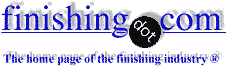
-----
Improve Hard Chrome Plating Corrosion Resistance
Q. One of our clients is doing micro-cracked hard chrome plating on mild steel front fork tubes of two wheelers. The thickness is around 18 - 22 microns. The crack density is around 1000 - 1100 cracks / linear cm. The corrosion resistance obtained is a rating of 8 after 16 hrs CASS [ASTM B368] test. We require higher resistance. What kind of pre-treatment / post treatment will increase the corrosion resistance up to 50 hrs CASS test (without using any kind of undercoats)? Does the crack density have a bearing on the CASS test hours?
Vijaykumar [last name deleted for privacy by Editor]- India
2003
A. The more cracks, the smaller the corrosion battery is. Yours is definitely in that range. Increasing thickness of plate will help, but not as much as you want. In the thirties, chrome bumpers were more than .010" and formed long cracks that lead to peeling. Copper underplate cut the amount of chrome in half and adding two layers nickel cut it to tenths with longer life. If you are going to do quality work, it will require an underplate or cheating and waxing before CASS. But cheating poor product would put that company out of business in a few years.
James Watts- Navarre, Florida
2003
Q. With some trials I managed to get 1500 cracks / linear cm on some pieces. But there was no difference observed in the CASS tests as compared to the ones with 1000 cracks / linear cm. I am of the opinion that if too many cracks originate from the same point, it may lead to pore formation, resulting in a decrease of corrosion resistance. Am I right?
An undercoat of copper / nickel will definitely help, but will involve installation of new tanks. Can there be any improvement by some specialised grinding / polishing of the base metal?
Vijaykumar [returning]- India
2003
A. You fail to say wether your plating solution is the old type (a thousandth per hour @ 2 Amps per sq in ), or the more modern high speed hard chrome that runs hotter with higher current densities? I have hard chromed parts for hot rod and bike enthusiasts of decorative nature. Differential housings, tappet covers, fork leg tubes, nuts and bolts and even plain wheel rims. Firstly, the parts are polished as normal. Any stopping off is done using a combination of rubber or wooden plugs. Sometimes disc thieves, as on differential ends. Threads are taped up and secured with s/s wire. After masking and etching, current is slowly increased to three times calculated for ten minutes, then reduced to normal for 12 hours, overnight. Remove trees, and finish polish. Good forever! The cost is Astronomical! But they pay.
Mark Gunn- NSW, Australia
2003
Q. How to achieve maximum corrosion resistance in hard chrome plating? What are the influencing factors? We normally do CASS (cupric chloride acetic acid ⇦ on eBay or Amazon [affil links] spray test) for 96 hours. We are looking at no corrosion in 96 hours spray. We are using conventional chemistry and high speed chemistry. What are the precautions taken for hard chrome plating used in offshore applications?
Jayakrishnan.C- Bangalore, India
A. Dear Jayakrishnan:
Use an underplate of nickel of at least 25 microns before chrome. This is top class of plating and should have no problems passing your tests.
Bye,
Guillermo MarrufoMonterrey, NL, Mexico
Q. Dear All,
Could you tell me how to improve corrosion resistance of steel. Now I use hard chrome. I must obtain resistance of the order of 500 hour in salt spray chamber. Maybe duplex chrome, HVOF, etc.?
Please help me.
hobbyist - POLAND
2006
A. Marek, frankly I don't think hobbyists should ever attempt hard chrome plating because the plating solution and its mists are carcinogenic and highly toxic; but maybe there was a misunderstanding about the word "hobbyist" and you are an industrialist "tinkering" with possible solutions to your situation?
While chrome plating offers a little bit of corrosion resistance, it is not anodic to steel so it doesn't offer sacrificial protection, and it is always cracked or porous, so it doesn't offer barrier layer protection either. So it is not a practical coating for an application that requires significant corrosion resistance.
With an under layer of electrolytic or electroless nickel, thick enough to be pinhole-free and non porous, you can obtain very good corrosion resistance. If you search the site for "electroless nickel hard chrome" you will find several threads where this combination coating is discussed. Letter 1686 is probably the best introduction to HVOF as an alternative to hard chrome plating. Good luck.
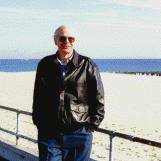
Ted Mooney, P.E.
Striving to live Aloha
finishing.com - Pine Beach, New Jersey
2006
Q. Dear Sir/Madam,
We have a technical difficulty in one of our research projects and hope to get some help from you.
In one of our corrosion tests, we used a carbon steel specimen partially plated with hard chrome. The reason we did that was to protect the unwanted surface from being corroded. Hard chrome was found to not corrode at all during the test. After the test, however, we need to clean/descale the specimen (remove the oxides on the carbon steel surface that was not covered by the hard chrome) so that we could know how much the weight loss is. Unfortunately, during this cleaning process, we found we had lost more hard chrome than carbon steel oxide. In other words, although hard chrome did not corrode during the test, it was corroded during the post-test cleaning procedure.
We have checked with ASM Metals Handbook and found it is said the corrosion rates for hard chrome in 10% and 20% NaOH should be nil at room temperature. In our cleaning, however, we found unbearable weight loss on the hard chrome (e.g. 200 MPY to 1,200 MPY, mils per year). We feel we have hit a ghost here. We had the hard chrome plated at a local company in sulfuric bath. Is this because they didn't do a good job ? Or is the hard chrome is supposed to behave like that ?
We appreciate your expert help on hard chrome plating.
Regards,
Fred Hua- Alliance, Ohio
A. Chrome is resistant to caustic soda ⇦liquid caustic soda in bulk on Amazon [affil link] solutions. BUT, add in a small voltage and chrome is stripped very efficiently and is one of the two most common ways for stripping chrome in the industry. Possibly, you had it in a metal bucket/can or you had a very moderately dissimilar other metal in the bucket or? In short, you somehow managed to have a battery.
James Watts- Navarre, Florida
A. Are you also using anodic DC current to clean the parts? If so you are stripping the chrome from the steel.
Todd Osmolski- Charlotte, North Carolina, USA
October 7, 2012
Hi Fred. One final comment on the test that you described: You said that the hard chrome did not corrode during your test, but please remember that the uncoated steel area was anodic to the chrome plating and offered cathodic protection, not unlike the way a zinc anode protects a ship's steel hull. The results might have been different if you had masked the exposed steel.
Regards,
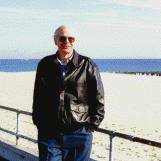
Ted Mooney, P.E.
Striving to live Aloha
finishing.com - Pine Beach, New Jersey
Q. I am looking for corrosion resistance in the presence of HBr, Cl, and Fl chemicals. Application is linear motion components in semicon process (etch). My plating options are Hard Chrome, Black Chrome, and Black Chrome with Fluorine Resin. The component material is high carbon steel and martensitic Stainless -- case hardened in both cases.
Steven BurleySilho Engineering - San Ramon, California
May 22, 2018

Q, A, or Comment on THIS thread -or- Start a NEW Thread