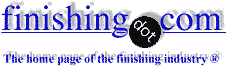
-----
Corrosion inhibition about phosphoric acid
I am from an engineering company in Hong Kong and got a cast iron cannon right now which shall be treated with a phosphoric acid-base corrosion inhibitor for the corrosion inhibition. I know that phosphoric acid is a good solution for forming rust protective layer. However, I want to know what's the concentration of the phosphoric acid to be and how long should I put the cannon in the acid. That is quite urgent right now and should any one help?
Elaine Yung- Hong Kong
2003
2003
Dear Elaine,
As far as I know Phosphoric Acid alone is not a passivation solution for Cast Iron even if you will leave the cannon in the solution forever. Try to consult with one of the experts in the present site for the best passivation process for it.
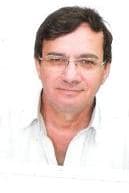
Yehuda Blau
YB Plating Engineering and Quality - Haifa Israel
Hi Elaine!
I believe that the acidic based phosphate will work adequately. You don't state if you are applying a topcoat upon the canon soon or not? In general, most acids work fairly aggressively upon cast iron. I would ask your chemical supplier to aid you in finding the most preferable concentration level for your project, but I believe that around 2.5-3.0 percent concentrate would be advisable. Have your chemical supplier advise you upon the time and temperature of the bath also. Then test your substrate for performance before making the entire run. I would also make sure that you use an acceptable sealer to insure stability of the phosphate and to make sure that there are no areas left non-phosphatized. Make sure you properly rinse the substrate as it leaves the pretreatment system.
It might be advisable to check the porosity of your substrate prior to cleaning to make sure your control parameters complete an adequate cleaning before the phosphatizing stage. This will insure that the substrate receives proper phosphatizing (remember that no phosphatizing will occur if the part is not clean) and that off gassing due to soils and/or surfactants remain upon the part can be kept in check.
![]() Bob Utech Benson, Minnesota |
![]() Ed. note: Bob is the author of: "High Performance powder Coating" on eBay or AbeBooks or Amazon [affil links] |
Q, A, or Comment on THIS thread -or- Start a NEW Thread