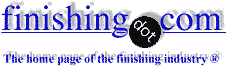
-----
Stainless Steel Railing Rust & Corrosion Problems
Quickstart: Among the discussions on this page are two where Finishing.com was honored that internationally recognized stainless steel architect Catherine Houska weighed in on the problems. Her responses are so to the point and so thorough as to leave us amazed, and to leave sculptor Randy Bolander thankful :-)

this text gets replaced with bannerText
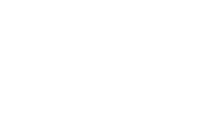
Q. Dear Sir/Madam;
Our company is a manufacturer and installer of custom railings and we have run into a large problem with one of our stainless steel projects. We have installed over 100 linear feet of 304 stainless steel rails in an outside application and are having severe corrosion problems. The stainless steel has 180 grit polish. All the rails are corroding on the top surface of the 2" dia. rails as well as around the welded spindles where ever the rain water has been sitting. It only took about two weeks of exposure to see the corrosion begin. The steel supplier is telling me that I needed to passivate the stainless steel after our polishing process with a Nitric acid dip. We were using 180 grit sandpaper to polish the welds to match the steel suppliers 180 finish. Everyone I have talked to other than the steel supplier tells me that there should be no need to passivate the stainless but only a good cleaning of the polished product should have sufficed. Is there any other means of stopping this corrosion than passivating with Nitric acid? We have power washed the rails and wiped with acetone
⇦ on
eBay
or
Amazon
[affil links] Warning! Flammable!
. It will be very difficult and costly to tear down all this railing, send out for a Nitric acid bath and reinstall. Is there a process we can use on site without having to remove the rails?
Please help!
Thank you for your time.
- Walled Lake, Michigan
2003
A. Hi Thomas. Yes, passivation needs to be done, but it can be done in situ. You can do it yourself or have it done with citric acid; or you can retain a professional to do it with the more dangerous nitric acid. The sooner the better because once pitting starts it's more difficult. Good luck.
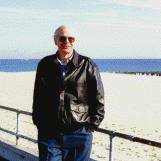
Ted Mooney, P.E.
Striving to live Aloha
finishing.com - Pine Beach, New Jersey
A. Thomas,
What was the abrasive in the 180 grit that you finished the railing with? I have a gut feel that it was not aluminum oxide but rather a flint or iron based abrasive. It could be aluminum oxide or other abrasive embedded in the SS providing sites for corrosion to spread. I welcome feedback here. You may have to on site remove the visible rust, and doubly good on welds. Use a "Scotch bright" abrasive wheel. Clean well and use the gel citric passivate from Stellar Solutions [a finishing.com supporting advertiser].
- Fridley, Minnesota
Q. Mr. Quirt,
In response to your inquiry, all of our abrasive flap wheels used on this project were aluminum oxide wheels. We also only used stainless steel wire wheel brushes for some tight corners. Everyone I have talked to seems surprised that we are having this problem. Other people have prepared similar projects in the same manner with no troubles. I am currently investigating the material grade of the stainless to ensure that it meets the 304 ASTM A554 grade. I appreciate your responses. Keep them coming! I am trying to find out the best way to remove this corrosion without having to uninstall the railings.
Thank you,
- Walled Lake, Michigan
Q. I'm a sculptor working in stainless. I've been welding for 3 years and all my teachers have taught me to passivate stainless steel welds using picking paste or a citric acid paste and electrical stimulation. Tonight a friend of mine, a well known and established sculptor in Seattle, told me I don't need to passivate Stainless Steel at all. Your problem with corrosion on the 304 railing further adds to my confusion. Have you resolved this problem and what was the solution?
