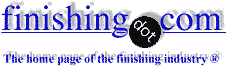
-----
Whitewash on Bright Nickel/Chrome Plated Parts
2003
Q. Good ole false chrome burn or whitewash ... whatever you choose to call it.
We recently did a brightener conversion on our bright nickel plating bath. We do bright nickel and decorative chrome on buffed brass substrates. We have an automated hoist line. Our nickel supplier discontinued the old brightener so we had to change.
Lab testing was done, both at vendors lab and our lab. All lab testing proved successful and all were made based on recommended concentration for this specific bright nickel process. Before conversion we were plating fine. After conversion ... major whitewash over 100% of the parts. A technical assistant came in, reviewed the situation. They felt our rinsing was inadequate (but it was fine before the conversion!). We have always used RO water for our nickel rinses. We learned a long time ago, to monitor and control both nickel content and pH in order to prevent whitewash. Our monitoring and control would no longer work. The Technical person had us rinse the parts down with city water. This alleviated the problem ... not eliminated ... just alleviated ... we went from 100% whitewash to, maybe 25% whitewash.
The defect sometimes is over the entire rack ... sometimes on the top parts only which leads us to believe we have a flash dry on that the RO water won't remove because the brightener is so stubborn to remove.
This whitewash is never visible before chrome, only after chrome. We are able to salvage these parts with the whitewash if we have a good polisher with a light touch. The whitewash will buff out and the nickel never shows through ... we really check for this. By accident, we found that if the bright nickel rectifier is turned off before the parts enter the tank, we let the parts sit for two minutes without current then turn the rectifier on, and up to correct amperage, we see 100% acceptable parts.
WHAT IS GOING ON HERE....WE FEEL SURE IT IS BRIGHTENER/RINSE RELATED. WHAT IS THE CHEMICAL REACTION GOING ON WITHIN, BEFORE, AFTER, OR BETWEEN NICKEL AND CHROME THAT CREATES WHITEWASH?
We are doing okay now, but this type of situation really bugs us! Any info would be appreciated.
Thanks,
Gloria J. Schwedler- Indianapolis, Indiana, USA
A. Hi,
I believe you have some bipolarity in your nickel plating solution. Therefore you will get 100% perfect finish on your part when you turn down the rectifier before you lifting up parts. I also believe you use more than one rack in your nickel solution and this racks gets the current from the same rectifier.
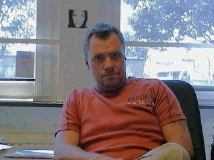
Anders Sundman
4th Generation Surface Engineering
Consultant - Arvika,
Sweden
2003
by George Dubpernell"
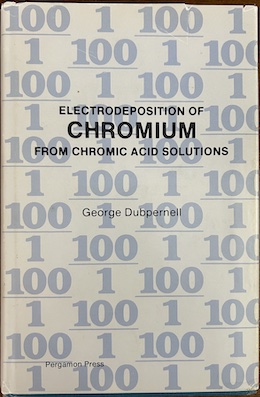
on eBay or Amazon
or AbeBooks
(affil link)
Q. Anders, thanks for your response. We have one station in our bright nickel bath, but each workbar that enters this station may have from one to three racks of parts on the workbar (cathode). This one workbar sits on saddles bolted onto the tank. Both saddles are connected to the same rectifier ... we only have one rectifier for the bright nickel tank.
We had a pow wow a few days ago where we listed all the possible causes for 'whitewash'. Our information came from other electroplaters in our field of finishing, technical data and our own history. The bipolar information I read came from the infamous 'Those Elusive Little Amperes' - V.E. Guernsey. Here it states that if we truly had a bipolar condition it would be seen only on the lower left and right hand corners of our racks, which is not our case. Sometimes it's on 98-100% of the parts and, more often than not, it is only on the top row or two of parts. There is mention that the problem could be 'stray current' rather than a bipolar condition. What's your take on this?
Thanks,
Gloria J. Schwedler [returning]- Indianapolis, Indiana, USA
2003
A. Hello,
Whitewash comes usually from passive bright nickel, or if your rinse water (the last step before chroming) is contaminated with organic break-downs, etc. Sometimes it is helpful to have an activator before chrome plating. The activator just contains a small amount of chromic acid and very low sulfuric acid. In there the passive surface of the nickel, especially bright nickel newer generation, gets reactivated. If you don't have an chrome activator or not enough space to make up one, you can drop down the pH of your last rinse station before going to chrome it.
Do you have an activator before chrome plating? That problem can be caused at too high concentration of nickel and some compounds of electrolyte (such as organic compounds) in your chrome activator. If that shouldn't be your problem than might you have to check your rinsing system after the nickel plating. Also what might can cause the problem if your led anodes are too much covered with lead chromate.
I hope I could help you
Kind regards,
Dominik [last name deleted for privacy by Editor]- Switzerland
2003
A. Dear Mr. Anders,
Please note that Gloria said that she turns the rectifier off BEFORE starting Nickel plating , not AFTER plating. I wonder if the chrome activator should be just immersion or electrolytic type?
