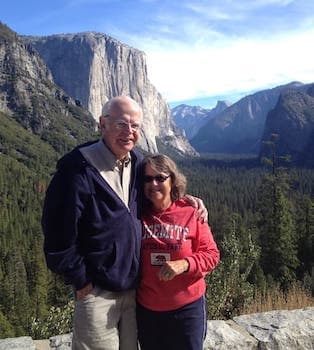
Curated with aloha by
Ted Mooney, P.E. RET
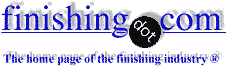
The authoritative public forum
for Metal Finishing 1989-2025
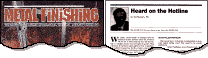
-----
ENIG (Electroless nickel / immersion gold) & ENAG Plating: Problems & Solutions

Q. Good day to all experts.
- I am currently trying out some different ENIGEG processes on glass-to-metal sealing products.
- I used medium p EN, then immersion gold and electroless gold plating, and the results were great.
- Is it possible to plate ENIG using High-P EN with good adhesion and wire bonding?
- I tried using high p EN but the adhesion was not good (tape test) and found some unplated areas.
- If so, any special treatments or chemicals needed to be used.
- I plan to be electroless throughout.
- Singapore
September 5, 2023
⇩ Related postings, oldest first ⇩
Q. I am looking for a brief description of processing and potential problems for immersion nickel and immersion gold. We are a manufacturer of printed circuit boards and have a need to install this process for one of our customers.
Thank you,
Jim MoritzES&D, Inc
1996
A. I have never heard of "immersion nickel", do you mean electroless nickel and electroless gold?
The Canning Handbook [on
eBay,
Amazon,
AbeBooks affil links] p. 640-641 is pretty brief on immersion gilding of gold:
1. hang the articles on 24 swg copper wire.
2. clean in the usual way ( ! ! )
3. well rinse in a swill.
4. cyanide dip, 50 g/l KOH, cold
5. "most neutral and acid gold solutions, if used hot, will produce an immersion deposit on copper nickel or brass", but the author cautions that the bath will become contaminated with the displaced base metal, and thus should not be used again in electroplating.
Note: I would check with some suppliers of gold plating solutions for further information. I just bought my 'Canning Handbook' at Sur/Fin '96 Cleveland last week -- I've always wanted one, and look, I'm using it already.
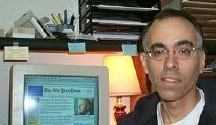

Tom Pullizzi
Falls Township, Pennsylvania
A. Jim,
I agree with Tom, never heard of immersion nickel, but there is immersion gold real easy to use, watch the adhesion though. Try Technic in R.I., ask for Ormerse.
Good luck,
David Guleserian- Rhode Island
A. Electroless Nickel-Immersion Gold is a popular finish in Europe to replace hot-air leveled solder, (HALS). Most of the major chemical suppliers have the process very well defined. Any of them can supply the whole process.
Richard Zuendt- Garfield, New Jersey
1996
ENIG vs. ENAG
Q. Electroless gold users, what are some of the problems you have experienced using an electroless gold process?
Back some years ago, the early baths produced a deposit with terrible adhesion. Is this still a problem with the latest generation of Electroless Gold baths?
Bob S [last name deleted for privacy by Editor]New Brunswick, New Jersey
1998
Q. I am evaluating the quality and reliability of two plating processes used in PCB manufacturing specifically at the plating process:
* What is the difference between Electroless Ni Immersion Au versus Electroless Ni Autocatalytic Au plating processes?
* What is the process flow and chemistry differences?
* What are the end result quality differences?
* What are the surface morphology differences?
laminate PCB user - Warren, New Jersey, USA
2004
A. Filmore: I'm a little out of the loop on progress in ENAG, but the biggest advantage of the autocatalytic process is that the thickness is not limited because you can build gold-on-gold rather than the operation coming to a halt as soon as no more nickel is exposed.
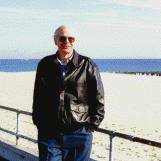
Ted Mooney, P.E.
Striving to live Aloha
finishing.com - Pine Beach, New Jersey
Multiple threads merged: please forgive chronology errors and repetition 🙂
Skip Plating Problem
Q. Our company faces a serious skip plating issue with ENIG finishes. The skip plating all happened on isolated pad of BGA with no line connected. Need your help. Thanks.