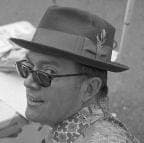
Randy Bolander
- Seattle, Washington
2003
A. There are several possible causes for this corrosion problem.
1) If corrosion becomes visible as soon as a few days or weeks after installation, the most likely cause is carbon steel or iron contamination of the surface. If it is surface contamination rather than deeply embedded particles, a surface chemical treatment can dissolve the carbon steel without damaging the stainless steel. Citric acid passivation products can be used but they are generally less effective than other options. There are Nitric acid gels which can be painted on in the field and then rinsed away. They can be tough on surrounding plants because they can be the equivalent of over fertilizing. Oxalic acid
⇦ on
eBay or
Amazon [affil links]
can be effective if you want to try an intermediate step before stepping up to a nitric acid.
contain oxalic acid and fine abrasive that will not scratch the finish. Make it into a paste, apply to the surface and let it sit on the surface for 10 - 15 minutes (giving the acid time to work) before rubbing. Thoroughly rinse off the paste. These contain some chlorides and could end up causing corrosion if not completely removed. I would suggest cleaning a small area with the product and then doing what is sometimes called the "wet diaper test". Take a diaper and thoroughly saturate it with water. Wrap it around the "clean" area. Tape to hold it in place and prevent moisture loss. Remove after 48 hours and see if the corrosion has returned. You can use a cotton cloth and wrap plastic around it instead of using a diaper. This accelerates the moisture exposure that would occur naturally over a couple week period. If there is no corrosion after 48 hours, you can assume the cleaning product will be effective. If it is not, you will have to use a more aggressive product. In the worst case, pickling or refinishing may be necessary.
2) The corrosion could also be caused by exposure to Muriatic acid (hydrochloric acid) if someone happened to clean stone, concrete, or masonry nearby. Alternatively, someone might have used a "stainless steel cleaner" on the railing that contains hydrochloric acid. There are some very questionable "stainless steel cleaners" on the market. This acid can is very corrosive to stainless steel. If this occurred, neutralize the acid with Chlor-rid ⇦ on eBay [affil links] and determine if the corrosion is bad enough to require refinishing.
3) The other common possible explanation will be dependent on the time of year when this was installed. If it was exposed to deicing salt shortly after installation, the following could be the cause. Type 304 is not a good choice for exterior applications in areas that use deicing salt or are exposed to coastal salt. It will corrode. Tube/pipe railings are often made from higher sulfur stainless and the sulfur inclusions can be sites for corrosion to start. The relatively rough finish could add to the problem, particularly if you used alumina abrasives. Always always use silicon carbide abrasives and replace them when they start to wear. Silicon carbide cuts the surface cleanly on a microscopic level which is important for good corrosion resistance. Alumina actually smears the surface on a microscopic level and those micro crevices greatly increase susceptibility to corrosion. For Type 304 to work in exterior applications exposed to salt (chlorides), you must use a very smooth finish (minimum of 240 grit but 280 to 320 would be better). Use silicon carbide abrasives, and plan to clean it every spring to get rid of salt and light staining before higher temperatures and humidity accelerate the corrosion.
Type 316 with a smooth finish is usually the best choice if you want to avoid maintenance. Stainless steel finishes and architecture are my area of expertise. I have written several brochures on selecting the right stainless steel for applications and preventing atmospheric corrosion of stainless steel for non-metallurgists. They are available free of charge from the Nickel Institute, Reference book series 11 024 "Stainless Steels in Architecture Building & Construction: Guidelines for Corrosion Prevention" ⇨ ⇨
and International Molybdenum Association, "Which Stainless Steel Should Be Specified for Exterior Applications?"
I think the first of these in particular would be a big help to you.
I hope this helps.
www.houskaconsulting.com - Pittsburgh, Pennsylvania
2004
Q. I have read with much interest the information on stainless steel railings. I have just completed an ocean front home with approximately 50 linear feet of #316 Stainless steel tube railings. They are subject to severe salt mist and sand grit but to my dismay they begin to discolor/corrode/or rust? in a matter of DAYS. I have tried marine wax but it only works for 7-10 days before the environment takes over. I'm at a loss here since I do not wish to make a career out of polishing my railings. ANY advice would be greatly appreciated. Also-is it possible that the construction crew used too much abrasion when they cleaned the railings? I can detect small scratches in the railings from their efforts. Thank you.
