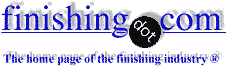
-----
Effects of chlorine on bronze sand castings
Q. If a bronze sand casting is not nickel & chrome plated properly, what would be the effects if the casting was submerged in chlorinated water?
Thomas Chianesecastings - Mt. Vernon, New York
2003
A. From my old days in Corrosion 101, sometimes coating an active metal (i.e. anode)with a deficient passive layer (i.e. cathode) is worse than leaving the part uncoated! Small anodic areas, such as a pin hole of bronze (copper-tin) exposed through large cathodic area (nickel-chrome) greatly accelerates the corrosion in the area of the pit (or crack, scratch, or other means of exposing base metal). One obvious suggestion, assuming that pits in the casting may be the cause of the corrosion is to vacuum impregnate the castings following machining to seal the pits. Pits are notorious for leading to problems, especially after plating since they adsorb corrosive plating solutions which in themselves can initiate and accelerate corrosion. Contact my firm if you wish to further explore the possibility of resin impregnation of the castings. Consult MIL-STD-276 for a brief discussion of impregnation.
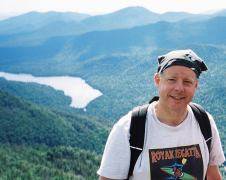
Milt Stevenson, Jr.
Syracuse, New York
2003
Q. I am considering to have work performed that includes replacing a "nickel-resist" shaft end-seal component with a similarly designed bronze material. The bronze material is of a non-contact design that may be submerged in water most of the time while in service. This water has been tested and resulting in containing chloride counts at approximately 125 ppm. Discoloring is expected.
Would the bronze material be suited for this type of application?
water reclamation district - lockport, illinois, usa
July 27, 2012
Q, A, or Comment on THIS thread -or- Start a NEW Thread