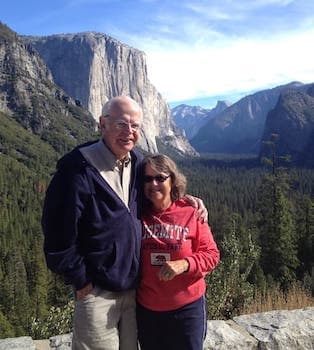
Curated with aloha by
Ted Mooney, P.E. RET
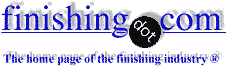
The authoritative public forum
for Metal Finishing 1989-2025
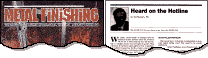
-----
Porous Hard Anodize.
We have a part, Aluminum 7075T651. Spec. is hard Anodize, .003" min. Part is stress relieved and pre-lapped. During final lapping after approx. 3 microns is removed, porosity shows up and is granular. It appears "chalk like". The more we lap, the worse it gets. Any ideas?
Bud Kincaid- San Jose, California
1998
1998
Bud,
I believe something wrong with the anodic coating on your parts. As a hard coating, it is difficult to remove by conventional lapping. The 3mil hard coating on 7075 should be quite dark rather than chalk like. Although anodic coatings are porous oxide films, pores are so small that you can not see them visually unless you use an electron microscopic instrument. You can imagine how tiny the pores are since there are about 400 billion pores per square inch.
It is not clear what kind of process you used to anodize that part. If the part sit in anodizing tank too long, the coating could become soft and chalky. Besides, if an inproper sealing pretreatment was applied, the coating could also turn to be soft and chalky.
Ling
Ling Hao- Grand Rapids, Michigan
Bud:
The military specification calls for a coating thickness of .0018 - .0024". .003" is too heavy a coating and could become what we refer to as smokey. Ling is correct in stating that the coating can become soft at .003". One other thought is that if the temperature in the hardcoat tank rose, results like you are experiencing could happen.
Regards,
Bob BramsonB&M Finishers / Prismatic Stainless Steel

Kenilworth, New Jersey
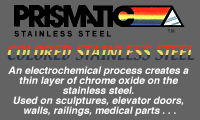
1998
1998
I'm not sure what you mean by stress relieving. To a plater stress relieving can be heating plated steel parts to 375 F to free absorbed hydrogen. Hopefully you're not heating parts that high, because the integrity of the coating would probably be destroyed.
I agree with Ling that it sounds like you have a soft coating.
You can hardcoat to.003" or higher, but special attention needs to be paid to a variety of parameters, where at .002" one might get away with some cheating. Here are some tips: (pardon me if you know or are doing any of these)
1. Pay strict attention to agitation, and if not already doing it, consider using work-bar agitation, and don't just depend on air to keep parts cool. To get a good hardcoat parts must be within a few degrees of bath temperature. I'm assuming yoyr tank can maintain temperature with a full load in the tank.
2 Pay strict attention to current density and accurate calculations of surface area of the parts and racks. Make sure buss bars and racks can carry the desired current without heating up.
3. Use aluminum racking, using the old rule of thumb of 20 amps per contact point. I used to use titanium racking for hardcoat, but never for coatings higher than .002". Use a rack which will build up a coating at a rate similar to the 7075. If the rack anodizes faster than the parts, it will build up a high resistance, and toward the end of the cycle the parts will draw higher current than desired, leading to increase of part temperature. If possible, use bolt-on contacts rather than spring clips, which can be lifted up as the coating grows.
4. Use additives in the hardcoat. Straight sulfuric will work better than many people will admit for .002" coatings, but for thicker coatings additives will help.
5. This is a capital expenditure, but the best thing the shop I worked at to improve the quality and tank efficiency of hardcoat was to install a pulse-current rectifier. Near the end of my job shop days we were helping a customer salvage parts with .005- .006" coatings, which are probably not possible with straight DC. We also eliminated work-bar agitation and used titanium spring clips for almost all conventional (.002") hardcoat. For heavy coatings we still practiced all of the above #1-4.
Phil Johnson
- Madison Heights, Michigan
Q, A, or Comment on THIS thread -or- Start a NEW Thread