Philo Youngelectronics - Shanghai, China
2003
A. Hello,
I have experienced this issue a lot. There is a lot you can do to minimize this problem: The most common reason for this to occur is that you have micro-etch solution remaining in the holes. If one BGA pad is somehow connected to this hole it will skip. Even if the contact is through an inner layer. The actions you might take are:
1. Make sure you don't have SM residues in the holes (helps trapping solution).
2. Make a horizontal micro-etch outside the line (if the equipment is vertical); it improves rinsing of the holes.
3. Improve rinsing in the vertical line with heated rinses and vibrators in the rinses after the micro-etch.
4. Increase time in the activator (to make sure even the small surfaces is activated.
5. Increase activity in the Ni-bath, by lowering the stab.
6. Increase surface in the bath with dummies. Most important again, check the rinsing of the holes.
ReCoV - Sweden
2003
A. This will be happen because in MASK you did not open small hole then it Si will be fully filled, a sort of mix of air and solder mask is in the hole. Then you do Ni/Au and the air in the hole will get bigger, due to heat, and push the SM out of the hole SM is coming onto a SMD-pad and on that place there will be no gold and this is called skip plating.
Vipul Desaijob - gandhinagar,Gujarat, India
April 13, 2013
Can't Pass Solderability Test after Steam Aging
Q. Hello,
I need some help about ENIG thickness requirements for Steam age testing. (Solderability - after exposing to steam for 8 hrs).
My base layer is Silver and is coated with 100 - 150 µin. of EN (7% P) and my final finish is 3 µin. of Immersion Gold. The parts pass solderability test before steam aging. After steam aging we observe de-wetting of solder on the surface.
My Question is, What is the failure mechanism? What is the minimum thickness of gold I should apply. Unfortunately I cannot go for electrolytic process due to the nature of the component. Is there a way to solve the problem without going for a thick gold using Electroless Gold? Does EN thickness play a role? Thanks for your help in advance.
Karthik Thambiduraielectronic components - Norwood, Massachusetts
2004
A. Steam aging causes oxidation of the 7% P electroless nickel under-layer. It is very difficult to pass steam-aging using immersion gold. However, I have succeeded by using a high phosphorus Electroless nickel (it is more corrosion resistant) and long times in the immersion gold. The gold does not build thickness, it only covers the nickel by chemical replacement. The nickel should be active before using immersion gold. Very short rinse (but thorough), short transfer time to the gold (before oxidation can occur), and longer time in the gold solution.
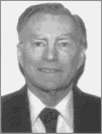
Don Baudrand
Consultant - Poulsbo, Washington
(Don is co-author of "Plating on Plastics" [on Amazon or AbeBooks affil links]
and "Plating ABS Plastics" [on Amazon or eBay or AbeBooks affil links])
Q. Hello Don,
Thanks for your input. I will try High Phosphorous Nickel on some samples and put them for steam age.
I have a few more questions. Won't longer duration of EN Parts in Immersion Gold bath lead to Black Pads? And also High-Phosphorous is not good for soldering -- what is your experience on that.
Thanks
Karthik Thambiduraielectronic components - Norwood, Massachusetts
Ed. note: Ed. note: Soldering issues with electroless nickel are the subject of many other threads on the site; Don Baudrand discusses it on thread 34791 for one.
Black spots on pads. Is rework possible?
Q. We are in the manufacture of PCBs with ENIG plating .
Recently we have experienced black spots on large size pads of 12 mm and 16 mm in Finished Board.
Question : How to remove this tarnishing . If we do any rework on ENIG, is it reliable ?
ECIL - Hyderabad India
2005
A. Haragopal: I'm just the website operator not an ENIG expert, but if an area must be reworked, it would seem that you could use brush electroplating of gold; you might contact brush plating suppliers about that. But a good first step is to try to determine at what point in the process the black spots first appear.
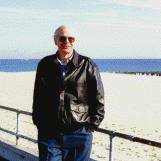
Ted Mooney, P.E.
Striving to live Aloha
finishing.com - Pine Beach, New Jersey
2005
ENIG on PCBs vs. on Silicon Wafer Pads
Q. We have started to use the ENIG process to plate Nickel (3 µm thickness over the copper pad) then followed by immersion gold layer (~500 Angstrom thick) to protect the nickel layer bond pad. We encountered a few technical challenges dealing with this process as we have seen multiple defects such as black bond pad, skip plating, delamination of pad after mounting on PCB board and more. What are the key differences in term of ENIG control when we use it to plate on the Silicon wafer pad versus PCB board ENIG plate?
Edward Ng- San Jose, California, USA
March 27, 2012
Need cyanide-free non-toxic ENIG
Q. I want to ask a question: "I work on Electroless/Immersion Ni & Au plating. Since cyanide is very toxic, is there any option on chemicals for the process which is cyanide-free, and of course not more toxic?" Thank you very much for your advise.
