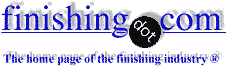
-----
Bright Dip Chemicals Attacking Tank?
1998
We do aluminum anodizing (all types) as well as bright dipping here. My question:
There are 2 main bright dip solutions in use today,
1- The traditional Phosphoric/Nitric solution.
2- The Phosphoric/Nitric/Sulfuric solution.
We use the #2 Solution because as a job shop we find it much more stable & consistent because we are running different alloys thru the tank.
Is the #2 solution more detrimental to the life of our 316L SS Tank life? Does the #1 solution not attack the tank as bad?
Any opinions would be greatly appreciated.
Thanks
- Long Island City, New York
1998
David,
If you want to know the corrosion rates of your tank material in these two solutions, you can do a simple experiment: put a sheet of stainless steel identical to the tank material with known weight and surafce area into each solution in beakers [beakers on
eBay
or
Amazon [affil links] with a certain volume (in general, surface area to solution volume requires at least 1 sq. cm to 50 cu. cm) at operational conditions (temperature and agitation) for a few hours. Then take out samples, wash, dry, weigh them again, and calculate the corrosion rates. Of course, the samples have to be cleaned and dried before immersion tests.
Ling
- Grand Rapids, Michigan
1998
Hi,
Why use ss ... why NOT use stainless! Stainless is very good when nitric (by itself) is used and maybe, I don't know, OK for solution # l. However, # 2 solution contains sulfuric and mixtures of acids may have some bad effects such as nitric + Hf = bad news to any metal, ANY, including titanium.
sulfuric is OK at very low or very high concentrations but otherwise is bad news, particularly in ducting venting low concentrations ... but then fibreglass will also eventually fail, too. PVC doesn't. Stainless will.
If you have a problem, consider a suitable thermoplastic duly FRP reinforced, eg. PVC but never PP or Pe due to their stress cracking potential in oxidizing environments particularly where any welding is done,
There are even better thermoplastics such as the weldable fluorocarbons but that is an expen$ive option! Any competent dual laminate fabricator should be able to help you.
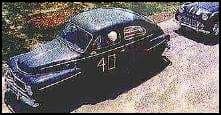
Freeman Newton [deceased]
(It is our sad duty to advise that Freeman passed away
April 21, 2012. R.I.P. old friend).
Freeman,
The problem is that these brite dips are about 210 °F., so PVC and the like aren't going to work.
David,
Solution #1 is also horribly corrosive, and 316L tanks have a limited life with it as well. Often, these tanks are built of double wall construction so that if the inside tank begins to leak at the seams, you won't have a catastrophic failure. I would guess that Freeman is right that fluorocarbons will probably work, but are horribly expensive. I don't know quite what size your tank is, but I wouldn't be at all surprised if you got quotes in the $30,000 and up range for fluoropolymer dual-laminate tanks. Have you considered a drop-in liner?
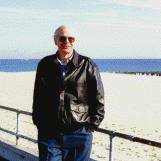
Ted Mooney, P.E.
Striving to live Aloha
finishing.com - Pine Beach, New Jersey
--
Ted,
Wow! I didn't know that the temperatures were that high! You are right, PVC is nbg. HOWEVER, there's the big brother of PVC, CPVC. When this has fibreglass bonded to it, if I recall correctly, the operating temperature can be 2l2 °F... and that under some pressure conditions, too.
However, if there's nitric AND hot temperatures, I am not in love with a flexible (I assume you meant!) PVC Liner. Why? Because the plasticizers can get leached out. (Ask Tibor Nemeth in Ca for his opinion)
Maybe PVDF (duly armoured with fibreglass by a specialist Company) is the answer. But like you I'd also consider, say, HALAR ectfe fluorocarbon which could be about the same price.
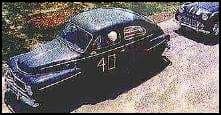
Freeman Newton [deceased]
(It is our sad duty to advise that Freeman passed away
April 21, 2012. R.I.P. old friend).
1998
Ted.
I didn't quite catch on in the beginning. You mentioned DOUBLE WALL tanks. Heck, I've never EVER SEEN a double walled plating tank. What in the H--- for! What a waste of $. But then I guess people feel that 'stainless' is a good material and they must use it, What about the super alloys? The Carpenter 20's & the Hastelloy, Super high nickel - chrome + moly or whatever to give very superior corrosion resistance,. However, you really cannot beat a high class thermoplastic duly armored with fibreglass where acids and stress and reasonable temperatures dominate.
