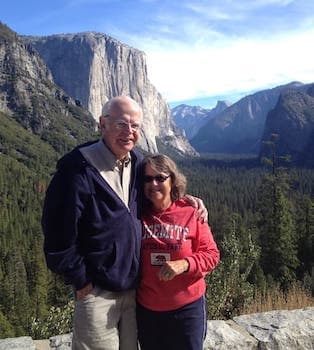
Curated with aloha by
Ted Mooney, P.E. RET
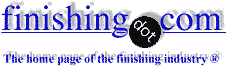
The authoritative public forum
for Metal Finishing 1989-2025
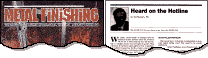
-----
Weld before MIL-C-5541/ chromate/ Iridite/ Alodine/ chemfilm or after?
Q. I am designing an electronics enclosure that is made up of spot welded aluminum (5052-H/32). Should the detail parts be chem coated (MIL-C-5541) class 3 prior to spot welding?
Larry Meadows- Sarasota, Florida
2003
A. Hi Larry!
Yeah, I'd go for that. I prefer coating the individual parts rather than the assembly.

Lee Gearhart
metallurgist - E. Aurora, New York
2003
![]() |
"Surface properties of Conversion Coated Aluminum"
by Raj & Ali ![]() on AbeBooks or eBay or Amazon (affil links) A. I would prefer conversion coating after spot welding due to the heat affected zone. Doug Hahn- Masn, Ohio 2003 A. This is a lose-lose situation. If you weld thru the chromate, you will have a lousy looking weld. If you weld and then chemically process, you have problems with chemicals wicking out from the seams that are tack or spot welded. Also shape can make processing a pain and the extra handling will cost more.Try a couple both ways and take the one that works for you. James Watts- Navarre, Florida 2003 A. Welding is fusing of two metals together. If you've got a chromate on the surface, you've got a barrier separating the two metals you're looking to join. Having chromate there first will always result in a weaker weld joint. If this was simple resistance spot welding, the pull strength of the resulting joint would be far less than expected. Any plater worth his salt can chem film (i.e. MIL-C-5541) a welded assembly without too much solution entrapment and resulting bleed out. Yeah it's nice to finish sub-assemblies prior to assembly, however, sometimes it just isn't advisable. This is one man's opinion only, I've been known to have been wrong before! ![]() Milt Stevenson, Jr. Syracuse, New York 2003 |
I was taught to always call an item which consists solely of metal that is welded together a "weldment", never an "assembly". And while people certainly don't have to agree to use my terminology, I think some of the "disagreement" here is simply that some people interpret the word "assembly" differently than others.
There appears to be a difference of opinion here about whether chromating before welding makes for better or worse welds--but I think that everyone and his brother agrees that things should be chromated before bolting together an "assembly".
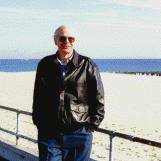
Ted Mooney, P.E.
Striving to live Aloha
finishing.com - Pine Beach, New Jersey
2003
A. Many mil spec QC folks will not agree with Ted's comment. They want the actual weld chromated also. Have done thousands of them. Spot welds or stitch welds are much harder to do than a good full weld. Milt is correct that any good shop can do it. There are some not so good shops out there also.
James Watts- Navarre, Florida
2003
A. I didn't think that's what I said, James -- it's certainly not what I meant :-)
I think things are always supposed to be chromated before bolting them together, but usually chromated after welding them together.
Regards,
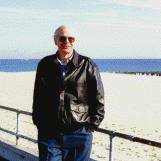
Ted Mooney, P.E.
Striving to live Aloha
finishing.com - Pine Beach, New Jersey
A. First bring the pieces in and deoxidize them in a chromated type deoxidizer. Chromate deox ahead of spotwelding will (1) increase the life of the electrodes, (2) cause a stronger joint (3) prevent or at least retard the amount of weld scale.
Then after the part has been spot welded and returned for "aluminum chromate" stay out of the alkali. Clean in a phosphoric-detergent type product, do not alkali etch, deox in the acid deox of your choice. By preventing alkali you are reducing the salt build-up near the weld and allowing the aluminum chromate to be more uniform and more corrosion resistant. By avoiding alkali you reduce the bleed-out of mixed salts.
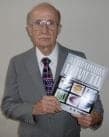
Robert H Probert
Robert H Probert Technical Services

Garner, North Carolina
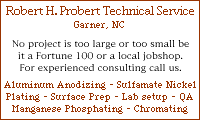
2003
A. Thanks Robert. That sounds perfect!
Readers: Please also see thread 12517, "Aluminum Welding issues: Iridite, Alodine, Chem-Film, Chromate Conversion Coating"
Regards,
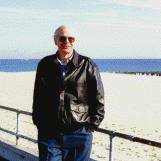
Ted Mooney, P.E.
Striving to live Aloha
finishing.com - Pine Beach, New Jersey

Q, A, or Comment on THIS thread -or- Start a NEW Thread