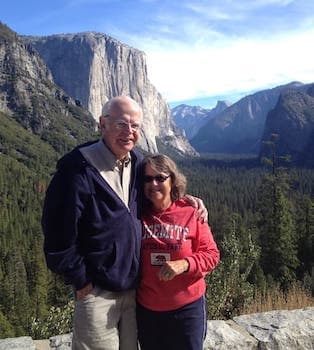
Curated with aloha by
Ted Mooney, P.E. RET
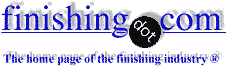
The authoritative public forum
for Metal Finishing 1989-2025
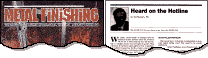
-----
Is there a coating to reduce stiction force in a heavily oiled valve?
I am having trouble overcoming forces in my high school project and it makes me use extra energy that I can use for other things. I am trying to quickly open and close an oiled valve, but I am having difficulties using too much energy and my advisor tells me that most likely it is "stiction". He recommended that I look in the internet to see if there was some coating or other method that could be used to reduce this force, but all I have found refers to computer and miniature equipment (MEMS). The valve is a stainless steel disk about one-inch (25 millimeter) in diameter and about 0.020 inch (0.5 millimeter) thick; it travels around 0.25 inch (6 millimeter).
Raphael- Lincoln, Nebraska, USA
2003
MEMS is Micro ElectroMechanical Systems and is not directly relevant to your problem. MEMS is a manufacturing method for making parts that are only a few microns big, so they are virtually invisible to the unaided human eye. In MEMS, lubricants can act against the system by generating drag. Your problem is on the conventional engineering scale. There is little information about what you re actually trying to do, so we have to guess. How fast is "quickly open" - are we talking in terms of 1-10 times a second or 10,000-100,000 times?. You say the valve is heavily oiled - is it bathed in oil or is this because you want it well lubricated? If it is in a bath then you will have a lot of problems from viscosity. Lubrication usually works by having a thin film that allows surfaces to glide over each other and too much lubricant can actually increase the drag. You may find it better to reduce the amount of lubricant being used. Do you need a "wet" lubricant or can you use a dry one?
These are often better as they do not have so much drag, so one option may be to coat your surfaces with PTFE ("Teflon"). An alternative approach may be to make the valve electromagnetic and use an oscillating current to open and close the vale by reversing the magnetic field. You can then alter the frequency of operation by altering the a.c. frequency.
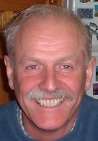
Trevor Crichton
R&D practical scientist
Chesham, Bucks, UK
2003
Never heard of stiction. The normal way to reduce the force is to reduce friction. Since you are oiled, try reducing the valve stem or opening up the hole it passes thru.Alternatively, you can reduce the backpressure on the valve head or reducing the head size.
James Watts- Navarre, Florida
2003
2003
Trevor,
I don't quite agree that MEMS covers only items that are virtually invisible to the naked eye, although it does imply the need for exceptionally small features which may well be. I was just looking at the July 02 issue of Smithsonian while at the barber shop today, wherein a MEMS gas turbine built of silicon is described; the overall assembly is a bit larger than a quarter. I make mention of this here because it is a very accessible reference for student in the USA.
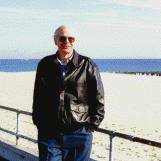
Ted Mooney, P.E.
Striving to live Aloha
finishing.com - Pine Beach, New Jersey
2003
James,
Friction refers to the resistance to motion as one surface slides over another. Stiction refers to the (higher) force necessary to start the sliding action in the first place, that is, to break the stationary "sticking" of one surface to the other.
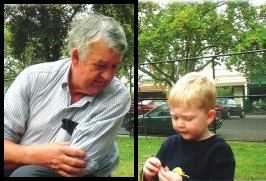
Bill Reynolds [deceased]
consultant metallurgist - Ballarat, Victoria, Australia
We sadly relate the news that Bill passed away on Jan. 29, 2010.
Thanks Bill. The name even sort of says that. It definitely is new to me.
James Watts- Navarre, Florida
2003
2003
Ted,
Thanks for the update on MEMS technology. I was not aware that it had been put into such large objects. The essential thing about MEMS is that the technology has allowed the development of microscopic parts that function just like their bigger brothers would. Fabrication of these microscopic parts would not be possible by conventional machining, but fabrication by material deposition does make it possible as long as the template has sufficient dimensional resolution. These extremely small parts can then be built into something much larger and more visible. I suspect the gas turbine you describe is one such product. The problem with microscopic parts is that conventional engineering concepts such as lubrication suddenly become turned on their heads and the reverse happens; lubricants exert surface tension and its impact is detrimental to the movement of the parts. "Stiction" is often used in conjunction with dynamic friction.
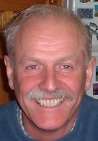
Trevor Crichton
R&D practical scientist
Chesham, Bucks, UK
Could the stiction be caused by an oil that is too high in viscosity? Maybe try a lighter (or thinner) oil that won't adhere as strongly. Be sure not to add any polymers that might alter the lubricant (i.e., STP Oil Treatment [affil links]).
Dan Brewerchemical process supplier - Gurnee, Illinois
2003
Q, A, or Comment on THIS thread -or- Start a NEW Thread