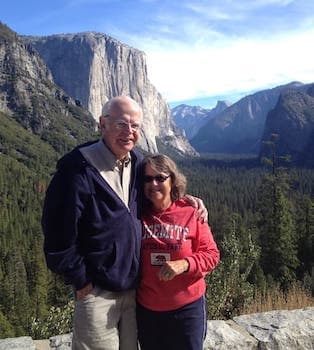
Curated with aloha by
Ted Mooney, P.E. RET
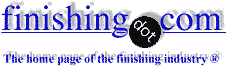
The authoritative public forum
for Metal Finishing 1989-2025
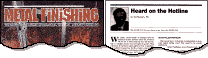
-----
Really need help with surface prep for anodized parts
2003
I am having a problem with a local plating house (sorry for the long email).
We had them etch and clear anodize some extremely expensive aluminum parts about 2 months ago. They turned out pretty well, and everyone was happy. Prior to sending the parts to the plater, we sanded the visible surfaces to 600 grit (per their instruction). This left very fine visible scratches. However, the etch smoothed this out well, and the parts look good.
Well, we sent another batch of identical parts to them last week. When I got them back today, all of the fine scratches created during final sanding were still visible. I assumed that either they hadn't been etched, or the etch was too short. When I pointed this out to them, they claimed that they did etch the parts the same way they did the time before.
They pulled out the documentation on our previous (good) batch, and discovered that they had added a light bead-blast step prior to etching that they had forgotten this time. I was completely surprised (and pissed-off), since we had not specified a bead-blast. Ever. They never told us they were going to bead-blast. In fact, we specifically did not want a bead blast because some of the walls in the part are .019" thick, and we were sure that bead blasting would cause serious warpage.
They are sticking to their guns, and claiming that they did the bead blast, it didn't cause warping, and that they have to do it again to get the same finish (after stripping the parts, of course).
These parts are irreplaceable, and I don't know what to do. Should I trust them, that they can bead blast the parts without causing warpage? Or should I go to another plating house?
Shouldn't the etch remove all of the surface scratches left over from 600 grit sanding?
I would really appreciate some advice. I know virtually nothing about the anodizing process (although I'm learning fast - the hard way)
Thanks,
Craig Lawrence- Palo Alto, California, USA
2003
Without more detail I do not want to tell you what to do, but I do want to tell you what not to do.
Be sure the 600 grit sanding medium is designated (limited) for aluminum only. If someone on the night shift uses the same media on steel or brass, then it will subsequently become imbedded in the aluminum surface and hence require even more etching.
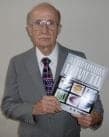
Robert H Probert
Robert H Probert Technical Services

Garner, North Carolina
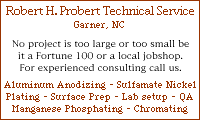
DEAR Craig,
I am wondering why your anodizer is not familiar of long life etch with ability to create satin finish on aluminum. Commercial product for matte finish on aluminum should be available in US. They are used in combination with caustic .The grit are used for aluminum alloys of high Si.indeed casting.
Hadi Khosravi- Tehran, Iran
2003
2003
I am in the process of doing an experiment on some 6061 aluminum because of possibly having the same problem-we had parts with a .442 +.001-.000 diameter that lost .004 from the I.D. during blue anodize operation-our plater claims he did not strip/re-plate them or leave them in the tank too long and remove material-he said there was a violent reaction in one of his dip tanks and suggested the surface may have been effected with a scotchbrite that was used on steel. So I made test blocks with a perfect .500 dia. and numbered them-scrubbed one set with 00 steel wool ⇦ this on eBay or Amazon [affil links] -another with emery paper that we scrubbed on steel first, and another that is raw bar stock. We have sent one block of each to two different anodizing vendors for plating. It sounds a little crazy but it gets the question answered.
Greg Freeborn- Guilford, Connecticut, USA
Q, A, or Comment on THIS thread -or- Start a NEW Thread