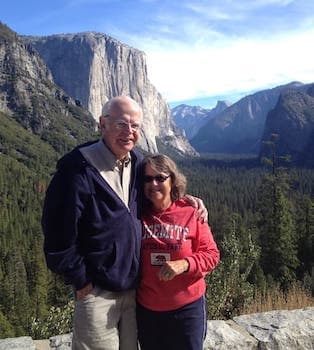
Curated with aloha by
Ted Mooney, P.E. RET
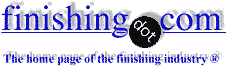
The authoritative public forum
for Metal Finishing 1989-2025
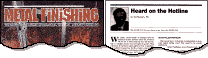
-----
The cleaning of ferrous metals before powder painting
I have a question regarding the need to assure the correct cleaning of steel plates and other ferrous materials before do the powder painting. My concern is with the emulsion cleaning usually a solution of phosphoric acid, organic solvents, and others to provide a phosphate layer in the surface of the material. I have troubles with the parameters of the emulsions and consequently problems withe the adhesion of powder paints. How the temperature and the pH of the emulsion in the soak tanks are important to the adhesion of painting?
António Ferreira- Aveiro, Portugal
2003
2003
Dear Antonio, controlling the parameters of ALL procedures within your paint system is of importance. Without documented control, improper cleaning and phosphatizing can occur, the same will happen in the coating application area. Some areas to control within the pretreatment area would be:
- · Line speed
- · Temperature
- · Part hang configuration
- · Nozzle velocity, pressure
- · Nozzle type
- · pH
- · Bath concentration level
- · Rinse water criteria
- · Floats
- · Bath/Water levels
- · System design
- · Temperature
Each of these parameters need to be checked at various times in order to maintain the parameter/s. If any of these parameters changes, the potential outcome will be topcoat failure. The failures (or reduced topcoat adhesion) will continue as long as your parameter specifications are out of control. For instance, if the line speed is too fast, your substrate may not be adequately cleaned or phosphated, which means that you will not be applying a phosphate evenly or may not apply phosphate at all. If the line is too slow, the system may apply too much phosphate and the topcoat will suffer.
Temperature of your system can make dramatic changes upon your substrate and the tests performed upon them. The pH of the bath will change as the temperature is increased and will work more aggressively. Generally speaking, hotter cleaning baths work better upon harder soils. The wetting agents react better, however, there are many newer products on the market that do a great job at low temperatures and save you fuel. You also, need to be aware of whether the cleaner is alkaline or acidic in nature, because you may damage the substrate if it is aluminum etc because of the aggressiveness of the chemical. Make sure that your part is adequately hung so it sees the water impingement from the nozzle or that it is submerged in an agitated bath for aided cleaning. Make sure the parts don't hold liquids or drag liquids from bath to bath.
Your nozzles should be checked to make sure that they are not worn out and they are properly aligned and not plugged. Make sure the nozzles are designed for the type of cleaning necessary for your substrate. Generally, the harder the pressure, the better cleaning will occur, but remember that too much pressure will also make parts fall of the line. The nozzles used within your phosphate bath do not need hard impingement, but rather simply to be applied to your substrate and let the chemical let it work itself. The only time I use high pressures within a phosphate stage is when the particular stage is a combination cleaner/phosphatizer. Remember that if there is no cleaning, there is no phosphatizing reaction.
The pH of the bath is particularly critical. The pH in a cleaning stage can be important especially if you are cleaning aluminum type substrates. Since aluminum does not accept a phosphate coating the same as does steel, it is important that it is properly etched for it to achieve proper adhesion. The pH within your phosphate stage needs to be controlled so that even distribution of the complete run is achieved. Too weak of pH will give spotty and unprotected areas of phosphate coating. Too strong of pH can cause areas to be burned or leave a phosphate film upon the surface, which will dramatically reduce your topcoat performance, not to mention wasting your chemicals and the time spent in the system.
The various baths need to have the proper amounts of each chemical supplied to them and they need this maintained throughout the process. Too little surfactant --cleaners¸ will hamper cleaning, whereas too much surfactant will not aid in cleaning, but rather only reduce your bank account. The phosphate stage will do the same, except that too much phosphate will reduce topcoat performance. Maintaining proper rinses throughout your system is of importance because without adequate rinsing, the parts may drag chemicals form stage to stage, thus contaminating them and/or neutralizing them and making them less effective. It is also important that the final rinse be controlled as the Total Dissolved Solids (TDS) in your rinse water is left upon the part prior to the topcoat application and this may lead to reduce or premature topcoat failure. This is why many companies use Dionized or RO water purifications systems.
Your system needs to be checked consistently and documented to insure you maintain all the parameters. If you do maintain these checks and balances, it is much easier to troubleshoot problems should they arise. The baths need to be maintained indefinitely. Maintenance of the entire system should be performed to help insure itsã function. Make sure your baths and tanks are cleaned in a routine fashion. Each of the various parameters can be adjusted to help in certain soils or metals achieve proper adhesion. Your chemical supplier is your best choice to help you set control parameters. Let them determine what soils are to be removed and help setup proper chemicals and control specifications.
Lastly, I believe that it is also important that éANY¸ employee who is employed to maintain the system be taught everything about the system. It is not enough to understand that you need to add a chemical and bring it up to meet the specifications set up by your chemical supplier, but also why it needed the chemical addition. For instance, your employee/s see that the pH and concentration level is weak in your phosphate stage so he/she adds chemical, but fails to see that the float is sticking and the tank is overflowing with water. This happens frequently and can be a huge cost factor as well as producing product failures.
![]() Bob Utech Benson, Minnesota |
![]() Ed. note: Bob is the author of: "High Performance powder Coating" on eBay or AbeBooks or Amazon [affil links] |
Q, A, or Comment on THIS thread -or- Start a NEW Thread