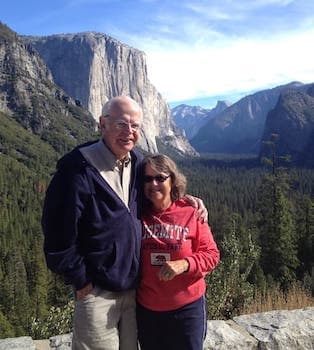
Curated with aloha by
Ted Mooney, P.E. RET
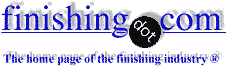
The authoritative public forum
for Metal Finishing 1989-2025
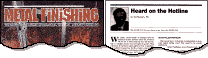
-----
Reducing the stress in cobalt alloy plating
2003
I have an application that may require the use of stress reducers in a cobalt alloy plating bath (low pH, temp of 130F-150F) to obtain a compressive stress. I have couple of questions before I proceed:
(1) What type of reducers are out there that work in cobalt solutions? Are they similar to the nickel baths, such as saccharin or napthalene trisulfonic acid, or is the range more limited? (I don't mind any hardness increase).
(2) I am not familiar with the operation of a bright plating bath. How do you control the breakdown and replenishment of the stress reducing agents - example, is carbon filtration continuous or periodic? I am assuming that a contractometer or equivalent is used to determine the approximate magnitude of stress.
(3) How does the answer(s) to question #2 change with the use of insoluble anodes?
- Renton, Washington
You say alloy, so what is the other metal and percentages.
Russell Richter- Danbury, Connecticut, USA
2003
by William Safranek
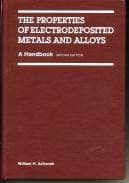
on eBay or
AbeBooks
or Amazon
(affil links)
Due to the highly technical work that you seem to be doing, I would recommend you to get a book like "Properties of electrodeposited metals and alloys" by W. Safranek .
Guillermo MarrufoMonterrey, NL, Mexico
2003
Alloying agent is a nonmetallic at about 15-20 weight %, so it is primarily a cobalt plate.
Yes I do possess the book and have reviewed the data in it. I asked the question here to get information from people like yourself who do real-world applications that are not done in beakers, especially question #2 which requires maintaining a bath longer than a week. Forgive the sarcasm (I am a researcher too), but if I got money for each research project that could never work in a manufacturing environment I would be rich.
- Renton, Washington
2003
Bright plating is a whole different story to what you are doing but when doing bright barrel plating (which is the highest drag out and contaminant situation) carbon filtration is recommended at least semi-annually. When doing rack manual plating or in certain situations you normally don't do it only unless Hull cell indicates so.
Guillermo MarrufoMonterrey, NL, Mexico
2003
Nickel and cobalt are extremely close to each other. Nearly anything that applies to nickel control will normally apply to cobalt control. Brightener breakdown elimination will normally be done by periodic carbon treatment, unless you have a very rare requirement that would require continuous. Insoluble anodes in a sulfamate bath will cause the internal stress to go from tensile to compressive. In a sulphate bath I would assume that is less drastic, but not cost effective as salts, purified , cost more than anodes do, oz for oz of metal ions. Using insoluble anodes for internal anodes or throw assistance can be very useful and hopefully controllable.
James Watts- Navarre, Florida
2003
James, you have kind of confirmed my original guess - thanks. I still want to clarify some things. Nickel and cobalt are indeed similar, but the plated forms are completely different. Cobalt plated out of a sulfamate bath is brittle and pitted, even with typical surface tension agents (learned this the hard way a few years back). The plating structure is also different. Does this mean the incorporation of sulfur in the plating will have similar or different results? Regarding carbon treatment - can I run a PP filter with a changeout to a carbon filter on a periodic basis, or should the carbon filter be run continuously, or do I need to use pack carbon treatment on a periodic basis? How do the breakdown products of these compounds change the stress in nickel over time? Are some agents better than others (less detrimental breakdown products)? My goal is to obtain a compressive stress (range) and maybe increased hardness, and maintain these limits over time in real tanks (50-2000 gal), not just a beaker. And yes - the goal is to use insoluble anodes for auxiliary anodes and to maintain a consistent metal content (cobalt chips aren't cheap). So far they have worked great.
Mike Ware- Renton, Washington
2003
Mike,
Cobalt plating is not as easy as nickel plating despite what the books say. I agree the electrochemistry of nickel and cobalt should be very similar, but they are actually quite different. Firstly, cobalt exists in both alpha and beta forms; the alpha form is hexagonal close packed and is not usually deposited in an electrochemical cell. However, the beta form is face centered cubic and is the preferred form. If deposited at over 70C, it is claimed that the deposit will be beta, but below that it is a mixture of alpha and beta. This will obviously cause a high degree of stress in the deposit. The addition of some brighteners are claimed to promote an all-beta form, but there is little actual commercial evidence for that! Not only will the deposit be stressed, but cobalt is inherently brittle, as you have seen. I agree with your idea that a sulphamate bath should proffer a reduced stress deposit when compared with a sulphate or chloride bath, but the overriding problem is the nature of the deposit. I have read somewhere on this website that, unlike nickel, you do not need to use sulfur enriched anodes to achieve good dissolution without chloride ions, so this may contribute to reducing the stress problem. Unfortunately, the brighteners and additives used with nickel do not appear to work as well, if at all, with cobalt, so you cannot rely on nickel based systems as your guide. Saccharin, for example has very little effect on cobalt; I do not know about NTSA.
