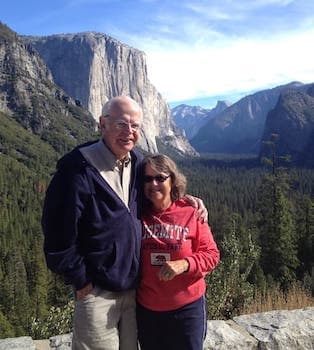
Curated with aloha by
Ted Mooney, P.E. RET
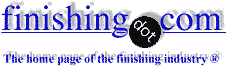
The authoritative public forum
for Metal Finishing 1989-2025
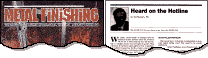
-----
Shock absorber pitting
2003
Our BE students are doing a project on corrosion in shock absorbers in coastal areas. While the shock absorbers on two wheelers are OK in interior areas, in coastal areas these show pronounced pitting corrosion. The shock absorbers are made of tube steel and hard Cr plated. CASS test requirements are 72 Hours and minimum 8 rating. Actual results obtained are between 16 to 48 hours and rating of 6 to 8 only. To improve corrosion resistance, following two methods were suggested after reviewing literature:
1) Removal of 10 microns after plating
2) Incorporating some Nickel in the hard chromium plating.
Question is:
1) Which of above or both methods will mitigate pitting corrosion
?
2) If Ni is to be added, how much percentage without affecting mechanical properties ?
3) Any other solution that has been tried and used ?
MS Ramaiah Institute of Technology - Bangalore, Karnataka, India
2003
I don't understand your first approach: remove 10 microns of what, and why?
Yes, nickel plating will help. But nickel is not mixed into chrome, it is plated before chrome. Ideally the parts should be electroless nickel plated, then chrome plated, and they will not pit at all. However, it's easier to say this than to develop a properly functional plating cycle to achieve it :-)
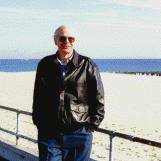
Ted Mooney, P.E.
Striving to live Aloha
finishing.com - Pine Beach, New Jersey
Q, A, or Comment on THIS thread -or- Start a NEW Thread