Wymen Lee- GeorgeTown, Penang, Malaysia
2002
A. Electroless nickel is cyanide free. It it usually based on hypophosphite or borohydride.
It isn't quite clear to me whether you electroplate gold onto the electroless nickel or if you are talking about an autocatalytic electroless gold process or an immersion gold process. Cyanide-free golds based on other complexes are available.
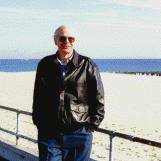
Ted Mooney, P.E.
Striving to live Aloha
finishing.com - Pine Beach, New Jersey
Q. Thank you very much Mr.Mooney. Yes, it's autocatalytic immersion gold onto the electroless plated nickel surface. I've surf some page and found some information regarding cyanide-free gold plating. What I've found there somebody said the substitute complex is more complicated to treat the solution before effluent to environment. Any comments on this?
Thanks again.
Wymen Lee [returning]- GeorgeTown, Penang, Malaysia
A. I don't know exactly what the complexing agent is, but yes, it probably requires some sort of "chelate breaker" chemistry. Remember that not much gold will dissolve in a simple alkali or acid and requires some complexer that probably will not allow metals to drop out via simple pH adjustment. But I suspect that for waste treatment the gold can be easily plated out or removed by ion exchange, and the complexing agent then destroyed/deactivated/occupied with a simple metal like iron, aluminum, or calcium. The water treatment is probably not a big deal.
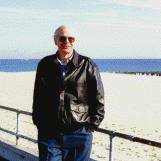
Ted Mooney, P.E.
Striving to live Aloha
finishing.com - Pine Beach, New Jersey
A. Electroless Nickel followed by electroless Gold or immersion gold is now very common in both the semiconductor industry and the printed circuit industry. In many cases the newer technology does not use a cyanide type gold. The use of a variety of sulfite type gold solutions is now common.
Louis HirbourAnaheim, California, USA
Q. I currently have wafers with electronic die that get an ENIG finish applied to the aluminum pads. This process is done with an outside vendor. We have had two problems that keep on occurring. I'm looking for answers, information, or directions on where to look for the cause. Any assistance would be appreciated.
1. There have been times where the ENIG process will selectively etch through the aluminum in small spots, but the rest of it will still be 2.0-2.3 µm thick (nominally 2.5 before the ENIG process). The aluminum clean is a very dilute (~0.02 mol/L). The zincation process, which we do a two step zincation, is about 25% NaOH. Is anyone aware of what would allow the process to selectively etch through the aluminum in select spots but not in others? The picture with the round pad shows some of this pitting after ENIG. They show up as shadowed areas on the microscope. Cross sections show nickel plated entirely in the void of the aluminum.
2. We are constantly dealing with rough ENIG. It comes and goes. We have made several changes to the ENIG process but have been unable to get rid of it. I've also attached images of this problem. One is the view under the microscope at 5x. The other is a 50x confocal scan of the surface to show what the roughness looks like. It appears to be irregularities in the nickel grain. What causes this type of appearance? What do we need to control better?
I appreciate any input. Thank you.
- Salt Lake City, Utah, USA
July 30, 2013
![]() |
A. If you filter your EN bath, I seriously do not think that it is the problem. - Navarre, Florida A. I do not see the photographs but it seems to me that the process is completely out of control. You need a process map and work on C&E. An Ishikawa Diagram wouldn't hurt either. Quick fix - change vendor. Long fix - make sure the zincate is in good condition and it should be mixed prior to use. Also, I suspect the problem is pre-treatment, specifically, poor drag-out and rinsing. When there are small pads like that, you have to use excellent rinsing and drag-out techniques. The double zincate is a good idea but you also might try moving the parts about a bit while in the bath. You shouldn't have to deal with this, get a new vendor, but be sure to inspect your parts at the same magnifications prior and after plating because if you are giving your vendor bad items you can't blame them. ![]() Blake Kneedler Feather Hollow Eng. - Stockton, California |
photos added Aug. 2
Q. In regards to the zincation solution, I believe the reason for the high caustic is to get some surface roughening for better adhesion, but the reaction is limited once the zinc plates over. I know I have read about both acid and base zincation solutions. Most of the time we only see 0.2 µm removal of the aluminum. I was wondering if anyone had seen anything similar. I don't know why the pictures haven't posted.
What I would really like to know is what could be causing sporadic rough ENIG. This has been an off and on problem and process mapping never seems to produce answers. Hopefully the pictures will help.
- Salt Lake City, Utah, USA
Ed. note:Pictures are posted now. Sorry for the delay.
