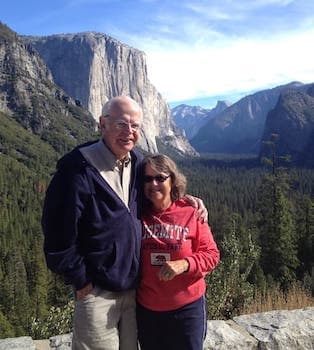
Curated with aloha by
Ted Mooney, P.E. RET
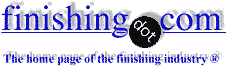
The authoritative public forum
for Metal Finishing 1989-2025
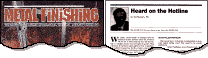
-----
Thermal de-burring of aluminum parts with hardcoat
2003
We are in the business of manufacturing many small intricate parts. Many of them are manifolds, (6061T6 aluminum) with various crossholes, intersecting holes that can easily hide small burrs. Our parts range from approximately 1.5 inches by 2.0 inches to 8 inches by 3 inches. The holes range in diameter from 1/16 to one inch. Alot of these holes are threaded ports. Many of our manifolds are hardcoated (light hardcoat 0.005 growth/penetration) and Teflon impregnated before machining. The local thermal de-burring vendor (using and explosion chamber) we used to de-burr these parts did a tremendous job. The application of these manifolds requires them to be burr and chip free. A single loose burr is devastating to the final product in use.
About a year ago, we had a third occurrence of batches of parts that came back from the de-burring process so badly scorched they could not be used. The scorching was visible and could not be removed physically or chemically. The parts were scrapped for the visual appearance they had. I worked with our vendor to no avail in trying to determine what caused the scorching and how to control it. The last several orders of parts that were scrapped due to this condition was devastating. We looked at coolant used, cleaning methods used, thickness of hardcoat, and anything else at the time we could think of that may have caused this. Since we were unsuccessful in determining the cause of the scorching, and since risk of loosing entire orders to this condition was great, we went back to deburring the parts by hand. this is time consuming, and we have failed in making sure that there are no burrs. I would like to thermally de-burr the parts again, but don't want the scorching issue.
With that introduction, I have two questions. Does anyone have a suggestion as to what would cause the scorching, and how to avoid it. The process is very effective in eliminating burrs, but I have no assurance with the vendor we have used that they can eliminate the scorching altogether. We need this done (explosion de-burring) east of the Mississippi
Betty Romanin- Amherst, Ohio
First of all, I suggest you get in touch with the manufacturer of the equipment. It sounds as if you are getting an incomplete mixing of the fuel or too much fuel resulting in at least a prolonged burn. In either case, there is some fine tuning required here.
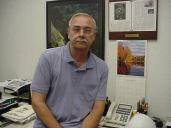
AF Kenton
retired business owner - Hatboro, Pennsylvania
2003
An alternative for small intricate parts is the sPINner magnetic de-burring machine. It uses a pin media driven by magnets below the tank. There is no damaging of parts to worry about, time cycles are no longer than 20 minutes, and with small parts you can do hundreds at a time. We use it here at our company and it knocked out our polishing stage as well since it accomplishes that too. Nothing but positives here.
Kyle Davis- Indianapolis, Indiana
2005
Q, A, or Comment on THIS thread -or- Start a NEW Thread