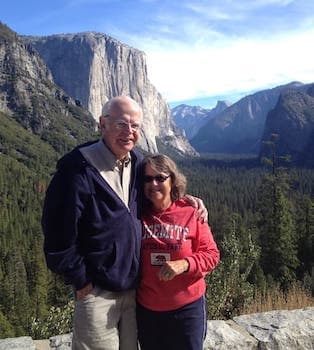
Curated with aloha by
Ted Mooney, P.E. RET
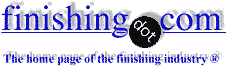
The authoritative public forum
for Metal Finishing 1989-2025
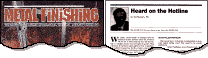
-----
Rack marks and MIL-A-8625 anodizing
Q. WE ARE HAVING SOME PROBLEMS IN HARDCOAT (HARD ANODISING).
IN ANODISING PROCESS WE ARE JIGGING WITH RACKS TO GET ELECTRIC CONTACT FOR THE PROCESS. THAT CONTACT AREA IS NOT COATED, SO A WHITE MARK IS THERE. TO MAKEUP THAT TO ANY NEAR GRAY OR BLACK COLOUR WE WANT SOME CHEMICAL TOUCHUP OR ANY SOLUTION WHICH CAN BE APPLIED AFTER ANODISING TO THE UNCOATED AREA.
THANK YOU.
- India
2000
Q. I have an Aluminum Alloy plate (2" x 6" x 0.1" thick) that needs to be Anodized per MIL-A-8625 / MIL-PRF-8625
[⇦ this spec on DLA]. The specs. clearly stated "surface free of scratches" but my plater is recently shipping me parts with minor scratches which they claimed to be marks due to the electrode clamp. They said the mark will "always be there". The single scratch mainly occurs on the edge but sometimes rolls over and appears on the surface of the plate.
Can someone share if this can be avoidable? What should be the rejection criteria according to MIL-A-8625?
Any comment is appreciated.
Regards,
- Vancouver, British Columbia, Canada
2003
A. Rack or contact marks are required for anodizing. MIL-A-8625 addresses this issue in Para. 3.13.1 Contact Marks and Para. 6.14 Size of Contact marks. You will need to work with your anodizer to find an acceptable racking method.
Chris Jurey, Past-President IHAALuke Engineering & Mfg. Co. Inc.

Wadsworth, Ohio
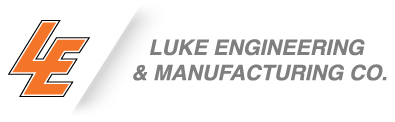
2003
A. MIL-A-8625 (as does the AMSA8625) allows for "rack marks" and permits touch up with "chem film"...see MIL-C-5541 (or AMSC5541 ...by brushing the solution (aka "Alodine", "Iridite" or other proprietary chemical solution...see the QPL. You can download the "MIL" specs and QPLs from DODISS / "ASSIST"). But it sounds like your subcontractor is trying to pass off scratches for rack marks. The rack marks should be reasonably consistent part to part. He may truly be scratching your hardware. Check your hardware geometry against his racking procedure and handling practices. Are you doing chromic acid, sulfuric acid or hard-coat anodizing? That is, which "Type" do you spec?
Doug Hahn- Mason, Ohio
2003
A. Depending on the finish in question. Sulfuric Type II, Sulfuric Type III (Hardcoat), or Chromic Type I, your racks marks can and will generally speaking vary.
At least with hardcoat anodizing (Type III) the surface area needed for sufficient current requirements can be pretty substantial depending on the size of your part. Most rack marks are going to be approximately the size of 1-2 pencil lead points in width, if the racks are titanium.
I've used 1/4-3/16" aluminum also on very large parts, and the rack marks associated with them can be just plain horrendous in size but, because of the size of the part, they are still within MIL spec. I believe somewhere in the specification there was a way to determine a pass/fail on rack marks such as X number of marks in a Y * Z square would pass or fail. But its been a few months since I read the spec, so I could be wrong. My suggestion is first talk to your supplier, see if there is an alternative method for racking. If he suggests the purchase of racks to solve the problem, weigh the cost and see. Most "stock" racks can satisfy 90% of racking requirements, and they are not all too overly expensive and the costs associated with your purchasing them can be absorbed quickly, and the benefits noticed immediately upon the change because rack marks can AND SHOULD be hidden as much as possible if the situation presents itself as being able to be done that way. But not everything is perfect, if it cannot be done to eliminate the problem, see about ways to at least minimize it.
plating company - Toledo, Ohio
2003
Q. Hi,
I'm looking for an option to rack hard anodizing parts. Currently, we are using annealed Al wire to rack it which it takes a lot of space and some causing burns. Previously, we have tried using Ti rack which shows unsatisfactory results, as there were jig marks.
Is there any other solution that might help us to improve this?
Thank you in advance for your response on this matter.
Aerospace Manufacturer - Sungai Buloh, Selangor, Malaysia
January 12, 2015
A. A picture of the part would help a lot. Have you contacted your customer to inquire where racking marks would be acceptable? Are there threaded holes on the part that you could use to make contact, either with Ti or Al bolts?
Anodizing racks are available in many, many, different configurations, both in Ti and Al. The larger rack making companies will also custom design something for you, if necessary, after discussing with your customer on where marks would be acceptable. It's a resource you should consider using.
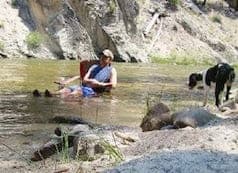
Marc Green
anodizer - Boise, Idaho
January 16, 2015
----
Ed. note: Readers may also be interested in letter 6109, "Hard Anodizing racking problems"
Minimising Jig contact points on Anodising
Q.
Hello All,
We anodise large heavy aluminium plates. Normally we clamp them top and bottom leaving on some occasions large jig contact marks. Can anyone please offer a suggestion as to the best method for jigging this type of part.
It measures: 18" x 15" x 0.5"
I am attaching a image of a similar plate with holes, but the plates we are having problems with have no holes.
Nigel BellProcess Technician - Northern Ireland
August 14, 2015
A. Can you use the two diagonal holes as a jigging point for Aluminium plate. Finally hole touch up is covered by MIL-A-8625.
"6.10.1.1 Holes. In the case of small holes and tapped holes, coating thickness can vary from no film to a full normal coating. Holes, both tapped and not tapped, over 1/4 inch should be anodized. Parts with Type II coatings, external or internal, with a total tolerance of 0.0004 inch or less, if lapped, honed or stoned to size after anodizing, should be subsequently treated with QPL-81706 materials to provide surface protection.
Discoloration on the surface that has been sized is acceptable (see 6.6). The designer is cautioned to require adequate thread and hole sealing operations in subsequent assemblies as may be required to produce the necessary corrosion resistance."
- united kingdom
July 18, 2018
Hi Loka. Thanks for helping but, the component which Nigel is actually having trouble with doesn't have any holes :-(
Regards,
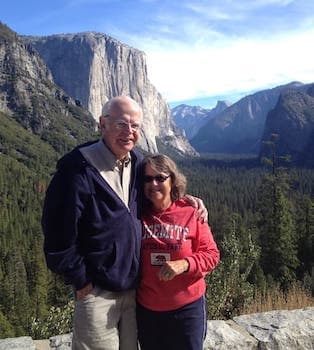
Ted Mooney, P.E. RET
Striving to live Aloha
finishing.com - Pine Beach, New Jersey
July 2018
Q, A, or Comment on THIS thread -or- Start a NEW Thread