Q. On the subject of my rough samples, I recently found articles that talk about Phosphorus content of the nickel and it's affects on nickel grain sizes. Specifically, above about 10.5% w/w of phosphorus the nickel becomes more amorphous. There was some mention that higher phosphorus was also better for soldering. Are these observations seen in industry? If so, what is the best method for measuring the weight percent of phosphorus in the metal. What is a good P concentration to have in the nickel that would be robust to fluctuations in the process. I appreciate any insight or advice.
David Kissick [returning]- Salt Lake City, Utah, USA
A. David,
Low phos. works best for soldering (1-3%). High phos. is not recommended for soldering.
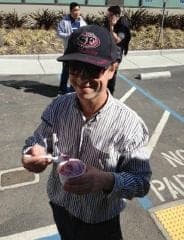
Blake Kneedler
Feather Hollow Eng. - Stockton, California
Porosity in Gold Plating
Q. Hello all,
What is the suitable bath composition, current density or electroplating method for gold electroplating on nickel? The gold must be very thin (100 nm) for good solderability with indium and there will be very low porosity.
Thanks to everybody
material engineer - ANKARA, Turkey
September 10, 2013
A. Hello Yasin,
There are pure gold plating solutions with grain refiners that offer low porosity and excellent solder ability on the market, and have been for years. Your best bet is to contact a supplier of precious metals for electroplating. Tell them what kind of part you are plating and they can help you. Good Luck!
Process Engineer - Mesa, Arizona, USA
Q. Hello I just want to ask a question. Regarding ENIG a problem that we experiencing frequently is increase in current during nickel plating. That resulted to plate out. Normally we never encounter this problem and the bath is new. What do you think the cause of sudden increase of current?
rhodora l.buenaventura- muntinlupa city, Philippines
October 26, 2015
A. Hi Rhodora,
Possible causes as below:
1. Stainless steel rod (cathode) heavily plated with Ni without strip off regularly.
2. Stainless steel rod and tank wrongly connected to rectifier (rod accidentally become anode with tank become cathode).
3. Stainless steel rod too close to tank or rod tip accidentally hit tank wall due to basket movement.
4. EN bath too active due to chemical (Ni, hypo, etc) or operating parameter (pH, temp, etc.) out of control.
5. Poor filtration.
6. Plating article accidentally drop inside the tank.
Regards,
David
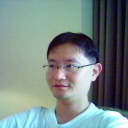
David Shiu
- Singapore
Q. Dear all,
I'm an engineer of ENIG process.
Currently I found serious problem about skip plating on small pad (round dia. 0.3 & 0.5 mm)
I've tried many items such improve cleaning, improve catalyst efficiency, EN efficiency but still not solve yet.
Does anyone have better idea to solve this issue?
Thanks in advance.
- BKK, Thailand
July 20, 2016
? Hi Kawin. Can you comment a bit more specifically on the skip-plating suggestions from Peter Fogel and Vipul Desai?
Regards,
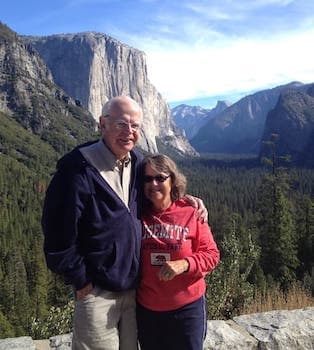
Ted Mooney, P.E. RET
Striving to live Aloha
finishing.com - Pine Beach, New Jersey
![]() |
Q. Dear Ted,
Since our product is flex board, we don't use SM in our process.
2. Make a horizontal micro-etch outside the line (if the equipment is vertical); it improves rinsing of the holes.
I've tried already but it still can not solved. (Outline micro-etch around 1.5 microns)
3. Improve rinsing in the vertical line with heated rinses and vibrators in the rinses after the micro-etch.
After micro-etch I already increased fresh feed rate of rinsing water and we also have acid activation and another rinse water between micro-etch and catalyst zone.
4. Increase time in the activator (to make sure even the small surfaces is activated.
We can't increase time in activator because limit of machine, anyway I've tried to increase temperature and concentration instead but still can not solved.
5. Increase activity in the Ni-bath, by lowering the stab.
Already but still can not solve.
6. Increase surface in the bath with dummies. Most important again, check the rinsing of the holes.
Already but still can not solve. Kawin N. [returning] - BKK, Thailand A. Hi Kawin, ![]() David Shiu - Singapore |
(you are on the 1st page of the thread) Next page >
Q, A, or Comment on THIS thread -or- Start a NEW Thread