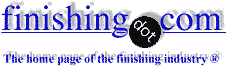
-----
WROUGHT IRON FINISHING PROBLEMS
2003
We are a manufacturer of wood furniture, introducing wrought iron components. A few months ago I had wrought iron sand-blasted in my shop and then transported 5 miles away to an auto body shop, in a trucktopper. After paint manufacturer recommendations, he applied a 2 step clear wet urethane finish. My problem is: Soon after, I began to see rust veining under the urethane. My questions are: Was the problem that auto body steel and wrought iron need to be treated differently? Or was it the urethane sealer and clear coat that failed? Or was it the transferring the metal from shop to shop, and being put under heat lamps causing the metal to sweat and moisture being trapped under the urethane finish? I'm hoping to cure this problem by doing the sand blasting and spraying in the same shop with the least amount of time between as possible. And then using a standard auto body application using acid primer and a pewter-colored paint and a clear coat.
Please, if any one can help me with a fool-proof system...I can't afford to have this happen again.
Thank you!
- Michigan, USA
Coating protection is like a tent supported by three poles:
1. the surface condition;
2. the selected paint,
and 3. the application itself.
If any one of these poles is weak and breaks, the whole tent collapses and the protection it provided is gone. Anything that affects the ability of the surface to receive and hold on to its coat of paint will profoundly affect the durability of the whole system. The majority of paint failures are undoubtedly due to insufficient or unsatisfactory preparation of the metal surface. Remove all oils, soils, etc., then remove chemical impurities like rust, mill scale etc., and bring the surface to a non-metallic, non-conductive first. Make sure that the surface is bone-dry, and then apply the right type of paint.
Chennai, Tamil Nadu, India
2003
Q, A, or Comment on THIS thread -or- Start a NEW Thread