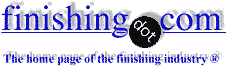
-----
Leach Tank Reliability and Replacement
We currently have fifteen stainless steel tanks used for Nitric Acid baths. Each bath is recirculated through heat exchangers to maintain a consistent temperature of 98degC. Over the past few years we've made several repairs to each tank to patch up leaks. Its now to the point that we need to replace tanks. Its difficult to visually evaluate the extent of the damage simply by looking at the corrosion build up around the outside of the tanks. What would be best way to evaluating and testing the structural reliability of each tank for the means of developing a systematic replacement plan.
Jerry C. Thorne- Danville, Virginia
2003
2003
Hi Jerry,
I would have thought, hoped, anyhow that some s.s. guru would have advised you earlier on. Anyhow, here goes.
However, there's a paucity of info from you (don't worry too much, many/most inquirers omit data) ... and that is WHERE are you having the problems?
1. At the liquid/air interface?
2. At the corners?
3. At welded areas?
4. Cathodic attack near the heat exchangers?
I'd surmise that you'd have trouble at the welds. Have you considered NOT welding with a stainless rod but with a pure nickel weld rod? Why? Because the weld temperature could be more, yes, MORE than some of the alloys melting temperatures ... and lastly, just WHAT grade of stainless were those tanks made of?
Once you can pinpoint areas, helpful suggestions might be made.
... another point (am curious), what is the size of these tanks? If not too large, consider making any replacements from PVDF, which is OK up to l40 degr. C and loves oxidizers. ... and if overly large, then 'armour' the PVDF with fibreglass to achieve a (bonded) dual laminate construction...and the first successful dual laminate tanks in the world were made by Alcore Fabricating in Richmond Hill, Ontario back in the early 60's...
Food for thought, eh?
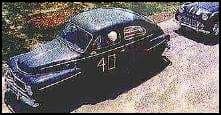
Freeman Newton [deceased]
(It is our sad duty to advise that Freeman passed away
April 21, 2012. R.I.P. old friend).
Q, A, or Comment on THIS thread -or- Start a NEW Thread