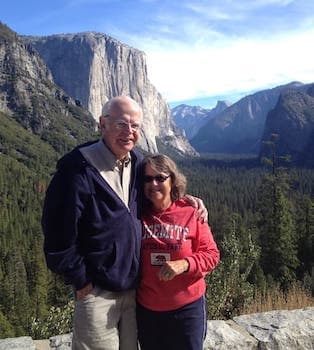
Curated with aloha by
Ted Mooney, P.E. RET
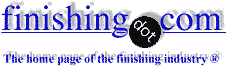
The authoritative public forum
for Metal Finishing 1989-2025
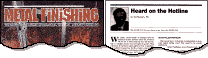
-----
Alternatives to Ivadizing
We currently make motors that operate in a salt water environment, underwater. We Ivadize and then paint them. Is this overkill for corrosion resistance, galvanic issues, etc. or is there a cheaper and more available way to have equal protection.
Sid Tryzbiak- Tulsa, Oklahoma
2003
First of two simultaneous responses
With the information given, no one can answer it. A guess is that 0.001" of high phos EN might work. Possibly 0.0015 of mid phos might do. Simulated lab testing will give a better answer. Field testing is the only real answer.
James Watts- Navarre, Florida
2003
Second of two simultaneous responses
It's not clear to me if the motors are made of aluminum, steel, or a mix.
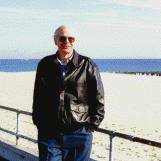
Ted Mooney, P.E.
Striving to live Aloha
finishing.com - Pine Beach, New Jersey
2003
The motor has a cast aluminum commutator cap and a a cast aluminum nose cap. The center section is steel which has magnets attached inside.
Sid Tryzbiak- Tulsa, Oklahoma
2007
Because this is a mix of metals in a very corrosive environment, I do not think any organic coating alone will prove sufficient. The Ivadizing you do before painting means that if the paint is scratched, the scratched area has the sacrificial protection of the Ivadized pure aluminum coating to protect it.
Jim is right that electroless nickel might do the job and be more available, but considering the rampant corrosion pervasive on salt water boats, and speaking as a former recreational boater, customers would have a hard time believing that the corrosion resistance of your motors is "too good".
Mooney's Law: Cost reduction programs are always ultimately a failure because they are proceed from the premise that the quality is too good or at least good enough, which is never the case and never will be (only personal opinion, but based on 40 years of diverse industrial and management consulting experience which never once disproved it). So look for better surface finishes and they may end up being cheaper. Good luck.
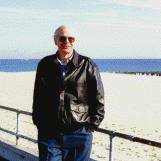
Ted Mooney, P.E.
Striving to live Aloha
finishing.com - Pine Beach, New Jersey
2007
Q, A, or Comment on THIS thread -or- Start a NEW Thread