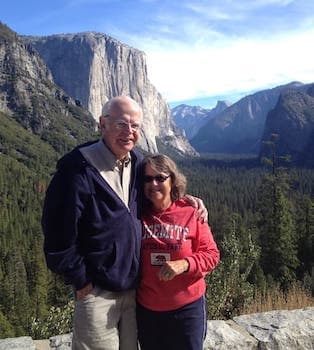
Curated with aloha by
Ted Mooney, P.E. RET
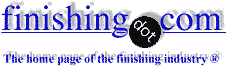
The authoritative public forum
for Metal Finishing 1989-2025
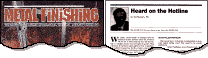
-----
4 categorizations of ring alloy types
2003
Hi all,
Continuing the idea from the previous posting (the central problem being plating quality)...
From my knowledge of castings and coatings, I would believe there exist four categories separate categories of rings based on their constituent alloys and coatings:
1) Cast, malleable precious alloys- Gold alloy (e.g. Gold-Copper-Silver-Zinc based); Platinum alloys (e.g. Platinum-Silver based). No platings are needed when the metals in platinum family or right level and when percent of gold/copper/silver mix.
2) Cast, malleable, plated precious alloys. Expensive White Gold
(Gold alloy with Palladium, not Nickel). Additional plating desired to improve finish and durability but not to protect color or prevent reactions.
3) Cast, nonmalleable, non-plated precious allows- (e.g Gold with Nickel not Palladium). Sufficiently think Rhodium platings improve color (no transparency) and resistance to Nickel reaction. And very thick, high quality platings endure.
4) Cast, nonmalleable, plated non precious alloys (e.g. Nickel-Copper-Zinc or similar) with very thick, quality platings to prevent skin reactions. Balfour/Josten's employ proprietary quality assurance designs and processes to achieve high effectiveness and high reliability, thereby making non-precious rings wearer safe and long-lasting.
Apparently, the categories involving, especially Rhodium plating on Nickel-based substrate (2), represent majority of reporting issues concerning see-through and wear-through. Further, these are problems of plating rather than casting or melding.
I recommend that alternatives for finishing such categories of rings be developed. The highest quality metals are not finished by plating. Taking the examples of metal parts for mass manufactured consumer apparel, such as gold watches and eye-glass frames, these are plasma coated and/or sputtered instead of plated for more uniform coatings.
Since White Gold is less malleable anyway, I conclude the problem is transiting the finishing step from goldsmiths to technical labs specifically designed for plasma and/or sputtering techniques. I recognize that moving such a centralized process would increase the quality and, hopefully duration of finishes. In addition, central sputtering would save tremendous cost due to the relative efficiency and cleanliness of plasma) and recycling of materials in near vacuum. Alternatively, centralized plating would benefit from many efficiencies as well. However, the separation of goldsmithing from coatings has the drawbacks of additional time and expense that may dissuade general adoption or hinder public acceptance. Category 2 rings should be phased out because the Nickel reduces value of precious metals. Category 4 rings are mass production item and accepted as such. For everyone not willing to incur additional cost and effort for plating (or coating) requirements of category 3 rings, I recommend staying with category 1 rings and purchasing the kind of precious metal within available budget- either gold, platinum, (or even palladium if that's feasible). If anyone has questions regarding these issues, please contact me. Otherwise, post for others to read.
- San Francisco, California
2003
Ya know, this is funny, or at least ironic. I've written repeated editorials going back as far as 1997 on the subject of the plating industry's myopic focus on environmental resistance, and its failure to take public pro-active positions on important consumer issues like nickel allergies, and gold & rhodium plating standards for jewelry.
And now here we are with Mr. Potter's otherwise extremely knowledgable presentation, which contains the understandable error of asserting that plating is a low quality technology, such that consumer problems would be resolved by switching to sputtering or plasma. But actually, it's complete nonsense and almost the opposite of the truth: When GM decided to sputter the exterior brightwork of Chevy Vegas in the 1970s instead of chrome plating it (as was done long before, and ever since), it was a fiasco they'd like to forget because it didn't compare to chrome plating in durability. Interior automotive brightwork is vacuum metallized and it wears off, whereas the exterior brightwork is chrome plated and lasts decades under environmental and wear conditions a hundred times worse. High quality, incredibly high density circuit boards in today's smart phones and computers are all made by electroplating; the IC industry recently switched from aluminum sputter fabrication to copper electroplated fabrication for better circuits, not for poorer ones. The wear components in tooling and engines are electroplated. The most intricate printheads and micromachines are all made by electroplating.
from Electrochimica Acta, Vol. 42, nos 20---- by L.T. Romankiw
In a sense, though, he is correct. Poor plating of rings and heirlooms has delivered heartache to millions of disgusted consumers. Can we realistically demand their sympathy and understanding that "plating is better than that" when we in the industry have done nothing, and are doing nothing, to help protect them from shoddy plating practices that we know continue to disillusion and victimize consumers thousands of times every week? Plating needs to be done to rigorous documented standards by electroplaters in modern factories, not by a jeweler working in a teacup on the corner of a desk, working by eye.
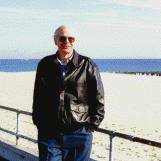
Ted Mooney, P.E.
Striving to live Aloha
finishing.com - Pine Beach, New Jersey
Q, A, or Comment on THIS thread -or- Start a NEW Thread