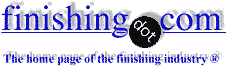
-----
Anodize as dielectric?
2003
Hi,
I'm trying to get an aluminum tube to be electrically isolated from 350 V. The electrical source will also be an indirect heat source (there will be arcing nearby), though the temperature the anodize would see is difficult to characterize. The tube OD with anodizing needs to be less than 0.030 in. Thus, the anodize thickness should be around .002-.004. Would anodizing do the trick here? What else can be done?
Thanks,
Harry Kwana medical specialties company - Hayward, California, USA
The main problem is that the extremely small diameter will cause a highly cracked anodic coating. A minimum diameter of 0.064 inch is recommended for a hard anodize thickness of 0.001 inch, and due to the anodic growth mechanism, the coating will have more cracks than a flat surface. The Surface Treatment and Finishing of Aluminum and Its Alloys by S. Wernick, R. Pinner, P.G. Sheasby 6th Edn., p.786. Another potential problem is temperature fluctuation, as aluminum has a much higher coefficient of thermal expansion than the anodic oxide. High temperatures could open cracks and melt any supplemental sealant, such as paraffin, ibid., p. 804, thereby compromising the dielectric strength [550 V for 0.001‡ hard anodize, sealed in boiling water and impregnated with paraffin wax].
Ken Vlach [deceased]- Goleta, California

Rest in peace, Ken. Thank you for your hard work which the finishing world, and we at finishing.com, continue to benefit from.
2003
This is an interesting question. I too have been looking at using anodic coatings as a dielectric to withstand 300 V. I have checked around in industry but can find no people using it as a dielectric. Many heat sinks are made using an anodic coating but it seems that other precautions are taken to ensure the electric isolation, presumably meaning that the coating is not trusted enough. Any information submitted to this thread would be much appreciated.
James CotsellCentre for Sustainable Energy Systems - Canberra, ACT, Australia
2003
Q, A, or Comment on THIS thread -or- Start a NEW Thread