Christie Peckhomeowner - Long Beach, California
2004
A. I am sorry to hear that you are having problems. Type 316 is the right stainless steel to use and it should have provided corrosion free performance. The rapid rate of corrosion is a good indication that the surface was contaminated with steel or iron particles. This could happen if someone "cleaned" with steel wool, cleaning pads that had been used on steel, or if the fabricator did not adequately protect the stainless steel during storage or fabrication in the shop. Your commentary suggests that they should take the time to learn more about stainless steel before working with it again or giving advice. The result is steel particles on the surface that are corroding like bare carbon steel that is exposed to a coastal environment. Staining can take as little as a few hours or as long as a few weeks to appear when there is contamination dependent on temperature and humidity levels.
There is no need to use wax on stainless steel that is clean (no embedded iron) and it could have an adverse impact on corrosion protection. After you resolve this problem, stop using it. See if the container suggests how to remove it from surfaces and clean it off the railing before trying the following.
If the contamination is superficial rather than deeply embedded, it may be possible to remove it using either Zud ⇩ or Barkeepers Friend
⇦ on
eBay
or
Amazon [affil links] (I am suggesting these because they are household cleaning products that are usually readily available.) Make the powder into a thick paste and spread it onto the surface. (Either premix the paste or sprinkle the products on a clean sponge or soft cloth that is moist enough to create a paste when rubbed on the surface. It is best to do this during a cooler part of the day or when the railings are not in direct sun so that the paste stays damp while you are using it. These products contain oxalic acid which will dissolve iron/carbon steel and remove it but will not harm the stainless steel. The fine abrasive can also help remove the carbon steel. Leave the paste in place for 10 to 15 minutes and them start rubbing along the grain line to remove any remaining staining. Rinse off the cleaner thoroughly or it will leave a white film. This is messy but it often solves the problem after one or two applications. You might want to try it in one area to see if it makes a difference before cleaning all of the railings. Never use Comet, Ajax, Softscrub, or similar common household cleaners. They can scratch the finish and some contain chloride compounds that can cause corrosion if they are not thoroughly washed off surfaces.
If this does not work, the carbon steel could be more deeply embedded and it may be necessary to remove the top layer of stainless steel (refinish). Stronger acids could also be tried but I would worry about surrounding materials and the person applying them. If you still have corrosion problems after cleaning with the products above, the contractor should refinish. They need to use new, silicon carbide sandpaper (not aluminum oxide sandpaper!) which should be replaced as soon as it starts to wear - starting with coarse and then using gradually finer papers to get the desired final finish (preferable as smooth as possible for maximum corrosion resistance).
I hope this works.
www.houskaconsulting.com - Pittsburgh, Pennsylvania
Thank you Catherine for your complete response.
I think the culprit was just steel wool contamination,; your solutions to the problem are very complete and I've learned a lot from you.
Thank you again,
Randy
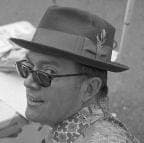
Randy Bolander [returning]
<- Seattle, Washington
2007
A. In my years of experience of finishing stainless steel handrails/welds, etc..I would suggest refinishing the handrails in situ to a finer grade finish, i.e., 240, 320 or even "bright" or "mirror",thus removing any deeper "scratches" that permit oxides etc to "cling" to the finished surface.
Alan Groves- Greater Manchester
May 22, 2009
Adv.
Scratch-B-Gone for Stainless steel quickly dissolves the rust and restores the grain pattern on architectural rail systems and leaves behind a protective coating to repel future rusting. In an accelerated weather test, the chemical treatment withstood 72 hrs of 10% NaCl fog and showed no rust return. Remember Scratch-B-Gone(.com) for rust on your Stainless! All repairs done on-site and non-invasive.
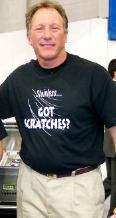
Barry Feinman - Chief Restoration Officer
BarrysRestoreItAll

Carlsbad, California
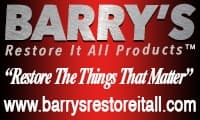
A. I will advise you to make Mirror polish on these railing because mirror polish helps you from corrosion for 2 or 3 years. And I suggest you that if outside railing then always use 304 grade material it has corrosion resistance and 304L is better than 304.
