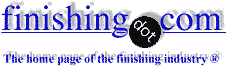
-----
White/light anodizing on aluminum casting
We are in the telecommunications industry. I am involved in the design of outdoor enclosures. We are currently working on an enclosure approx. 1.5 cubic ft.in size manufactured from cast aluminum. We have experimented with different types of coatings to help in the emissivity of the heat generated from the internal components as well as being thermally reflective. White powder coating has worked well but is somewhat expensive. Anodizing is more cost effective, but has proven to be less reflective due to the fact that it turns the aluminum a much darker color. Has any one heard of a white anodizing process or any similar process that might be of use in this situation? I'd appreciate any feedback.
Rick O [surname deleted for privacy by Editor]communications - Petaluma, California
1998
The gentleman who wrote Letter # 2053 has a problem similar to yours. Many people who design parts made from cast alloys are quite disappointed at the appearance after anodizing. Most common cast alloys are made with silicon as the major alloying element- often in the range of 4 to 23%. The more silicon the worse the situation- this element causes the anodic oxide to turn grey, and since hardly any cast part can solidify all at once in the mold, there is often a striation of the silicon and other alloying elements, causing the grey color to be variegated. This latter situation is especially true on any as-cast surface. Any time aesthetics of a part is important, these facts must be considered. There is no light colored anodize dye with anywhere near the hiding power to hide the mottled effect. Actually black dyes will hide the poor appearance best, unless your casting alloy is one that is highly porous and prone to bleedout. Consider also that a black coating has much higher emissivity than white. Is white necessary?
There is a series of cast alloys, the 500 series, I believe some call almag, with magnesium as the major alloying element instead of silicon. I have seen boat hardware made from one (512?) that retain their silvery aluminum appearance, but I don't know enough about their metallurgy to know why these alloys are not used more- perhaps it's a cost issue.
I still believe that for maximum outdoor corrosion resistance and best appearance that a formed wrought alloy would be best in the long run.
Phil Johnson
- Madison Heights, Michigan
1998
Q, A, or Comment on THIS thread -or- Start a NEW Thread