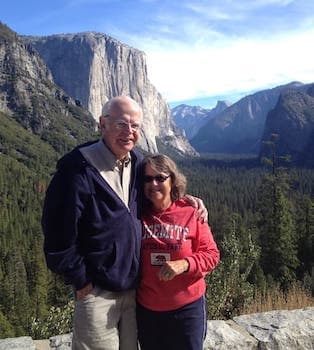
Curated with aloha by
Ted Mooney, P.E. RET
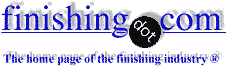
The authoritative public forum
for Metal Finishing 1989-2025
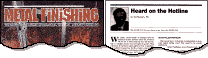
-----
Electroless Nickel Plating from low cost country peels and blisters
Q. We recently received some poorly plated parts from a Low Cost Country supplier. I used a dull stainless steel tool to "burnish" the part and the Electroless Nickel plating began to peel up or blister. This obviously shows poor plating, and the last I had to deal with this I was working with a company in the USA. Their problem was that the cleaning process in the HCl tank was contaminated and left residual acid on the surface of the part before the plating process. This led to poor adhesion. My questions are:
1. Is there a burnish tool specification so the Low Cost Country can test to see if they have proper adhesion?
2. If they continue to have problems in plating, is it even worth trying to work with the Low Cost Country with such a difficult process as EN plating? I just want to know if it is a common problem that is difficult to resolve.
Thanks,
Jason Ertel- Waukesha, Wisconsin
2003
A. I think this is a question best answered by a high quality shop in that low-cost country :-)
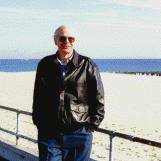
Ted Mooney, P.E.
Striving to live Aloha
finishing.com - Pine Beach, New Jersey
2003
A. Hi Jason,
My first impulse was that you get what you pay for, but as a Wisconsin native, I'll try to help. First, "residual acid on the surface" isn't a likely cause. HCl is easily rinsed and is an ingredient in the subsequent Wood's nickel strike. Possibly, an organic contaminant was involved, the surface became passive, or the Wood's nickel strike plating was done improperly or even omitted. The procedures from the EN supplier should be followed. Parts should not be allowed to dry after the HCl cleaning and anodic cleaning (if used) since the surface will passivate. This passivation can be overcome in the Wood's nickel solution by a little reverse current before plating. Further, the Wood's nickel should not be allowed to dry before EN plating.
As for testing, require the adhesion test on a part or a sample coupon per MIL-C-26074 [⇦ this spec on DLA]E (&ASTM B571). As this spec. is no longer freely available, here are the relative sections:
"3.3.3 Adhesion on metals. The coating adhesion after completion of all processing and thermal treatments shall be such that when examined at a magnification of 4X, the coating shall not show separation from the basis metal when tested in accordance with ASTM B571 as specified in 4.5.2. It also shall be impossible to detach any area of the coating with a sharp instrument on the outside radius of the bent-test specimen. Formation of cracks that do not result in loss of plating adhesion is acceptable."
"4.5.2 Adhesion test. The test specimen shall be bent 180 deg over a mandrel [of] diameter 4 times the thickness (0.4 inch minimum) of the specimen."
It is up to you whether to continue using a supplier who ships product without rudimentary QC testing. EN coatings lacking adhesion will also fail salt spray testing, etc.
Ken Vlach [deceased]- Goleta, California

Rest in peace, Ken. Thank you for your hard work which the finishing world, and we at finishing.com, continue to benefit from.
2003
A. Once again, the matter of outsourcing. To contract a service (specially abroad) is by no means the same as to go out for shopping. You want a commodity part of such brand and No., buy it wherever it's cheaper. There's almost nothing the vendor can do to reduce it's quality. You want to hire a service performed ahead of time, you better get a qualified source. We have a saying in Mexico which translates more or less "Cheap at the end is expensive".
Guillermo MarrufoMonterrey, NL, Mexico
2003
Q, A, or Comment on THIS thread -or- Start a NEW Thread