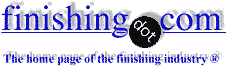
-----
Practically possible to 100% eliminate pinholes?
Q. I'm experimenting with a Megger as a way to electrically verify the absence of pinholes in organic coatings on aluminum. The coated sample is dipped into a water bath and the Megger leads are attached to an uncoated part of the sample and to a conductor immersed in the water. The Megger is a hand cranked instrument that applies up to
1,000 VDC, depending how fast one cranks, and measures the current flowing through the leads and displays the load resistance. Like with any ohmmeter, the applied voltage must be large enough so that a minimum, measurable current is produced. Thus the relatively high voltages, and as one might expect, very thin layers of the coating break down because of the impressed voltage. Sparks and bubbles can sometimes be observed coming from breaks in the coating. Importantly, for the coatings I'm experimenting with (polyurethane), the dielectric strength is high enough so that a properly applied coating of specified thickness (several mils) does not break down. My goal is to produce coatings with zero pinholes, of course, but even more stringent, the coatings need to have some minimum thickness everywhere - 100 % - so that no breakdown occurs in the detection process. Is this an impossible goal, practically speaking? Is it
*possible* to apply any organic coating no more than several mils thick with zero pinholes? Are there other, better, pinhole finding techniques? I haven't tried the Tinker and Rasor Holiday testers, but they do not seem suitable for such detailed examination of small parts (the aluminum pieces are thin pieces about one foot by six inches). I could be wrong.
I'd appreciate suggestions and hearing about other experiences by other members of this forum.
Thanks in advance.
- Princeton Junction, NJ
2003
A common cause of pin-holeing is the shrinkage of coatings that are less than 100% solids as they dry. Practical elimination involves applying multiple coats. Each coat has pinholes, but the probability that pinholes from each coat will line up and provide a path to the substrate diminishes with each additional coat. Determination of practical limit is an empirical process -- as far as the best test, I don't know.
Michel Moninger- Sarasota, Florida
2003
Q, A, or Comment on THIS thread -or- Start a NEW Thread