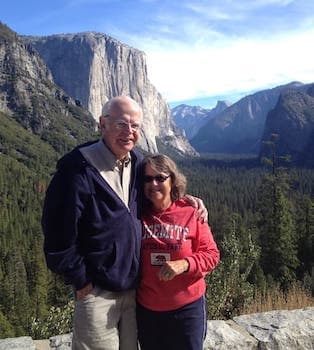
Curated with aloha by
Ted Mooney, P.E. RET
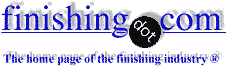
The authoritative public forum
for Metal Finishing 1989-2025
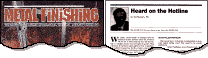
-----
7 tank hot phosphating process
Q. We use lot of sheet metal components in an industrial product with a powder coated finish. The basic pretreatment used before powder coating is 7 / 8 tank Hot process for cleaning & applying a thin phosphate coat. In this regard we will like to know if you have done any standardization of chemical Processes ? If yes , can you throw some light on following
1) Details of 7 / 8 Tank hot process
2) The chemical composition & temperature of each liquid in all tanks.
3) The Approximate time interval for sheet-metal to be kept in each tank for cleaning / coating etc.
4) If you have made any industrial standards as ref. document?
5) If you suggest any book which covers these topics , it will be extremely good.
Please Revert Back with reply.
Best Regards,
DILIP P. MANOHAR- MUMBAI, India
2003
A. Hi Dilip. It's out of print and hard to find but Samuel Spring's Preparation of Metal for Painting ⇦[this on Amazon affil links] is a book that I can recommend as what you're looking for.
Another book with a good reputation that sounds right, but which I personally haven't reviewed is "Phosphating of Metals" ⇦[this on Amazon or AbeBooks affil links] by Rausch. Best of luck.
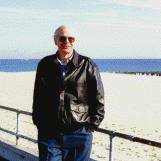
Ted Mooney, P.E.
Striving to live Aloha
finishing.com - Pine Beach, New Jersey
Q. I am a metallurgical engineering graduate 1990 batch, with MBA. I have installed a new small scale unit basically for powder coating, products like wrought iron articles/furniture, lamps and lamp shades, pedestal fans and many other items that can be coated. I have not yet started commercial production which shall begin in a couple of days; right know I am working on samples to be displayed in the target market. I would like to know if the three-in-one phosphating chemical is equivalent to 7 tank process, if yes what should be the concentration of phosphating chemical in water (if it is to be diluted), temperature and time for removing rust from steel and cast iron. Further before phosphating I am using HCl Acid for degreasing scale removal; I have heard that some people use sulfuric acid, which is better if final product is to electrostatically powder coated.
RAHUL SHUKLAMETAL CRAFTS - Batala, Punjab, India
2004
A. Hi Rahul. The 3-step phosphatizing (clean/phosphatize, rinse, rinse) is almost always iron phosphating and is restricted to steel parts whereas the 7-step process is usually zinc phosphating and can be used on aluminum as well. A typical sequence is clean, rinse, rinse, zinc phosphate, rinse, rinse, passivating rinse is one sequence.
I don't think anyone anywhere would claim that the 3-step process is as good as the 7-step process; nor that putting the ice cream in the soup, and the salad into the coffee, to get to 3 plates is as good as a 7-course dinner. But, if the painting system is good, a good 3-step process may be fine, and certainly for interior work.
The principal reason most people use hydrochloric acid is that it will work at room temperature whereas sulfuric acid tanks need to be almost 100 °C to function well for scale removal.
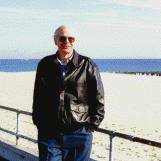
Ted Mooney, P.E.
Striving to live Aloha
finishing.com - Pine Beach, New Jersey
2004
Q. Dear Sir,
I would like to inform you that I have applied for the post of AME(C&W) under Eastern Railway. I am continuously trying to get the process of Hot phosphating which is urgently required for examination. Please send at the earliest to my email address so that I can prepare the same.
