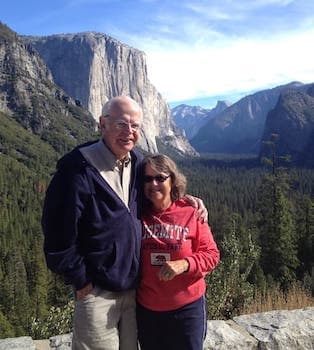
Curated with aloha by
Ted Mooney, P.E. RET
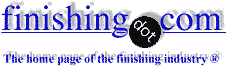
The authoritative public forum
for Metal Finishing 1989-2025
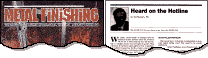
-----
Chromic vs. Sulfuric Anodize
Q. We are looking for some type of characterization of the knockdown in fatigue life that occurs in aluminum parts when subjected to a chromic anodize treatment (MIL-A-8625 / MIL-PRF-8625 [⇦ this spec on DLA], Type I) as opposed to a sulfuric anodize finish (MIL-A-8625, Type II).
A.W. Vaughan1998
A. Hi A.W. I would probably start with the thickness. Chromic acid anodizing reduces the thickness of the substrate by .02 to .4 mils, whereas sulfuric acid anodize reduces it by at least several times as much; plus sulfuric acid anodizing can leave corrosive residues whereas chromic acid does not. However, chromic acid is definitely on the EPA bad list and there is much pressure to supplant its use. Boeing is promoting a boric-sulfuric process, BAC5632, that definitely deserves looking into. Good luck.
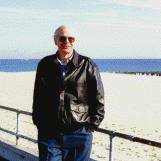
Ted Mooney, P.E.
Striving to live Aloha
finishing.com - Pine Beach, New Jersey
1998
A. There has been some work on fatigue performed primarily with hardcoat, MIL-A-8625 Type III, Sulfuric Films). The evidence seems to show that film thickness is not an issue as coatings between 1-5 mils have been tested.The coating lowers fatigue strength severely at high stress, however low stresses had little influence on fatigue strength. Another interesting factor is the influence dichromate sealing had in reducing fatigue loss, however naturally abrasion resistance was decreased in hardcoat. One of the main factors to be looked at I believe is the difference in physical properties between chromic and sulfuric coatings. The thinner chromic coatings sealed in dichromate are more flexible, more adherent and more dense than sulfuric coatings. This may relate to the fact that fatigue loss is thought to be due to microcracks in the coating. The thicker more porous, less dense sulfuric coatings have a tendency to craze more than chromic coatings. The properties of boric/sulfuric coatings are more closely related to chromic coatings than are sulfuric. Boric/sulfuric is a more forgiving process than chromic, however there is still a requirement for sealing in a dilute hexavalent chrome solution.
Ward Barcafer, CEFaerospace - Wichita, Kansas
1998
! I have found it curious since the onset of the Boric-Sulfuric Process as a replacement for Chromic Acid how the corrosive sulfuric acid was considered a reasonable substitution for Chromic Acid.
I understand that the 700 milligram maxim coating weight produced by the Boric-Sulfuric process affords the fatigue properties of a thin film. I understand environmentally that the Chromic Acid process is more difficult to manage. I do not understand how sulfuric acid is remotely considered for use in areas where danger of acid entrapment exist.
Does the Boric-Sulfuric process exhibit any characteristics that promote its use in lieu of Chromic Acid Anodize?
In MIL-A-8625 / MIL-PRF-8625 [⇦ this spec on DLA] it is stated that Type IC is a non-chromic acid anodizing, for use as a non-chromate alternative for Type I and IB coating. It is my understanding that this Type IC was a category that was inserted as a vehicle for the inclusion of the Boric-Sulfuric process that is a Boeing process.
Joe Hillockanodizing shop - Philadelphia, Pennsylvania
1998
1998
Agreed, Joe -- youre not the only one to notice this. Certainly sulfuric acid should not be used on spot welded assemblies, rolled seams, etc., which could trap solution.
I agree with the thrust of what I think you are saying, i.e., that substitutions can be very dangerous because we can forget that there was often more than one reason why a particular process was originally selected. While we must not back away from substitution of less toxic finishes in place of more toxic ones, in our hunger to solve an environmental problem we may be tempted to turn a deaf ear to other concerns.
opinion! One reason I object to the never-ending flood of repetitive government grants for studies of substitutes for toxic materials in the finishing industry is that after 24 years of mindless repetition, although they produce nothing new, they do constitute a deafening drumbeat drowning out all else, and impelling engineers & finishers towards ignoring product utility & safety issues.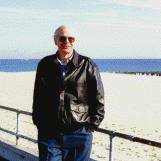
Ted Mooney, P.E.
Striving to live Aloha
finishing.com - Pine Beach, New Jersey
Q. The idea that type II (sulfuric) creates a fatigue resistance debit for reasons beyond the thickness increase over type I is of interest to me. As the Engineering Manager for a small aircraft component manufacturing firm, I have several products that I (send out for) anodize. Like everyone else, I am under pressure to steer away from chromic anodizing (by the rising cost and the threat of export regulation). I have read that the dichromate seal mitigiated the type II fatigue strength loss "somewhat", but I have not been able to find anyone to quantify that for me. Likewise, the stress environments that might make this a concern. For example, I have a small hinge used to attach control surfaces on Cessnas. It is 6064 AL and I am toying with the idea of going with Type I because I can not be sure how the stress of this particular application rates. I suppose I could set up a test, but that would take a while. Some of the less stressful applications (such as seat rails), I am specifying dichromate seal and letting it go at that. I have never used the boric-sulfuric, but I have read of it.
