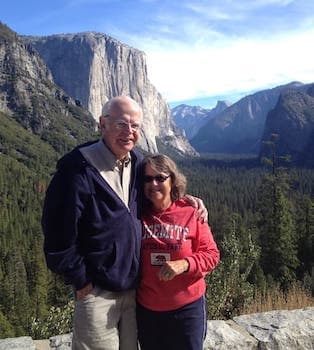
Curated with aloha by
Ted Mooney, P.E. RET
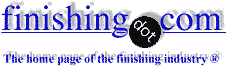
The authoritative public forum
for Metal Finishing 1989-2025
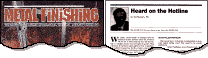
-----
Yellow dichromate adhesion problems on large zinc plated parts
We are commercial job shop platers. We are having difficulty with adhesion of yellow dichromate on the zinc plated surface of large parts (1 square foot and larger)plated on our hand line. The parts look good when we ship, but the customer leak tests the parts in a soap/water solution. Afterwards, the yellow can lose adhesion and be rubbed off.
We have tried adjusting temperatures. We run zinc at 80 °F; Chromate at 90 °F.; We use a nitric acid dip prior to chromating at 100 °F. Final hot rinse at 120 °F. We are using an acid based zinc from Lustron, and their Yellow as well. We use the same chemistry in our barrel lines, but don't seem to have the problem on small parts.
Suggestions? Anyone suffer this problem before?
TIA,
- Newark, New Jersey
2003
Dear Bart,
If I were you, I would just try simple hull cell with subsequent chromating. You may want to vary your chromate timing. Replace the bath if it is too old. Vary the temperature in chromate,try little lower temperature. All this you can do through hull cell without wasting much chemical and then try the same leak test or soap solution test on the panel. Make the change accordingly to your bath. I bet you it will work.
Regards,
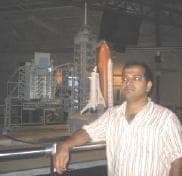
Hemant Kumar
- Florida, USA
2003
First of two simultaneous responses --
Look for organics in the zinc. Too many will make for the problem you're experiencing. Good luck ....
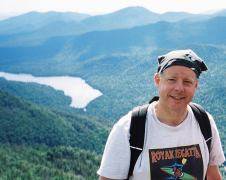
Milt Stevenson, Jr.
Syracuse, New York
2003
Second of two simultaneous responses --
1. First treat the acid zinc solution for removal of iron.
2. Then on the side in a bucket, try 1/2% Hydrochloric Acid instead of Nitric.
As you know iron in the zinc deposit affects the chromate and you also know that the wetters in acid zinc are very difficult to remove. Sometimes I have had to go back into an alkaline cleaner and then HCl before some of the more sensitive post treatments.
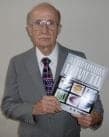
Robert H Probert
Robert H Probert Technical Services

Garner, North Carolina
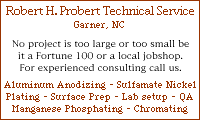
2003
Hi,
Brightener or organic contamination in the zinc plating solution can also cause the chromating problem.
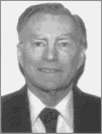
Don Baudrand
Consultant - Poulsbo, Washington
(Don is co-author of "Plating on Plastics" [on Amazon or AbeBooks affil links]
and "Plating ABS Plastics" [on Amazon or eBay or AbeBooks affil links])
2003
2003
You say they are using a soap/water solution to test? How hot is the water and what kind of "soap" do they use? Where did that test come from? As with any type of test the parts have to be allowed to cure for a minimum of 24 hours to allow the chromate film to
"set-up".
All the answers are correct. Another thing to consider is not run the zinc bath full bright, like it needs a brightener addition.
tech svc. w/ chemical supplier - Grand Rapids, Michigan
Everyone is giving you the right answers. Some are causes to try to correct, others are ways to overcome the cause. In some cases a pre-dip in 1% sulfuric acid works better than nitric or HCl for yellow on acid chloride zinc. In a pinch you can try chromating first in a blue bright (trivalent preferred) then rinse and yellow. The blue bright chromates usually contain chlorides and fluorides which are aggressive enough to remove organic films from the surface. There are also proprietary acid salts available to help overcome this type of problem. Generally, they are based on combinations of citric and sulfamic acid with sodium nitrate ⇦ this on Amazon [affil link] .
Gene Packman- Syosset, NY
2003
My company is experiencing a dichromate adhesion problem with powder paint sloughing off after paint cure. We sent samples to an independent lab for review and the results were plating related. I would like to know what formula to use for a soap leak test to test our dichromate plated parts before paint.
Bill Hartline- Monett Missouri USA
August 18, 2011
Q, A, or Comment on THIS thread -or- Start a NEW Thread