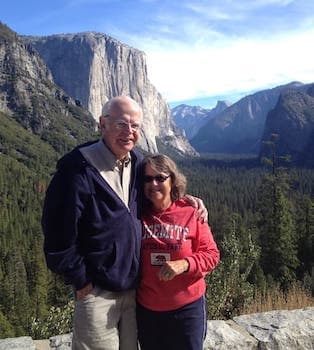
Curated with aloha by
Ted Mooney, P.E. RET
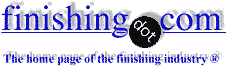
The authoritative public forum
for Metal Finishing 1989-2025
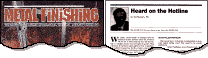
-----
Extend life of phosphate tank chemicals
I am currently working on a project to extend the life of our phosphate tank chemicals. Historically, we dump the tank and re-charge the tank every three weeks. What do we need to consider as variables that affect the life of the phosphating chemicals?
Sue SestinaJackson Tumble Finish - Jackson, Michigan
2003
First, you have to determine what kind of phosphate process you are operating so that you can identify the general chemical nature of the reaction. For example, iron phosphatizing operates on different principles than zinc phosphatizing. Next you need to determine how many stages your system has; if you have a simple 3-stage iron phosphatizing process, contamination from incoming oil may be the primary limiting factor, whereas if you have a 7-stage zinc phosphatizing process, oil and soil may never get as far into the system as the phosphatizing step.
One thing worth investigating is that if you dump the tank every three weeks there may be a reson why, and if you can identify the reason, you've taken the first step towards prolonging its life expectancy.
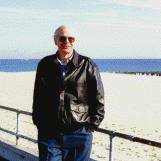
Ted Mooney, P.E.
Striving to live Aloha
finishing.com - Pine Beach, New Jersey
2003
We have managed to extend the life of the phos tank by eight days. We have added additional rinse cycles to the process, however, on the eighth day after the usual time-framed bath change, we have again experienced white dust on the parts. I understand that this is a typical occurrence with zinc phosphate baths, and that the white dust is actually iron.
Are there variables to consider other than high metal throughput; bath temperature; and rinsing cycles, to inhibit the build-up of the iron content?
Also, our zinc phosphate supplier has recommended that we need to change the phosphate bath when the iron content reaches .8. (We use the same supplier's chemicals upstream in the process.) Is this criteria, .8 iron content the industry standard used to determine phos tank change out?
Does introducing a light volume of air into the tank during idle periods have any affect on iron content? Does maintaining a light volume of air flowing into the phos tank, during part processing time have any affect on the iron content?
Thanks,
- Michigan
2003
Dissolved iron is principally precipitated by the accelerators in the formulation (nitrites, peroxide). In some plating operations like acid zinc plating, air agitation is a very necessary component for oxidizing dissolved iron so it precipitates out of the solution, but I don't know whether zinc phosphating baths work the same way.
Sorry, I don't know enough about the process to help you with those questions, but we have many suppliers of zinc phosphatizing baths listed in our Chemicals Directory who can offer a second opinion; plus we have many
"regulars" here who hopefully will read your question and help you.
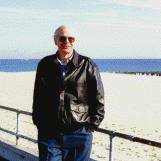
Ted Mooney, P.E.
Striving to live Aloha
finishing.com - Pine Beach, New Jersey
2003
Q, A, or Comment on THIS thread -or- Start a NEW Thread