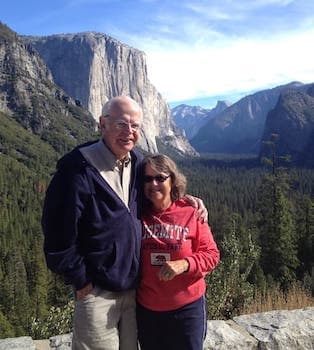
Curated with aloha by
Ted Mooney, P.E. RET
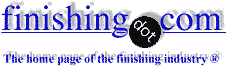
The authoritative public forum
for Metal Finishing 1989-2025
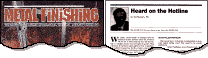
-----
Alternate cathode materials for anodizing tanks
[editor appended this entry to this thread which addresses it]
Q. Does anyone have experience with sulfuric acid anodizing cathodes other than aluminum or lead?
Luke Engineering & Mfg. Co. Inc.

Wadsworth, Ohio
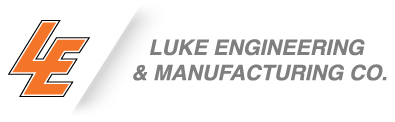
June 27, 2024
A. Hi Chris. We added your inquiry to this thread where Phil Johnson mentioned the alternative of stainless steel cathodes. I've personally never seen them used, and have seen nothing but lead or aluminum.
So far on this thread we've heard from 3 people who think stainless steel is not a good idea ... hopefully we'll hear from a user advocate so we can learn at least the hypothetical advantages of stainless steel :-)
Luck & Regards,
Ted Mooney, P.E. RET
Striving to live Aloha
finishing.com - Pine Beach, New Jersey
⇩ Related postings, oldest first ⇩
Q. Looking for peoples experience & opinions on which is better - using Aluminum or Stainless Steel cathodes in a anodizing tank.
David A. Kraft- Long Island City, New York
1998
A. David,
It depends on the anodizing processes you are using. For sulfuric acid anodizing, aluminum cathodes are better than SS cathodes from the point of economic view. For details, you may refer to some references:, The Surface Treatment and Finishing of Aluminum and Its Alloys by S. Wernick, R. Pinner, P.G. Sheasby p. 404; Plating and Surface Finishing, November
1981, p. 32-34; Metal Finishing Guide Book and Dictionary Issue 98, p. 474; and discussions in finishing.com 4th quarter 1997 or 1st quarter 1998 (Letters
524,
554,
1177).
Ling
- Grand Rapids, Michigan
A. Several years ago the job shop I worked in switched from lead to aluminum, following a paper on Al cathodes by Charlie Grubbs, then with Reynolds. Since we anodized most of our work by current density, rather than voltage, we quickly recognized that our loads were running about 1 to 1-1/2 volts lower than previously. This translates to close to at least a 10% power savings, and is probably even more, since there is less heat produced with consequent chiller power savings. Since then I've advocated Al cathodes. The difference between stainless and aluminum would probably not be as dramatic, but I still believe Al would save electricity, due to its higher conductivity.
If your loads are large enough, surface area-wise, that you need more cathode surface area than straight sheets can provide, Al is readily available in other shapes. The plant I worked in used 1-1/2" x
2" x 1" "U"" shaped extrusions. Drilling holes for connections is much easier in Al, as you probably know. We always used a conductive grease in joining Al cathodes or buss bars, to combat oxidation/corrosion.
Several of our large customers use stainless cathodes, but I am not that familiar with their long-term use. Maybe not everyone knows that weak sulfuric acid solutions will attack stainless steel, even 316, but not as much as Al, so stainless would probably last longer. It is not always practical, but for maximum cathode life it would be best to remove the cathodes from the anodize tank during prolonged down-times.
Phil Johnson
- Madison Heights, Michigan
A. The use of aluminum cathodes in preference to SS cathodes has stood the test of time. While Al has a conductivity of 55-60%, SS has about 7%. This translates into energy available for anodizing rather than producing heat.
Another factor to consider is the possible dissolution of Ni and Cr out of the SS cathodes.
Although sheet products are available that will work as cathodes, I have found that you have more flexibility with extrusions. These shapes will allow you to place the cathodes where they will do the most good.Many times a flat extrusion will suffice rather than trying to locate the more exotic shapes.
A 3:1 anode/cathode ratio has proven to be about the best in most general anodizing situations. I would STRONGLY suggest you use welded connections instead of bolts. Use alloy 5356 for welding and keep the welded joints out of the solution.
- Alpharetta, Georgia
Q, A, or Comment on THIS thread -or- Start a NEW Thread