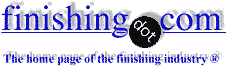
-----
Reducing the required dip time for black chromate
Q. Looking for help with black chromate over zinc ran on an automatic machine. Are there black chromates around where the dip times can be held around 30 seconds? The proprietary chromates I have seen require about a 90 second dip time, which requires the machine to be slowed down. I was told that silver-free blacks have less dip times, but I have no experience with these. Does anyone know if this if accurate, and if there are reliable silver-free black chromates ? Since silver-free blacks are so uncommon in my experience, I am guessing there are problems with them.
Thank You
- Jefferson, Missouri
2003
A. The alternative that I am more familiar with is black chromating of zinc-iron alloy. Once the iron is in there in the plating, silver-free black chromating becomes easier and more practical.
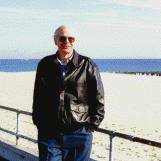
Ted Mooney, P.E.
Striving to live Aloha
finishing.com - Pine Beach, New Jersey
2003
A. You can have a workable dip time of 45 seconds with a silver hexavalent black chromate. Have plenty of silver nearby for additions. It will also require regular checking of pH. That means hourly. Temperature should be maintained at 80-85 degrees. Being done routinely. 30 seconds creates headaches, inconsistent results. It could be done. In my experience it is not worth the aggravation.
There is a working production non-silver black available? Maybe tri-valent? That equals color & corrosion protection? Meets automotive specs? LET US KNOW, PLEASE.
- Grand Rapids, Michigan
2003
A. Using olive drab and black dye can give more reliability and better corrosion resistance than the silver blacks.
To keep dip times fast with silver based chromates you must introduce strict controls and the thing that effects speed most is pH, keep as low as practicable and check at least twice daily. Also warm bath and maintain at a constant temperature as this also keeps more silver in solution
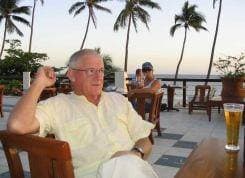
Geoffrey Whitelaw
- Port Melbourne, Australia
2003
A. Just a thought. When measuring immersion time (or cycle time) you need to include transfer time. This is the time necessary to remove the part from the chromate, drain and immerse in the first rinse. Often, this is forgotten leading to a variety of chromate problems or use of over-concentrated solutions. When you figure in transfer time, I bet you do have 45 seconds in your chromate. BTW On the subject of trivalent blacks for zinc plate (not alloy plate) the ones that I am aware of only work on alkaline zinc.
process supplier - Great Neck, New York
2003
Q, A, or Comment on THIS thread -or- Start a NEW Thread