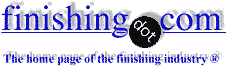
-----
Length of time it takes for SS to become passive after passivation
There seems to be varying opinions on the length of time it takes stainless steel to become passive after removing it from the nitric bath during passivation. Looking for professional opinions or hard data that verifies the length of time.
Brian Sanders- Bradford, Pennsylvania, USA
2003
I have seen times from one hour to 24 hours mentioned in the literature over the years. There are so many variables that hard data would be useless if there were a way to quantify the level of passivity accurately in the first place. This is one of those queries that begs the question:"Who cares?"
Dan Weaver- Toccoa, Georgia
2003
2003
The subject of chromium dioxide formation times is of importance to me, as I manufacture ASTM F138 316L esr vm objects that will be placed directly into human flesh and remain there, possibly forever.
My schedule is very tight and I have delivered objects that were still warm from the rinse water after passivation. I inform my customers that the full effect of passivation is not finished until the steel has been idle in air for 24 hours, OR, it has been subjected to an oxygen-rich atmosphere for 1 hour.
The reason for the times I specify is; the product will have to be immediately subjected to autoclave sterilization, (heat, pressure, and harsh chemical fumes), then subjected to the inside of the human body (a rather nasty place where O2 is confined to the inside of red blood cells, and not available to the steel surface),
The function of the oxygen is essential when one wishes to see a rich "oxide layer" accompany their product. This can be achieved by anodizing the stainless steel, during which, the anode is oxygenated at the surface.
Electropolishing will, of course, provide the same action, and passivation occurs during this process also, although a post-pickling passivation process is still usually called for with both of these processes. Although it seems redundant, the pickling will help the removal of any residual acids, and unwanted oxides from previous steps.
I have seen passivity occur within 1 second during a few tests on pickled-only products, the layer is very thin, and seems to become more evident with age, with no outgassing after about 24 hours.
Generally, if your part is not subject to immediate surface strain, then 24 hours in air (not sealed in a container unless it is filled with O2 gas) will do you just fine. Coloumetric thickness testing proves to be quite accurate when attempting to measure chromium oxide, as well as the reagent surface drop test. Hope this helps you out!
Jeff Swayze- Kelowna, B.C., Canada
Current theory on passivation of stainless steel indicates that formation of the passive layer is completed within the passivating solution. This is probably only true for oxidizing acidic solutions and cases where an anodic potential is applied to accomplish the passivation. Recent in situ studies published in the Journal of the Electrochemical Society in 2001 by A. J. Davenport et al. and L.J. Oblonsky and M.P. Ryan show that preferential removal of Fe & Ni atoms occurs concurrently with formation of a chromic (hydr)oxide surface matrix.
Note that none of the passivation specifications require any time delay prior to testing.
I agree with Mr. Swazye that exposure to air/oxygen is needed following pickling in a reducing acid. A monolayer of chromic (hydr)oxide is expected to form ~immediately during rinsing, then further thickening of this layer is expected to become slower and slower according to the parabolic rate law, i.e., rate proportional to the square root of the oxidation time.
Ken Vlach [deceased]- Goleta, California

Rest in peace, Ken. Thank you for your hard work which the finishing world, and we at finishing.com, continue to benefit from.
2003

this text gets replaced with bannerText
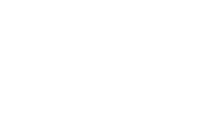
Q, A, or Comment on THIS thread -or- Start a NEW Thread