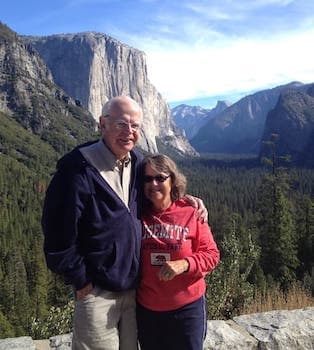
Curated with aloha by
Ted Mooney, P.E. RET
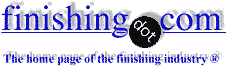
The authoritative public forum
for Metal Finishing 1989-2025
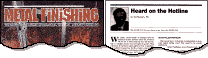
-----
Dry sliding of Electroless Nickel + Ptfe for a precision sliding-block
2003
Dear Sir,
I am working to develop an automatic machine that print rolls of paper with subsequent rolls of different colors. Often the paper is used in alimentary packages. Oil and lubricants like MoS2 coatings are not allowed in that position. I have parts in dry sliding contact, a sliding block. Now they are made of Nitralloy, nitrided, polished down to 0,05 Ra, but the solution is not acceptable, allowing only some hours of life, with severe wear, also adhesive wear. The parts are sliding with a relative speed of 1,5 m/s and a load of 30 N/mm^2. The alignment is not perfect, so I must consider a localized running-in wear of 10 micron for each piece, without a complete destruction of coating. This means that, at the beginning of running in, loads may be also twice that the nominal one, and that the thickness of the coating should be more than 10 microns, hopefully 20-30 micron. In some condition drop of water solution can reach the sliding block. I was thinking about Electroless Nickel+PTFE without temperature coating, for both parts, one against the other. Is there somebody that can advise me about this choice or propose other solutions? It will be helpful to get wear rate datas (also indicative) because I must also estimate the life of this component, because it is critical for the "timing" of different colors printing: after 30-35 micron of total wear of both components the colors will be relatively misplaced and the sliding block will be substituted. Somebody knows which is the thickness of coating and the kind of base material that allows the better anchorage ? Somebody knows which is the tangential stress that this coating can withstand? Please, note that I am working on a prototype, already built, so there is not room for a drastic change in design! (Help!)
Thank you in advance and best regards.
Mario Antonio Morselli- Modena, Italy
Your choice is correct. EN plus teflon against same will show the smallest friction coefficient (around 0.1 initial 0.2 final) and the longest life. Reports compare 8,000,000 cycles against 30,000 cycles for anodized aluminum. Also EN+PTFE against Cr steel showed 40 times the wear. Heat treating the composite showed a slight reduction of properties but experience dictates this treatment for improved adhesion, specially in high point load applications.
Guillermo MarrufoMonterrey, NL, Mexico
2003
Many thanks to Mr. Guillermo Marrufo.
Best Regards.
Mario Antonio Morselli- Italy
2003
Q, A, or Comment on THIS thread -or- Start a NEW Thread