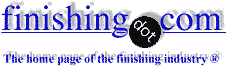
-----
Aux. anode placement and LCDs
2003
Hello all:
I was wondering if there was a way besides using auxiliary anodes to help the plating bath throw better into the LCD areas? Without additives to the basic baths. Can magnetism be used to manipulate the flux lines? I was thinking if a neg. pole of a magnet was set up behind the LCD would it cause more of a field in that area? Or does it have to be connected to the same power supply/source? Also, on the note of aux. anodes.... Are they connected to the same power supply and if they are, how to you gauge how far to place them from the LCD and not burn the area? If you are using another power supply, will there be a danger of the more powerful power supply with higher amperage going into the part feeding back into the smaller one on the aux. anode? or will it not feed back through the NEG on the part being plated?
Thanks, I know these are basic......but so am I! :)
Tom Haltmeyer- Peoria, Arizona, USA!
Auxiliary anodes are usually connected to the same power supply, although it is possible to use a separate power supply.
Two other methods of current distribution are bipolar electrodes and shields. A bipolar electrode is not wired to anything; it is a piece of metal having one end placed close to the area you want to plate and one end placed close to the anodes. What it does is shorten the electrolyte path, and thus the resistance, between the anodes and the LCD area. Ions only have to travel from the anode to one end of the bipolar electrode, plus from the other end of the bipolar anode to the piece you are plating, rather than all the way from the anode to the LCD area. The end near the anode gets plating on it; the end near the LCD area acts as an anode, so you need to be concerned about it dissolving.
Shields are simply inert plastic (PVC or polypropylene) plates that block the short path to the HCD area so that the HCD area is no longer "closer" to the anodes than the LCD area. The ions have to travel a wetted path from the anodes to the plated area. If there is a plastic shield in between, they have to go around the plastic because they can't go through it.
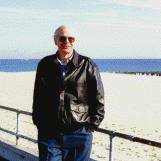
Ted Mooney, P.E.
Striving to live Aloha
finishing.com - Pine Beach, New Jersey
2003
Thanks for the answer Ted: But, it leads to another question.... You say the bipolar anode will dissolve on the end closest to the part. Besides using copper or nickel as a bipolar anode, could titanium be used safely without it dissolving?
Thanks,
Tom Haltmeyer- Peoria Arizona USA
2003
Well, as long as it's not "mission critical", I'd say try it. Titanium is a strange material of construction in a plating bath and it's entirely possible that it will rapidly dissolve (as has been known to happen to titanium heaters that aren't grounded to the anode); but it may last, and it should not contaminate the bath significantly since it's not soluble. Platinum clad titanium is the right answer, but it's quite costly. I'd try the shields first though.
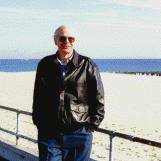
Ted Mooney, P.E.
Striving to live Aloha
finishing.com - Pine Beach, New Jersey
2003
I have had problems with titanium anodes in the past. They have a habit of passivating and developing a high resistance coating, sending the voltage drop through the roof. Platinum coated titanium is much better but much more expensive. Ted is right about using screens, they are the simplest and cheapest way of altering the current density distribution. However, there is another possibility, try using a "robber". This is another cathode located around the areas of high current density; it acts as a sink for the overactive cations heading towards the cathode and also creates electromagnetic repulsion between itself and the working electrode. In doing so, there is a better equipolarisation of the workpiece.
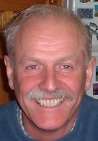
Trevor Crichton
R&D practical scientist
Chesham, Bucks, UK
2003
Thanks for the replies and help. I have been using robbers successfully but it didn't help to throw into the LCDs much and the flat areas would build up quite thick. I'm restoring mostly pitted potmetal parts for cars from the 40s and 50s. I tried out my first shield last night and it worked fantastic. I will continue to use them in the future. This has been a great help and THANKS!
Tom Haltmeyer- Peoria, Arizona, USA
2003
What has not been said is what type of bath is it and what size/shape the part is. I have used 304SS in some baths as a bipolar anode with reasonable success. In another, increased agitation took care of the problem. Shields are best in some cases and robbers can be very effective in some. A very few cases will require all of the methods to get it to work. If it is nasty, preplate with brush plating might be an option. So, it depends on lots of things.
James Watts- Navarre, Florida
2003
Sorry about the details. I have both a 7 gallon and a 25 gallon bath for Bright copper and Bright nickel plating. The copper is the standard acid copper with brighteners/levelers. The nickel is a watts bath with brighteners/levelers.
The shape of the parts vary from round bezels to the big Vs you see on the back of old Cadillacs. The shapes are many and varied on the 40s and 50s cars. But, all are potmetal. I am using a HIGH sulphate NICKEL bath for striking initially and then into the acid copper. Just don't want to deal with cyanide. Most of the LCDs are that areas that the moisture collects and pits the parts so it takes a lot of work in these areas. That's the reason for the aux. anodes in these areas to build them up for solder or sanding prior to the final copper to buff and the nickel. The robbers worked great and I will continue to use them. The aux. anode on a door handle that I set up also worked great for building up in the inside of the handle where you grab it. I will probably continue to use the same metal as a aux. anode as it seems to help the build up with the copper.
Any and all comments are appreciated.
Tom Haltmeyer- Peoria, Arizona, USA
2003
You should also consider using periodic reverse rectification. It has been my experience that once you have optimized the shields, robbers and auxiliary anodes, it is still possible to cut the thickness range variation by 50 percent using PR plus the optimized DC cell design. Main consideration for PR to work is that the bath should be formulated so soluble anodes can be used.
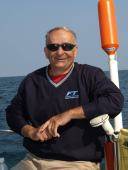
Pat Mentone
St Paul, Minnesota
2003
I would try a "high throw" bright acid copper bath, set-up properly, you won't believe the results.
Russell Richter- Danbury, Connecticut, USA
2003
Platinised titanium expanded mesh will act in this bath with good electrolyte flow.
Vanajambika Jeyakumar- Chennai
2004
Q, A, or Comment on THIS thread -or- Start a NEW Thread