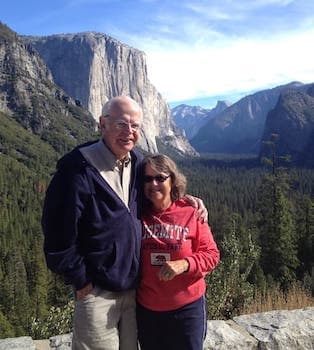
Curated with aloha by
Ted Mooney, P.E. RET
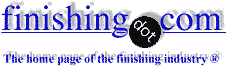
The authoritative public forum
for Metal Finishing 1989-2025
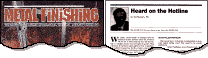
-----
Blisters after zinc plating 12L14 & 1215 steel
2003
Q. We have a machined part which undergoes surface treatment (rainbow zinc)
The base material is steel, zinc is then electroplated on, and then chromium is added on finally via electroless plating.
Note that the above process is acid based .
We have two problems:
a) we dipped the finished part into plain water, and after a day, we noted that the chromium disappeared, leaving only the zinc behind. Is this normal (i.e., the chromium seem to be water soluble?)
b) We have been having some corrosion problem. (see attached pic). Typically, there are 2 scenarios:
1) blister appears 2-3 hrs after completion of plating.
2) no blister seen , but 2 months later, blister appears.
Plater has tried reducing the brightener, but that does not seem to help.
Tumbling of parts (through deburring process) was also done, but did not seem to help.
Spec is as follows:
Base material: AISI 12L14 or 1215.
Finish: Zinc Plate per ES-572, para 3.1.1.1.8, Type ii, .0001 to .00025 thick. Plating process complete by acid base.
What do you think is causing the blister?
Yeang Hoong Keng- Malaysia
2003
A. Yeang,
12L14 steel has Lead. This makes it softer to machine but it creates another problem, blisters.
Your problem comes from a bad preparation (cleaning).
You should use an acid salt after alkaline cleaning.
The intention is not to bring more lead to the surface.
The chrome in the final finish can be damaged by water, even more if it's done immediately. Chromates need to dry, or cure, at least 24 hours. Why immerse the parts in water?
Good luck
Enrique
Enrique Segovia- Monterrey, Mexico
A. First let me agree with Enrique Segovia, you might have a cleaning problem, second, do you buy or mix chromium ? I have tried to mix a chromium compound myself and ran into exact same problems with water solubility. Try to buy from a supplier in your area.
Good luck,
Bo Kønig- Odense, Denmark
2003
2003
Q. Dear Mr. Segovia/Mr. Konig:
Thank you very much for your response. My answers are as follows:
a) Why we immersed in water...it was just an experiment to see how the part responses in water. Malaysia is a humid country, and if we send by ship to our customer, it will be many weeks on the high sea. We just wanted to see the effect of 100% humidity (ie, water) on the chromate.
b) We cannot buy or mix the chromium as this is part is processed by a sub contractor (ie, not inhouse)
c) However, I have taken the advise from both of you that possibly it is due to poor cleaning. We have audited the supplier's facility and is now verifying whether cleaning is the cause of the problem..
Again, thank you for your response.
Best regards,
Yeang Hoong Keng [returning]- Malaysia
A. In the preplate process (cleaning and activation) a fluoroboric acid dip should be included before plating to remove lead from the surface. Lead is not soluble in other acids. This should end the blistering presuming it is not related to poor cleaning prior to acid dip.
Gene Packmanprocess supplier - Great Neck, New York
2003
Q, A, or Comment on THIS thread -or- Start a NEW Thread