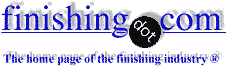
-----
Gold Alodine Color Variation
2003
I have been using a local company to do a gold Alodine finish on 6061 aluminum. My parts have an end use in an electronics application.
My dilemma has been a fair amount of color variation and striking. The color variation is in the form of a pink haze especially noticeable around holes and close to the edge of the part or panel. My supplier is telling me that this is normal and expectable iridescence and there is nothing that they can do, but I am not convinced hence this inquiry. As for the striking it is my belief that this could be solved by rinsing and drying the parts more thoroughly. Do you have any insight that you can provide?
Thanks,
William Cope- Powell, Ohio, USA
Your supplier is more than likely 100% correct. The "discoloration" that is occurring around your holes is common. The reason I most associate with it is that the stresses that are associated with those cutouts take the chromate conversion coating in a different fashion. Whether those holes are punched, laser cut, waterjet or what have you from the part is a non-issue. There is always going to be an associated stress in those areas that the rest of the part does not have to endure. Thereby the chromate reacts differently in those locations.
Now, if the areas in question are giving you issues, the only suggestion I would have for your finisher would possibly be to etch the parts more thoroughly to possibly minimize the effect this is having on the coloration of the part. But other than the coloration difference, it should have no direct bearing on the performance of the part or the finish.
I am unsure as to what exactly you mean by "striking". Is the part conducting a spark in these associated area's more so than in others? Do you mean "streaking" as in the part has a noticeable pattern of discoloration in a certain direction? If so then you are probably right there, to some extent. Study the parts in question, if the streaks that I assume is what you mean mind you. If they are universally directional, then yes, they are probably not being dried fast enough, and water is discoloring the surface. If your product has a cosmetic use than I can see your discouragement with such a thing. I dry my chromate parts in a fully enclosed box heater setup I made. Basically 2-3 6000 W heaters using fan forced air are mounted to this box, and they circulate air around 100 F around the inside of the box. Its efficient, and cost effective, and the drying temperatures are nothing that will inhibit the chromate coatings (drying at temps higher than I believe I've read 140 F can sometimes lead to premature cracking of the surfaces). I very rarely have issues with streaks, but some parts do tend to lend themselves to trapping of water more so than others. Study how the part is racked first, see if there is excess water being trapped in the part after its rinsed, see if that water can be either physically shaken from the parts prior to finalizing the drying, or see if racking the parts in another configuration could allow for more suitable drainage of the parts to possibly fix this problem.
Good Luck to you William.
Matthew Stiltnerplating company - Toledo, Ohio
2003
Color variation and iridescence IS normal on chromate conversion coatings (hence the brand name Iridite from one manufacturer). You can get color variation from an even gold color to green and/or pink iridescence within an hour during production. It's the nature of the animal. As far as "striking" is concerned, I don't know what you mean by that.
Guy Lester- Apple Valley, California, USA
2003
Q, A, or Comment on THIS thread -or- Start a NEW Thread