Another problem with cobalt is that it exists as Co3+ as well as Co2+; this can be generated at the anode, so there is an immediate process problem here. The effects of Co3+ are unclear, but it is generally assumed that it induces stress and this may be why cobalt baths suffer from a deterioration over a relatively short period of time. Furthermore, an increase in Co3+ will adversely affect the deposition efficiency. The use of insoluble anodes will make these effects more prevalent. Carbon treatment is all very good if you are removing organics, but I doubt very much that it will have any effect on inorganics such as cobalt - give it a go, but I wouldn't bet may months pay on its success.
Finally, cobalt is deposited preferentially to nickel because it has a less stable intermediate complex with water; this complex forms during the cathodic reduction reactions of Co2+ to Co(0). Saying all this, I am very interested in this thread and hope someone can shed some useful practical light on how to make a successful bright and low stress cobalt bath!
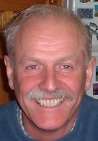
Trevor Crichton
R&D practical scientist
Chesham, Bucks, UK
2003
First of two simultaneous responses --
I suggest using cobalt chloride, as outlined in Lowenheim's "Electroplating" →
Cobalt chloride 90-105 g/L Boric acid 60 G/L. pH 2.5-3.5, Temp 55C. No other plating solution will tolerate insoluble anodes. (except combination of cobalt sulphate and chloride with high chloride) Anode reactions from insoluble anodes create sulfur containing compounds that co deposit, causing extreme brittleness, and non satisfactory deposits as you experienced using a sulfamate solution. sulphate is prone to this also if chlorides are low. the cobalt deposit from the all chloride solution will have tensile stress. Adding organic stress reducers can lower the stress but will result in more brittle deposits.
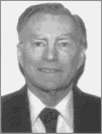
Don Baudrand
Consultant - Poulsbo, Washington
(Don is co-author of "Plating on Plastics" [on Amazon or AbeBooks affil links]
and "Plating ABS Plastics" [on Amazon or eBay or AbeBooks affil links])
2003
Second of two simultaneous responses --
You mention that ...the brighteners and additives used with nickel do not appear to work as well, if at all, with cobalt, so you cannot rely on nickel based systems as your guide. Saccharin, for example has very little effect on cobalt." Where did you get this information? Who did the research? If you read Safranek, there are several references that state that saccharin does reduce the stress. I don't know what to think. I tend to agree with you that it should behave differently. I am hoping that the sulfur can reduce the stress, but I just need to find the right compound so it will end up in the deposit. If not, then I am in trouble.
Mike Ware- Renton, Washington
2003
If you look in Lowenheim, he mentions numerous additives, but it is not always clear as to whether he is talking about cobalt or cobalt alloys. Furthermore, he is not always clear about what alloys he is discussing, so you have to go back to the original texts. Saccharin is passingly mentioned as an additive, but no specific details are given. From personal experience, I can say that saccharin does not have any significant effect on cobalt deposits, although it can be beneficial with nickel-cobalt. I cannot readily recall having come across any references specific to cobalt and saccharin, but I wouldn't expect a paper to have a title saying "The non-effect of saccharin on cobalt electrodeposition", but there may be some throw-away comment in a paper discussing cobalt alloys. One suggestion has been formamide and I have found this to be beneficial. As far as stress in pure cobalt is concerned, I would suggest a good possible approach may be to look for grain refiners to overcome the disruptions caused by the co-deposition of alpha and beta phases. By the way, why must you use cobalt - won't nickel or some other better understood metal do the job for you?
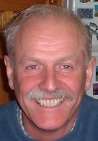
Trevor Crichton
R&D practical scientist
Chesham, Bucks, UK
2003
I do agree saccharin could reduce the stress for cobalt deposition. Without saccharin, it is hard to get uniform cobalt coating. And some literature said, the root cause of saccharin as a stress reducing agent is due to the sulfur incorporation of coating layer.
No I am doing the work of Mn-Co co-deposition!
WVU - Morgantown, West Virginia, USA
2007
If cobalt behaves anything like chromium, you might like to try pulsed current plating. I have found this very effective for putting chromium down under compressive stress, with the normal cracking completely suppressed, even in thick layers.
With repeated thermal cycling no cracks appeared in the plating of sample parts. The pulsed plating current approach may give you another handle to the problem.
- São Paulo, SP, Brazil
January 2, 2008
Q, A, or Comment on THIS thread -or- Start a NEW Thread