Thanking you,
Yours faithfully
PERSONNEL - ASANSOL,WEST BENGAL, INDIA
2006
A. Hello Pranab. Best of luck with the examination, but realistically no one is going to write a book about phosphatizing for you and e-mail it to you personally, and all at no cost :-)
We've answered some specific questions, and are willing to try to answer others, and have recommended two books about phosphating. If neither of those books is available in a local library, then please start with the Metal Finishing Guidebook. There should be copies in your local area; and if not, used copies can be obtained for about $10. Success on the exam!
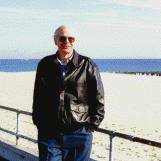
Ted Mooney, P.E.
Striving to live Aloha
finishing.com - Pine Beach, New Jersey
2006
Q. I am having a bus body painting, I want to know the process of hot phosphating and also the in-process quality parameters to be checked which are affecting the coating.
Anil Balurkarpainting shop employee - Zaheerabad, A.P., India
March 7, 2008
Q. Dear sir,
This is rajeshkumar; currently I am working in a radiator manufacturing industry as a Quality Engineer; in my concern 7 tank hot phosphating process exists, we have the procedure to prepare the bath solutions but we don't have any in-process checking parameters and how check the supplied solutions; whether in correct concentration or not, I want the clear procedure about the process, in-process checking parameter, procedure to check the chemicals before mixing & bath maintenance.
employer - coimbatore,Tamil Nadu, India
August 5, 2008
A. Dear Rajesh Kumar,
I do not know why you facing problem to check strength of supplied chemical or your bath strength. The simple process is titration.
- New Delhi, India
October 21, 2008
by Samuel Spring
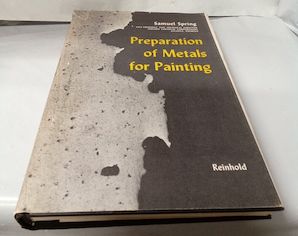
on eBay
(currently)
or AbeBooks
(rarely)
or Amazon
(rarely)
(affil links)
Q. Dear sir,
My plant has 7-step hot zinc based Phosphating Process basically done for precoating for metal parts for rubber bonding purpose. We don't have any standard for thickness of phosphate coat required for metal to rubber bonding -- can you guide me?
Recently we eliminated derusting by HCl , we do derusting by phosphoric acid but more time is required for this process -- you have any solution? We given compressed air line in all tank for better agitation, is this the right method?
QA Incharge - Nashik, Maharstra, India
April 21, 2009
Q. We are painting 1 mm sheet thickness components hence we would like know the correct procedure for 7 tank pre treatment process before spray painting. I also wish to have the details of each tank content, chemical specifications, timings, proportion of mixing, titration procedure and their chemicals, identification of metal finish after every tank for correct work done and life of chemical mixture etc.
Regards
production manager - Dharwad, Karnatak, India.
March 30, 2010
A. Hi, Muralidhar. We have recommended two good books on phosphating that were written to address exactly those issues, and we've suggested the general purpose Metal Finishing Guidebook as a starting point if you have trouble locating those.
Alternately you can contact a metal finishing supplier who will recommend their proprietary chemistry for the seven steps and give you technical data sheets for each step. Good luck!
Our readers can often answer simple straightforward questions, but what you are asking for cannot be delivered short of book length, so the only options are to get one or for a supplier to sell you the chemicals and include suggested operating parameters for their particular solution to your problem. Good luck.
Regards,
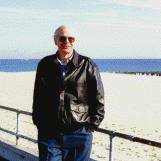
Ted Mooney, P.E.
