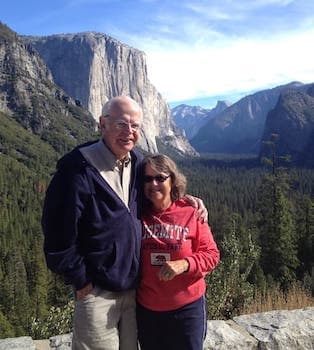
Curated with aloha by
Ted Mooney, P.E. RET
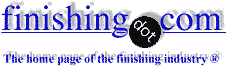
The authoritative public forum
for Metal Finishing 1989-2025
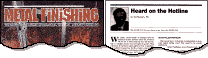
-----
Is copper or nickel flashing a must for good solderability of tin plated steel
Q. We manufacture electrical filters in cold rolled steel boxes. The boxes come from our box (can) vendor electro or Hot tined plated. We are unsure of their process and if they do a copper or nickel flash prior to plating. We have a new second source for plating. But the workers complain that it is very hard to solder unto the boxes from the new plater. We know the new plater is not doing a copper or nickel flash. He is adding some organic stuff to make the tin finish bright. Is it possible that the solderability problems are due to not doing a copper or nickel flash prior to tinning? Are there other factors involved? If flashing is the answer, would this increase the cost of tinning considerably?
Sergio N. Longoria- Austin, Texas
2003
A. I think the principal problem is the brighteners in the tin bath. I think an alkaline tin is easier to solder than a bright acid tin.
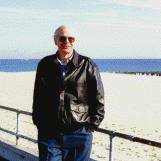
Ted Mooney, P.E.
Striving to live Aloha
finishing.com - Pine Beach, New Jersey
2003
A. If you want solderability, use a matte tin. Organic brighteners in really bright tin make soldering a bitch. Solder as soon as possible after plate. One month old tin plate is a lot harder to solder than 1 week old, even in matte. Can you switch to a more aggressive flux or will that cause even worse problems. I did an experiment on recycling wire connecters that had been on the shelf for aver 3 years. Unfortunately, I do not have the records of it.
James Watts- Navarre, Florida
2003
A. The best way to solder tinplate is to use alkaline tin that has been flow melted. Acid tin will be more likely to have brighteners added and this will make the wettability of the surface quite poor. The "art" to soldering is to have a good wettable surface and hence a low contact angle between the molten solder and the tinplate. Try using a good flux with the solder, or better still, don't let the tinplate age as it develops a tenacious tin oxide layer that must be removed. This can be done by giving it a quick alkaline etch. If the soldering is in a non critical area, try giving it a scrub with mild abrasive.
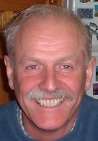
Trevor Crichton
R&D practical scientist
Chesham, Bucks, UK
2003
A. In tin plating if you would like good solderablity you need to keep as little brighteners out and also thin deposits .0001"" or lower. If you need thicker deposits you might want to look at tin/lead deposits.
Chris Snyderplater - Charlotte, North Carolina
2003
Q, A, or Comment on THIS thread -or- Start a NEW Thread