. I might be lazy, but I would switch to a organic solvent based oil that will dry to the touch with no heat, just hanging.
James Watts- Navarre, Florida
January 16, 2013
Q, A, or Comment on THIS thread -or- Start a NEW Thread