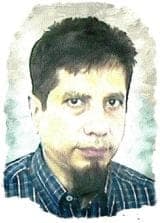
Khozem Vahaanwala
Saify Ind

Bengaluru, Karnataka, India
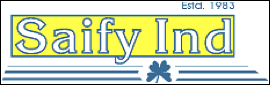
A. Dear Gloria,
The whitewash problem in Bright nickel plating is mainly attributed to the imbalance of the carrier and brightener in the bath. It seems that at the time of conversion to the new brightener system, too much quantity of carrier has been added. Even in the replenishment if the more carrier is used this problem usually appears. Please do not confuse white wash problem with the nickel passivation. It is true that whether whitewash or dull white gray finish will appear only after chrome plating. Do not change anything in your process since all these so called factors like rinse water, bipolarity were already existing before the brightener changeover. Stop adding the carrier and maintain the bath with the brightener till such time you are through with your problem. However, you may also consult your existing supplier.
Wishing You Good Luck,
YASH P. BHALLA- New Delhi, INDIA
2003
A. Gloria,
Yes check the rectifier for right DC current you may have some AC current on different current density.
Khozem has it right. I missed some information you told in the letter. If all electricity connection is okay, maybe your problem could be in the nickel brightener additive, wetting agent. If you have changed your supplier, maybe they have different chemistry which can't work together. So my recommendation is if this is true to clean the nickel solution with cartridge treatment.
Regards,
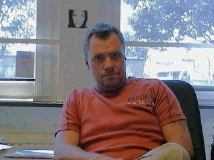
Anders Sundman
4th Generation Surface Engineering
Consultant - Arvika,
Sweden
2003
A. All the above mentioned reasons for white wash or nickel passivation are correct. I think I have seen all of them. The only thing that solves this problem once and forever is an Electrolytic activation prior to the nickel^chrome.


Sara Michaeli
Tel-Aviv-Yafo, Israel
2003
Q. Sara, I am curious. You say electrolytic activation PRIOR to nickel. Is this correct? This would occur BEFORE the nickel plating process? I have had many people say this should be done after the nickel and before the chrome, but this is the first I have heard that electrolytic activation prior to nickel could possibly solve the whitewash problem. You sound very confident that this is the way to solve the whitewash problem. If this is true, I would be interested in learning more about your experience with the problem and your solutions.
Regards,
Gloria J. Schwedler [returning]- Indianapolis, Indiana, USA
2003
A. Sorry, Sorry, Sorry! Of course it is an activation prior to the chrome and not prior to the nickel.


Sara Michaeli
Tel-Aviv-Yafo, Israel
2003
A. In order to activate your nickel plated racks, rinse the rack in the chrome recovery or drag out tank before going into the chrome plating tank. I do agree with most of what has been said here but typically this problem is related to brighteners excessively added to the plating solutions -- so try running them in the lower limit and see how your problem behaves.
Guillermo Luna- Mexico City, Mexico
2003
2003
Q. I truly appreciate all of the response I have received regarding the problem of whitewash. Please see our process listed below. Our line is an automatic. We are running brass substrates which are buffed for bright nickel and brushed for semi-bright nickel. With the exception of the nickel, both buffed and brushed parts see the same tanks.
Our process is currently as follows (rinses, cleaners, and activators/acids use RO water and plating processes use DI water):
* alkaline soak cleaner
* secondary alkaline soak cleaner
* two counterflowing rinse tanks
* electroclean
* two counterflowing rinse tanks
* 3 oz/gal acid salt to remove alkaline residue
* two counterflowing rinse tanks
* one counterflowing rinse tank
* 1% sulfuric acid dip for activation prior to nickel
* two counterflowing rinse tanks
* semi-bright nickel process OR bright nickel process
* After semi-bright three rinses on nickel recovery and after bright nickel process - two rinses on nickel recovery (currently not ran as recovery and using city water due to recent whitewash problems as city water has helped with the problem)
* After the nickel rinses we go into a strong 10 oz/gal activator - ambient and not electrolytic - this is our step to prep for chrome plate
* two counterflowing rinses (only in these rinses for a very short period of time so as not to loose activation)
* Decorative Hex Chrome - once work has sat into the electrolytic saddles we have a delay of about five seconds before the rectifier comes on (we do not enter live). The delay is supposed to act as another activation step.
* We have five counterflowing rinses that follow the chrome plate process.
- Indianapolis, Indiana, USA
A. Gloria,
In my experience almost all the time whitewash (and not chrome burns, they are different) is caused due to a wetter/ carrier out of balance/range. This usually shows up as a rinsing problem. Some Ni brighteners are "indexing" and some are not. It really sounds that the brighteners are not as compatible as first thought; a lot of times problems show up as old brighteners start to be weened out. Some fixes until all old brightener products are out of solution are: adjust pH to 4.2 or a little lower (I like sulfuric better than HCl in this type of problem), this will help the rinsing of the wetter/carrier off of the parts; keep rinse water at room temperature. The cooler the rinse water the less effective rinsing of wetters/carriers. Also if you can do it, let racks sit in Chrome solution for 15 to 30 Seconds before putting current to parts. Movement would also help.