Striving to live Aloha
finishing.com - Pine Beach, New Jersey
March , 2010
Q. Dear sir,
Please give me information about seven tank process for powder coating for m.s.parts and aluminium parts
plant owner - Pune, Maharastra, India
April 4, 2010
A. STANDARD 7-TANK PROCESS
A standard 7 tank DIP ZINC PHOSPHATING process is used, where good paint adhesion and corrosion resistance are required before painting. However, where hot rolled sheet metal or heavily rusty surfaces are to be dealt with, the use of mineral acids like hydrochloric acid or sulfuric acid will have to be used. An additional tank for cold water rinsing after derusting will be necessary to ensure that carryover of mineral acid into the zinc phosphating bath is avoided as it is detrimental to its functioning.
PROCESS
TANK # FUNCTION CHEMICAL STRENGTH TEMP °C DIP TIME (MINUTES) 1. Degrease Chemlene 1D 3-5% 85-95 5-15 2. Cold water Rinse - - - 1 3. Derust Chemdine250 25-30% RT 5-10 (Cold) Chemdine170 20-25% 60-70 5-10 (Hot) 4. Cold water rinse - - - 1 5. Zinc Phosphate Chemphos 20 3% Chemtoner 0.025% 70-80 3-5 6. Cold Water Rinse - - - 1 7. Passivation Chemlyte 10 0.025% RT-70 1
CHEMDINE 250 (cold) or CHEMDINE 170 (Hot) is generally used, for derusting of cold rolled metal. Where the use of mineral acid such as hydrochloric acid or sulfuric acid is used to remove scale, an additional Cold water rinse , after pickling (Tank # 3) will be necessary. This will make it a 8 Tank Process.
CHEMPHOS 20/CHEMTONER forms a micro-crystalline uniform tightly adherent zinc phosphate coating which has excellent paint adhesion and corrosion resistance.
ZINC PHOSPHATING PROCESS USING PRECONDITIONER CHEMFIX 50
Often, the use of a PRECONDITIONER before zinc phosphating is preferred to condition & prepare the surface to receive an extremely fine textured coating. This becomes particularly important in certain steels and steels which show some resistance to coating formation.
- Pune, India
----
Ed. note: We thank Ganesh for providing this detail and an example of one particular proprietary brand name for the various steps. But readers should be aware that there are many suppliers of proprietary process chemistry for phosphatizing, and that we are trying to avoid a race to the bottom with any claims that any particular brand is better than another.
Q. Please suggest suitable Alkaline based chemical for passivation after Phosphating.
Anand Kaundanya- Mumbai, India
March 1, 2013
A. Hi Anand. Are you a supplier of phosphatization chemistry to job shops, or are you a user? If you are a user, it is best to go with the same supplier for the 'passivation' as for the phosphatization, as the "system" is what they will be experienced with and will have case studies and test results for.
Why "Alkaline"? Do you intend to paint the parts? If so, what kind of paint or powder will you be using? Thanks.
There are no prizes for brevity in posting. Please introduce yourself and your situation so that we have a better chance of not wasting your time.
Regards,
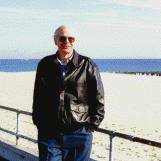
Ted Mooney, P.E.
Striving to live Aloha
finishing.com - Pine Beach, New Jersey
March 1, 2013
Q. 7 tank process. We have a lot of customers to provide us the powder coating jobs. Hence, we need to start this business within 2-3 months. We request you to provide details for this business.
dilip narkhede- Pune, India
April 12, 2013
A. Hi Dilip. Although Ganesh has described the 7-tank process for you, if you need to start up in 2 or 3 months you don't have time to learn what you need to know, no matter how hard you study :-(
I think you need to immediately find a trusted powder coating consultant who can review you proposed work load with you and plan out the pretreatment line and the powder coating line. Do you have strong reason to believe that the 7-tank process is the best pretreatment plan? Do you foresee dipping the work or spraying it? Will you be doing steel work only? Will all of the work be for outdoor exposure or all for interior use, or a mix? Are you sure you don't also need an electrocoating line for priming the work? Please don't wait too long and paint your consultant into a corner before you even retain him -- the earliest decisions are the most crucial ones. Good luck!