Therefore I'd guess that a CPVC:FRP tank would cost less than a dual containment ss 3l6 L tank & THEN maybe a HALAR:FRP tank might be the same as the ss tank. And the big crunch against ss tanks would the welding, carbide precipitation et al. We spark test our thermoplastic welds and then, after bonding on (bonding is a KEY word) the fibreglass structural side, we re-spark test for total weld integrity.... and no carbide precipitation ... no zemetit & perlite zone problems! Lucky us! Then we re-spark test after completing the FRP structural.
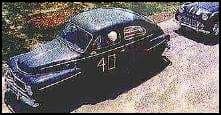
Freeman Newton [deceased]
(It is our sad duty to advise that Freeman passed away
April 21, 2012. R.I.P. old friend).
1998
I believe completely in the use of plastic rather than metal in a plating shop, Freeman. But before somebody invests $10-$50K in a single tank, they are going to want to know that the material of construction is satisfactory.
Your guess is that CPVC is okay, my guess is that it is not. Now, if we had a welded coupon of CPVC, and let it sit in the heated solution for a few weeks, we would be closer to knowing. We still wouldn't know for sure, because oxidizing acids have a way of attacking vinyls at the air-liquid interface (thus the double layer of lining material used there in typical chrome plating tanks). Chrome also always manages to weep through PVC welds (which is why the welded joints in hoods and ducts have to be at the top rather than the bottom), and I don't know whether CPVC tanks holding brite dip solutions would suffer the same problem.
I believe that fluoropolymer linings (that's what I was referring to, not PVC drop-in linings) would hold up fine, but I'm sure that Mr. Kraft would like to see one that has been in use for some years before making such an investment.
The reason that double-walled stainless has been used is simply that it works, while affording a safety net against this nasty solution. If we can be assured that fluoropolymer linings work, that would be the ideal solution. If someone has one, or if some vendor has experience in this, please pipe in.
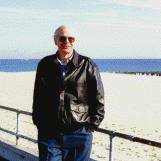
Ted Mooney, P.E.
Striving to live Aloha
finishing.com - Pine Beach, New Jersey
--
1998
Hi Ted !
Re CPVC & 'my guess; ... no guess, Ted, but a reasonable assumption. Not an affirmation but not a wild guess.
Re surface interface attack, for flexible PVCs you HAVE to use a double layer. Flex PVCs suffer from one main thing, they get BRITTLE as the plasticizer gets leached out. Hence, it's a must for chrome tanks.
Re fluorocarbons. Ah. They would work A.0K. But would I recommend them for a plating tank? Not if they were just liners! Why? Because they are, for us as a main fabricator, only available at 0.060" and
0.090" thick. By that I mean these are the max. thicknesses that are available for welding them.. and they sure ain't too flexible. Further, with a thin liner, would you really feel that the plater would get a good life from it? ... just one big scrape ( Aw heck, the Mack Truck cylinder head has gone an' fallen off the hoist an' dropped onto the tank.... OW !)
Another question... & pardon my ignorance ... but I just did not know that these bright dip solutions run at 2l0 degrees.
Not being in the office, I don't have that tome of Knowledge, the ventilation manual, to tell me what, perhaps, the solution temperatures go to. For Bright Dips in the past (in Ontario where all the action is) all hoods & ducting were straight PVC which, had there been high temperatures, would have caused hood distortion. I am working just now on a mini set-up ... nitric at full strength (so I was told to my disbelief) and sulfuric and plus, ah, some nice Hydrofluoric). But all at room temperature. The mini tanks are Polyethylene but with a heavy wall. Many, many years ago I.C,I.(U.K.) made a rather interesting statement. Whereas Polyethylene is most definitely & quickly attacked by chlorine, it is RESISTANT if it has a heavy wall. One deduces that the chemical attack peters out ... and leaves a passive barrier. Which is maybe why a PVC liner of, say, l/l6" thickness will only last 4 times or so LESS than one at 1/8" thick. Food for thought, eh?
Lastly. A coupon, testing thereof! Ah. Whereas you can do this with equanimity for metals, you do NOT get the feedback using plastics. I'm damned sure that if you got a PVC coupon and kept it in a vicious bright dip solution at 210, upon removal it wouldn't tell you a thing ... and would weigh the same (maybe a v.v. slight increase in weight as it's permeability is very low) & you can't etch it like a metal sample, to determine grain boundaries, etc.
From a design viewpoint you look at extrapolated curves of the modulus and tensile strength ... and the strengths drop rapidly for one year and then slow right down to nearly parity at 3 years. These then are the figures one must be guided by when designing, especially for HEAT, any stressed structure. Thermoplastics being very heat sensitive unlike fibreglass.