Chris Snyderplater - Charlotte, North Carolina
2003
A. A delay before the rectifier comes on in the chrome plating solution sounds like a passivating act and not an activating one. And by the way, most plating lines do not have three rinses between the semi bright nickel and the bright one. You don't need a rinse between the two nickels at all! It is just trouble to rinse between the nickels.
I don't know what kind of activator do you use prior to the chromium with 10 oz/gal and followed by rinses. The electrolytic activators operate at less than 0.5 oz/gal and again, no rinse before the chrome! Try instead of the activator with two rinses, just to have a short dip in a solution containing 1 oz/dal CrO3 and entering the chrome without any rinse!


Sara Michaeli
Tel-Aviv-Yafo, Israel
2003
Q. Sara, thanks for the information. We are not using a two step nickel process. We use either the semi-bright nickel only or the bright nickel only. We do not plate duplex nickel.
Our 10 oz/gal activator is a proprietary acid salt. We must rinse after this activator as this activator alone has caused us whitewashing problems in the past when we make it fresh.
It sounds like most platers recommend the low concentration chrome pre-dip just before entering the chrome. I know some people recommend using the chrome predip with current and some as immersion only.
At this time, the chrome pre-dip is probably going to be our first choice so I would like to know what are the pro's and con's of current vs. immersion in the chrome pre-dip? If current is best, what is the most common voltage/amperage recommended and length of time?
Thanks again for everyone's input.
Gloria J. Schwedler [returning]- Indianapolis, Indiana, USA
2003
Q. Have been reading the advice on whitewashing and realise that the problems encountered are very similar to ours. We bright nickel and chrome buffed brass and usually have no problems but do occasionally get whitewash that when polished goes through to the nickel, and adding acid to the water nickel rinse gets rid of it. The last whitewash though was different; adding acid to the rinse made it worse. Adjusting all the usual parameters made no difference but turning off the air agitation to the nickel rinse helped a lot, but not rid us of the problem. We have 2 nickel tanks and decided to change the brightener from PPS to the Acetylenic type in one tank only and noticed an immediate improvement in the new brightener i.e. no whitewash with or without air agitation in the nickel rinse. While it is obvious that we now need to convert the remaining tank to the new brightener we would like to know what is happening and why. Our suppliers say they have never experienced this type of problem and cannot explain the difference why the new brightener works and old one does not. I suspect they know more than they are telling. Anyone help?
IAN JAMES- Cheltenham UK
2003
Just a brief follow-up for the white washing problems we were experiencing. Following is what we have done short term to alleviate whitewash and future long term plan.
The brightener levels were out of balance. When we brought one brightener up to par and allowed the other to drop the whitewash problem did not exist.
We still found it necessary to keep the pH of the bright nickel close to or slightly below 4.0. We chose to keep the city water rinses after the bright nickel rather than go back to RO (we tried RO again but some whitewash appeared again). We are using high agitation in these city water rinses and they are counterflowing rinses. We are not adjusting pH in the rinses nor or we adding nickel to the rinses ... the pH maintains near neutral and the nickel content in the rinses are only from the drag over of the nickel bath.
Long Term: We do plan on making changes to include a chrome pre-dip before the chrome plating bath.
Thanks to all for their suggestions, information, and help.
Gloria J. Schwedler [returning]- Indianapolis, Indiana, USA
2003
2003
Thanks for getting back to us, Gloria!
It always nice to read a story that has an ending, rather than to read one only to discover the last chapter missing.
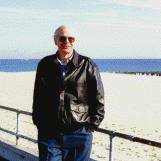
Ted Mooney, P.E.
Striving to live Aloha
finishing.com - Pine Beach, New Jersey
2003
A. Just happened to read the letter Gloria Schwedler wrote. Having been in plating for over 55 years and publishing 4 papers on this related subject, I would like to see if I can shed some light on this subject for those concerned.
First let's state a well known fact:
1) Never try to operate a chrome tank without a live lead; this will neutralize any stray currents and bipolarity. For instructions please read the paper "Those Elusive Little Amperes" for electrical configuration and operating parameters or the newest version "MORE OF Those ELUSIVE ..."
2) Long delays such as you have in the many rinse tanks, an acid activator prior to chrome is a necessity, remember air is a good passivator. Reduce the amount of air being used in your rinse tanks prior to chrome. As an activator I can only suggest, not give something specific: start with 0.5% bv of sulfuric acid, make the part cathodic at about 3-4 volts for approximately 30 seconds to one minute; all parameters may have to be changed since many things in this industry are never certain.
Good Luck. Please contact me if I can be of further help. You might want to read other papers pertaining to this subject such as "Down Under Where The Chrome Don't GO" or the new version of "The Burn That still Burns" and "Strangers in the Tank". If you don't have these articles, let me know I can furnish.
Sincerely,
- Broken Arrow, Oklahoma
Ed. note: It is the website's sad duty to pass along the news that V.E. Guernsey died on March 19, 2007. An obituary can be found in the May 2007 issue of Plating & Surface Finishing.
Q, A, or Comment on THIS thread -or- Start a NEW Thread