Regards,
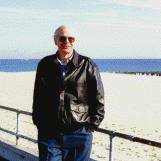
Ted Mooney, P.E.
Striving to live Aloha
finishing.com - Pine Beach, New Jersey
April 13, 2013
7 tank process at room temperature
Q. Dear Mooney,
I am in automotive sector and use surface treatment process for rubber bonding with metal application. So I have to know which type process & chemical would be adopted and used to achieve this. This is my value engineering because: save energy save earth so naturally save people.
Value Engineering - Rampur , UP, India
June 15, 2013
A. Hello Fareed. Sorry, I don't know the best preparatory steps for rubber bonding.
opinion! But since you posted this under "hot vs. room temperature phosphating" ...
I completely disagree with the premise that saving energy in phosphating saves the earth! We live in a world of limited resources that we should be working to sustain, but what I see around me every day instead is low quality pretreatment which condemns the metal things we manufacture to a very short life.
Patio furniture, as one quick example, can easily last two decades in the worst environmental conditions if it is properly phosphated and properly painted. Instead, most such items that we buy today last but 3 years and often less. By shortcutting the phosphatizing, we must re-mine ore and re-ship it, re-smelt the steel and re-ship it, re-fabricate the item, re-phosphate & re-paint & re-package the item and reship it; re-stock & re-sell and re-ship the item to the consumer, and finally build huge lanfills and send garbage trucks out to collect this junk and dispose of the item at least 5 times as often as necessary. Corner-cutting on phosphatizing is an environmental disgrace!
Everyone should phosphate their items the very very best way they know how, ignoring energy requirements, ignoring cost, and ignoring how much chemical they need to use for proper pretreatment. The earth will thank us :-)
If you must do cost reductions due to management pressure, well, you must. But please never kid yourself that you are doing it for environmental reasons -- skimping on phosphatizing is a sustainability travesty.
Regards,
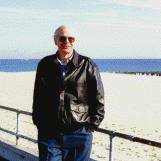
Ted Mooney, P.E.
Striving to live Aloha
finishing.com - Pine Beach, New Jersey
June 21, 2013
Air bubbles prevent proper pretreatment of storage water heater tanks
Q. Dear Sir,
I manufacture storage water heater tanks. they need to be passed through 7 tank pre-treatment process. We are experiencing formation of air bubbles inside the tank which leads to formation of rust in that specific portion of tank.
Please suggest something in order to overcome this air bubble problem.
Awaiting your quick response.
Thanks!
- noida, uttar pradesh, India
July 12, 2013
Q. I need to know the life of Phosphatized surface treatment done on Investment casting parts. Is it true that such treated casting lasts for corrosion protection for several years? Please guide.
Jainik Shah- Bhavnagar, India
April 3, 2018
A. Hi Janik. There are several types of phosphatizing, ranging from the simplest (iron phosphate) through zinc phosphate, and on to manganese phosphatizing (which is thickest and best at retaining rust-preventative oil).
Even the best, with a good coating of oil, have limited corrosion resistance -- it's not considered a final finish except for parts which will operate bathed in oil like engine parts. A heavy phosphate dipped in rust preventative oil might last a couple of years in indoor storage under good conditions but you would have to lucky. Phosphate without oil or wax sometimes doesn't resist rust for a day. Good luck.
Regards,
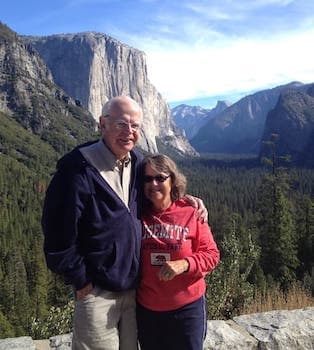
Ted Mooney, P.E. RET
Striving to live Aloha
finishing.com - Pine Beach, New Jersey
April 2018
Q, A, or Comment on THIS thread -or- Start a NEW Thread