Jeff Brockaviation components - Kansas City, Missouri
February 6, 2008
Multiple threads merged: please forgive chronology errors and repetition 🙂
Boeing BAC5632 Boric-Sulfuric Acid Anodizing
Q. I'm looking for information about boric-sulfuric anodizing process. I'm working for a major company and I would like to submit an alternate to them for the chromic-acid anodize that we are doing now. any information would be helpful.
ken neuts1998
A. Ken,
It is my understanding that Boeing actually patented Boric-sulfuric. Try to get your hands on the Boeing spec {BAC5632 I believe it is}. I'm an anodizer and can give you more detailed technical info.
We get excellent salt spray results and excellent paint adhesion. Our coating weight is 500-600 mg/ft2. I've found bath maintenance a little tricky at times but I'm sure that's to be expected from any over-worked, underpaid bath.
At its base, the spec. calls for a 3-5 minute ramp time, followed by 21 minutes anodize at 15 volts. Occasionally after that we do a hot chrome DI seal for 26 minutes.
Good luck,
James A. Corier1998
A. Let's not forget that Boeing does have a patent on the boric-sulfuric process, and because of that fact, to legally use it you need to obtain a license from Boeing or a vendor who might be promoting the process for Boeing. I recently saw an ad in one of the finishing magazines for a vendor who is promoting it, but I don't remember the magazine or the company. If you are an approved Boeing sub-contractor, obtaining the license should be easy.
There has been some recent data published where some claim that the boric acid is not necessary. I don't know if there are any patents on anodizing with a straight 5% sulfuric acid solution using the processing sequence of the boric-sulfuric process.
Phil Johnson
- Madison Heights, Michigan
1998
Q. My question is simple: where can I find this magazine concerning the finishing treatments that everybody is talking about -- I would especially like to have it sent to my shop for further evaluation and reference -- thanks
ken neuts [returning]1998
Fungus growth in Boric/Sulfuric
Q. Hello all,
I am having a problem with fungus in my anodize tanks and rinses. At first the fungus started in the Boric/Sulfuric anodize. Now I am seeing the fungus in my chromic anodize rinses. I know that Sodium Benzoate can be used to kill the fungus in the boric. Can it also be used in the chromic rinses? Also where is the fungus coming from? How much Sodium Benzoate do I need to use in a 2200 gallon tank? Is it something that I will have to add consistently to the tank? So many questions!
Please enlighten me,
Randy A.Mattson- Auburn, Washington
2003
A. I used to have fungus problems in the past with the same types of solutions you have described. I have found the only way to control fungus buildup, was to use constant carbon filtration and sometimes followed by a .2 micron filter. I am sure that there are better methods than this. I have heard that a small amount of methanol [affil links] added to the sulfuric anodize bath also helps prior to carbon filtration.
Brian A. BeaubienEMF Corp. - Rancho Cordova, California, USA
2003
A. A few other comments about BSAA for what it is worth.
It has been used successfully since the early 90s for an alternative to CCA for corrosion protection, paint adhesion and fatigue reduction but it should not be used where there is a chance of trapped electrolyte including certain part geometries, recesses, laps crevices, weldments, etc).
BSAA is more energy efficient than chrome based processes (lower temperature, lower voltage [15V], 20 minutes [less time than CCA]). A dilute chromate seal is used in lieu of a hot DI seal. A hot DI seal works but is not as robust. Materials of construction are 316L Stainless Steel. You will not need the Hexchrome Scrubber though or the compliance issues to deal with for the anodize tank.
The seal tank is less than 75 ppm Cr(VI).
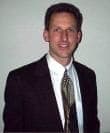
Steve Anzelc PE Lead AP
Kansas City, Missouri
July 8, 2008
Selecting cathode material for Boric/Sulfuric anodize
Q. We are a finishing job shop serving the aerospace industry. Our anodize processes include Chromic and Sulfuric anodize.
We recently setup a Boric/Sulfuric anodize process. I cannot find any info on what is the material to use as cathodes in the Boric/Sulfuric tank. We use lead cathodes in our Chromic tank and aluminum in our Sulfuric tank.
Anyone have any experience with the Boric/Sulfuric process as to what material is best to use as cathodes in the tank.
process manager - Denton, Texas, USA
August 26, 2010
A. Either one is fine for boric-sulfuric or chromic, you just have to make sure that the thickness is proper for the current-carrying. I prefer stainless for environmental reasons.
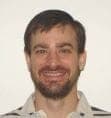
Jon Barrows, MSF, EHSSC
Independence, Missouri
August 30, 2010
Q. I am looking for literature on Boric Sulfuric Anodizing. I have already read "Aluminium How To" by R.H. Probert. Great book but I need technical information on Boric Sulfuric Anodizing.
Thank-you,
Finishing shop - Rincon, Georgia, USA
August 2, 2017
A. Hi Micheline. I don't think you're going to find a book that covers it. But in addition to this thread, letter 41155 has a lot of good info. Also you should probably try to get a copy of BAC5632, and take a look at www.boeingsuppliers.com/environmental/chromic.html
Luck and Regards,
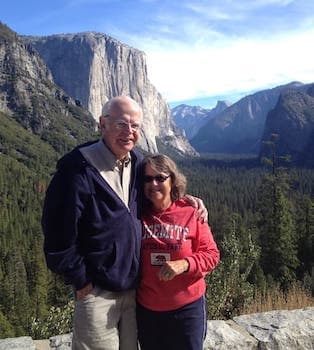
Ted Mooney, P.E. RET
Striving to live Aloha
finishing.com - Pine Beach, New Jersey
August 2017
Q, A, or Comment on THIS thread -or- Start a NEW Thread