I like your comment about duct welds should be 'at the top'. I also agree that, for some unknown reason, PVC welds at chrome hoods sometimes fail. However, I've always been a proponent of using the most suitable approach and using (for chrome) l2 ga or l0 ga mild steel for the hoods. Why? Only because the impact strength is so much better and one must consider, at I know you will, the long term cost effectiveness to the plater..
Apropos of weld failure ... I know of totally NONE over 20 years on (my) Assay-Perchloric hoods handling mixed and far worse acids ... strong nitrics, Perchlorics ( which is a helluva wicked oxidizer), HCL, 93% sulfurics (which are boiled away at 320 degrees C !) Plus some HF & aqua regia. NO CORROSION, NONE, nil. zero. There was a case of heat distortion due to badly designed 4-1/2 kW hotplates, which even damaged the hotplate cables ... and one other where a gallon of Pyridene was spilt which caught fire & damaged 2 hotplates but not the hood (the fan impeller was damaged, however)
I'll check further re CPVC 's integrity with B.F. Goodrich & let you know what they say. OK?
Regards, Freeman
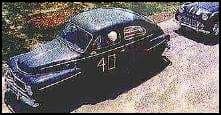
Freeman Newton [deceased]
(It is our sad duty to advise that Freeman passed away
April 21, 2012. R.I.P. old friend).
1998
Folks,
In fact, stainless steels (for example, 316L) are generally used to build Al bright-dip tanks in finishing shops. Because of the oxidation of nitric acid in bright-dip solutions, SS can maintain its passivity very well. Even at 210 °F, the general corrosion of SS in brit-dip solutions is trivial. However, it is very important to control the concentrations of components. It is extremely dangerous if the brite-dip solutions are contaminated with chlorides or fluorides. It is tough for PVC to resist high temperature. PTFE is too expensive and inconvenient to build tanks relative to SS. I believe SS coated with PTFE is the best tank material for the Al brite-dip solutions consisting of sulfuric/nitric/phosphoric acid mixture.
Ling
1998
Ling,
Thanks for your comments on bright dips using stainless. As I said earlier on, why not ... unless there are 'other' acids to make it a virulent brew. And you correctly pointed out chloride contamination.
Is the main problem at the welds? And if so, can one, does one use a low carbon special rod or can, perhaps, pure nickel be used? Am curious.
You are right about PVC. It doesn't like highish temperatures, nor polar/aromatic solvents, nor low temperature impact .... but oh, does it ever excel in acids and alkalies! And if reinforced with fibreglass, you achieve a true synergistic effect. The PVC protects the FRP against it's shortcomings of abrasion resistance and strong acids & alkalies. The FRP in turn , IF BONDED CORRECTLY to the thermoplastic, reduces its co-efficient of thermal expansion, increases its impact resistance and vastly increases its effective operating temperature.
The world's first successful dual laminates were tanks made in l96l for Robert Shaw Fulton's Toronto plating plant by Alcore Fabricating in Richmond Hill, Ontario. (They are still in business)
13-1/2 years later they closed that plant. I went down to see those tanks I had sold. . Ah. Just the identical sameness as they were AFTER a month's usage ... being tallish rectangular tanks, being (as we were then) clueless about stresses and FRP: thicknesses, not being told that the working temperature was min. l50 F, they bellied slightly at the top and remained, without failure, that way for 13-1/2 years.
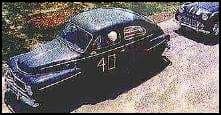
Freeman Newton [deceased]
(It is our sad duty to advise that Freeman passed away
April 21, 2012. R.I.P. old friend).
I believe the very best material for Bright Dip tank construction is Carpenter 20. It was designed just for exposure to Sulfuric acid conditions as well as maintaining the corrosion resistance for Nitric and sulfuric. It is an alloy consisting of 20% Chrome, 25% or more Nickel, 3-4% Moly, 2-4% copper with the balance iron. A so-called super stainless steel. I worked with a tank made of this material which lasted at least 10 years. 316 is the stuff everyone usually uses but in my experience only lasts about 5 years, much cheaper tho.
Ward Barcafer, CEFaerospace - Wichita, Kansas
1998
Use 316 L stainless steel and keep nitric level above 1.2 % to passivate the tank. If you are electropolishing do not use the tank as a cathode. Use a separate plate to carry the current load! Maintain temperature at about 210 °F. Your tank losses will be measured in mils/year.
Les Widmyer- Richmond, Virginia
2001
October 14, 2012
Get a titanium tank to keep from attacking it
Factors that cause tank to get attacked:
1. Heat
2. Mix of solutions
3. Time
4. How clean the tank is
5. Carry over from soap tanks
I can go on and on.
- Al
Q, A, or Comment on THIS thread -or- Start a NEW Thread