Because 304 grade Carbon content: 0.08%
and 304L Grade tubes Carbon contain: 0.03%
Hope it will be helpful for you.
steel - Ahmedabad, Gujarat, India
May 29, 2010
Q. Dear sir,
regarding your explanation about stainless steel, I have some problem to choose material for railway equipment.
The equipment is used at a beach area in southeast Asia.
Do you have a suggestion for that situation?
Best regards,
product designer - South Sumatra, Indonesia
May 18, 2009
A. Hi Gazali,
I don't know much about railway equipment, but presumably you are not talking about rails which, I believe, must be made of specific steels for strength and wear-resistance needs, rather than of corrosion-resistant stainless steel. What sort of railway equipment please?
Luck & Regards,
Ted Mooney, P.E. RET
Striving to live Aloha
finishing.com - Pine Beach, New Jersey
Q. I have made no. 4 finish on type 304 stainless steel sheet. My client has made panels. But removing PVC from the surface, after some time the sheet is getting red. I don't understand the problem; please advise how to remove redness from the sheet.
Abhishek Purohit- Mumbai, India
September 1, 2012
A. Abhishek,
Would you say the red is a rust color? When you apply the #4 finish, do you use equipment that is used only on stainless, or is the equipment used for carbon steel also? How is PVC involved here?
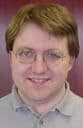
Ray Kremer
Stellar Solutions, Inc.

McHenry, Illinois
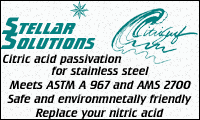
A. Hi Abhishek,
Presumably the PVC is a protective film which is kept on until the stainless steel sheet is installed and put to use? The sheet may not have been passivated or it may not be up to withstanding the specific environment. Can you tell us more?
Luck & Regards,
Ted Mooney, P.E. RET
Striving to live Aloha
finishing.com - Pine Beach, New Jersey
![]() |
Q. Hello sir. - London, U.K. October 1, 2012 ? Hi Shazat. Sorry, but I'm still lost. Is your "structure" made of 304 or 316 Stainless Steel as addressed in this discussion, or is it some other material? Regards, ![]() Ted Mooney, P.E. Striving to live Aloha finishing.com - Pine Beach, New Jersey October 1, 2012 Q. Sorry sir. This is situation at the port near to the sea where exposed corroded reinforcement on the soffit of the beam. So the question is if no corrosion protection currently in that place, what are the recommendations as a repair option to that corroded reinforcement so that the structure can last for 5, 20 and 50 years? Shazat Shah [returning]- London, U.K. October 2, 2012 A. Hi again Shazat. Sometimes people are on completely different wavelengths. Apologies, but I have to leave this one to someone else who may be more familiar with what you are trying to describe :-( Perhaps your query has nothing to do with stainless steel but you have reinforced concrete that has broken and you are inquiring about the feasibility of painting the exposed rebar to try to prolong the life of a failing structure? That doesn't sound reasonable to me, but I am not a concrete beam engineer :-( Regards, and sorry for being unable to help ![]() Ted Mooney, P.E. Striving to live Aloha finishing.com - Pine Beach, New Jersey |
Q.
Is there any way to prevent the welded spot from rusting itself?
MAHA CAUVERY EXPORT- SS SPECIAL PUPOSE KITCHEN UTENSILS AND APPLIANCES - Chennai, India
May 23, 2018
Hi Aravindan. The robust way to address this problem is to start with 316L or 316Ti stainless steel, which is designed to prevent carbide precipitation and consequent corrosion in the weld areas. Some premium cookware manufacturers use that. What are your utensils and appliances made of?
Passivation, perhaps with pickling paste, should be done but may not solve the problem.
Regards,
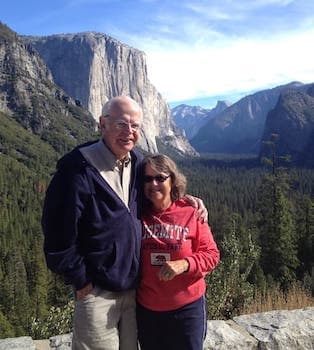
Ted Mooney, P.E. RET
Striving to live Aloha
finishing.com - Pine Beach, New Jersey
Q, A, or Comment on THIS thread -or- Start a NEW Thread