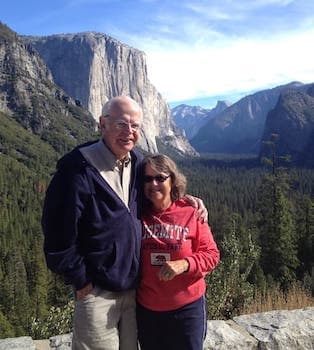
Curated with aloha by
Ted Mooney, P.E. RET
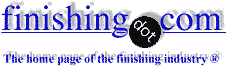
The authoritative public forum
for Metal Finishing 1989-2025
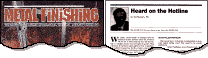
Thread 192/25
Blisters on Electroplated Zinc Items
We cast small sized giftware items in zinc alloys which are buffed/polished, cleaned and electroplated. We do not have a ultrasonic cleaner yet but take great pains to clean the articles thoroughly before our online electrolytic cleaning and electroplating. However, despite our efforts we find that many of our castings develop 'blisters' within a few days of their plating. We heard that oven heating the parts prior to buffing and electroplating help, so we now heat our articles after casting them at temperatures of 300C for about 3 hours. Although the blisters seem to have reduced they are still developing on some pieces after a few days.
Any advice to fully overcome this problem would be highly appreciated.
- New Delhi, India
2003
publicly reply to Aloke Mookerjee
Your only hope is vacuum impregnation or perfect castings. If you can see "cold shuts" you must expect blistering.
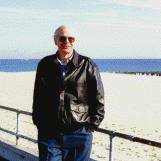
Ted Mooney, P.E.
Striving to live Aloha
finishing.com - Pine Beach, New Jersey
2003
publicly reply to Ted Mooney
Thank you for your response re. blisters on cast zinc alloy pieces. We cannot guarantee 'perfect' castings yet so I shall appreciate it if you would explain what 'vacuum impregnation' is or tell me where I could gather detailed infornmation of this process.
Thank you,
- New Delhi, India
2003
publicly reply to Aloke Mookerjee
Concerning my problem with blisters on nickel plated zinc alloy castings, Ted Mooney advised vacuum impregnation (apart from a perfect castings which I cannot guarantee) as the only solution. Can anyone please tell me more about this process?
Thank you.
- New Delhi, India
2003
publicly reply to Aloke Mookerjee
Some manufacturers you may want to try to reach include Blazers Process Systems, Epoxylite Corp., Loctite Corp. and Ultraseal America, Inc. We cannot print further contact info for these companies.
I perhaps exaggerate in saying you need "perfect" castings, but if you can see defects, you won't be able to plate them without impregnation. An intermediate solution is to "mush buff" copper into the pores. In other words, after copper cyanide and bright acid copper plating, rebuff the castings before continuing the process.
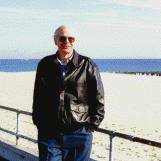
Ted Mooney, P.E.
Striving to live Aloha
finishing.com - Pine Beach, New Jersey
2003
publicly reply to Ted Mooney
First of two simultaneous responses --
Dear Aloke:
Are you adding some de gassing additive during casting if not try it. Once my customer faced same problem and I bought him out by the same.
All the best,
- Ajman, U.A.E.
2003
publicly reply to Qutub Saify
Second of two simultaneous responses --
Dear Alok bhai,
Why don't you try ultrasonic cleaner. We had the same problem and we just bought an ultrasonic through an auction. Situation improved dramatically. Well cleaning of casting is not an easy job. May be you want to scotch brite your parts manually, before going to the Zinc bath. Just a suggestion.
Good luck,
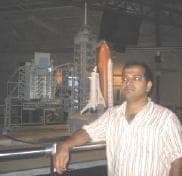
Hemant Kumar
- Florida, USA
2003
publicly reply to Hemant Kumar
Dear Mr. Aloke ,
The problem you are facing is due to the fact that during the cleaning process prior to electroplating , the acid ( cleaning agent
) gets deposited in the micro porosities of the castings .
After plating the acid deposited in the micro porosities try to come out and affects the aesthetics of the components .
The solution is to fill the micro porosities( using Loctite impregnation technology) before cleaning & electroplating . The acid will not settle in the micro porosities hence removing the root cause of the problem.
Thanking you With regards,
Speciality chemicals - New Delhi, India
2004
publicly reply to Bibhas Agarwal
Q, A, or Comment on THIS thread -or- Start a NEW Thread