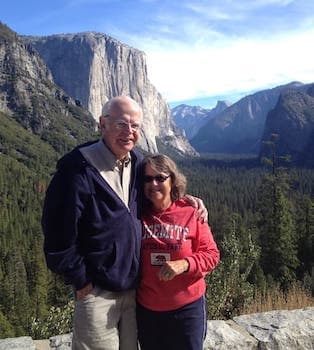
Curated with aloha by
Ted Mooney, P.E. RET
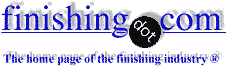
The authoritative public forum
for Metal Finishing 1989-2025
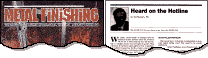
-----
CLEANING HEAT TREATMENT BURN MARKS ON STAINLESS STEEL
2003
Q. Dear Sirs,
We are a Turkish company, processing stainless steel mostly AISI 304. In order to tell you our manufacturing problem I want to tell our production processes first.
Rolls of stainless steel raw material cut by shearing are deep drawn in hydraulic presses. After the hydraulic and deep drawing oils are degreased/cleaned from the surface, the part is heat treated at 900 °C. After heat treatment the part is formed in a hydraulic press.
Formed parts are sent to etching unit (I am not sure whether that is the right name for our process). In this unit what we do is that with strong acids bath (30 lt HNO3 + 500 lt H2O + 15 lt HF) we clean the 900 °C heat treated, burned surface of the parts.
After this process we use electropolishing to have a shiny surface.
My question is: do we have the right composition of above mentioned bath? Is it the appropriate method for AISI 304 stainless steel? The acids we are using are dangerous and we are searching whether we can find alternatives for these mixtures in the name of worker health and work site security.
Thanks to all of you for your concerns.
Aysenur Y [last name deleted for privacy by Editor]- Tuzla, Istanbul, Turkey
A. Hi, Aysenur. It sounds like these are rolled products, not cast products, and thus would not contain silicon. In that case, the HF may not be necessary. But heat treatment scale on stainless steel is very durable stuff that cannot be removed with mild chemicals.
If abrasive removal is not practical and you don't want to use strong acids, the most promising avenue to investigate might be heat treating in a vacuum or inert atmosphere. Good luck, and apologies if this is not help -- I'm from the plating industry, not the heat treatment industry :-)
Regards,
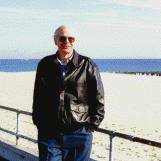
Ted Mooney, P.E.
Striving to live Aloha
finishing.com - Pine Beach, New Jersey
April 17, 2009
Q, A, or Comment on THIS thread -or- Start a NEW Thread