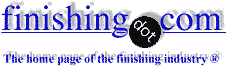
-----
Galling Problem with stainless steel threads
A. Part of our product offering includes couplings with mating threads of 316 Stainless Steel. To overcome Galling we presently Nitrate^nitride followed by sandblasting, pickling and passivation to prevent Galling and inhibit rust formation. I'm looking for an easier solution. I've heard that using a Nitronic stainless or one that has a different hardness for one of the components could eliminate the problem. What would be the difference in hardness required? Is there listed ASME materials to achieve the desired result? Other options?
- Calgary, Alberta, Canada
2003
A. I don't really know the hardness difference you need. But a better answer might possibly be to silver plate one of the surfaces.
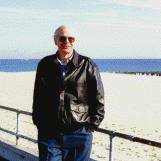
Ted Mooney, P.E.
Striving to live Aloha
finishing.com - Pine Beach, New Jersey
2003
A. A layer of 0.001" of electroless nickel would be my choice. It will solve galling and will uniformly cover the entire surface no matter how intricate. You certainly won't have to blast it anymore and it will look nicer. I don't know if it will be more expensive to what you are using now.
Guillermo MarrufoMonterrey, NL, Mexico
2003
A. My guess is your are thinking of Nitronic 60, a Carpenter product. I do not understand the Nitrate process you are using but why sandblast? It tears metal, glass bead if needed. To get the best from what you have in stock try a electropolish, depending on thread size removal of metal is limiting. EP in addition to smoothing and burr removal, will give you a more lubricious surface finish.
Jon Quirt- Fridley, Minnesota
2003
![]() |
A. Jon, Q. Bill, A. Sure can. If you want a large number of (sometimes contradictory) reports/letters/ideas/theories, try searching this site using keywords "nitride" and "stainless" (just type the two words into the search field together) and limit the number of hits to, say, 50. |
A. Nitronic 60, a galling resistant stainless steel, is an Armco (now AK Steel) product. Carpenter makes a similar material which they call "Gall-Tough". And Myles, that could be a solution to your galling problem. You can fairly easily check with the folks at CarTech, who should be able to tell you if their material can match the corrosion performance of 316 in your environment.
Oh, Nitronic 30 and 40 are different stainless steels, not known for galling resistance. Don't use them here.
Yes, 300 series stainless steels can be nitrided, and it puts a thin, hard,layer on the surface. It is usually below 5 mils thick. Stainless nitrided cases are nice in that the case is a clearly defined layer, with effective case equal to total case. The caveat is that the corrosion resistance is severely impaired, as the chromium is depleted by the nitrided case.

Lee Gearhart
metallurgist - E. Aurora, New York
2003
A. We had the same problem years ago . We used silver on one batch and Cadmium on the other both worked but Cad was cheaper and smeared into the threads which also improved the results because of it's lubricity. An alternative is to make one of the parts from an alloy which is not Nickel rich, thereby avoiding the cold welding problem, perhaps a 400 series stainless.
Dave Brackenridgeaerospace plating - Germiston, South Africa
2003
A. First off, I doubt your process! Any nitrided stainless I've ever passivated has been destroyed due to the chromium depletion that Lee Gearhart correctly refers to. An etched, nitrided part might gall due to the rough, chewed up surface finish! Electropolish is a reasonable approach, however, not easy or advisable on nitrided stainless.
I haven't seen anyone suggest dry film lubricants (ref. MIL-L-46010/MIL-PRF-46010 [from DLA] . They work great on stainless and doing only 1 of 2 mating parts usually does the trick. Silver works for high temp applications but chrome flash is also widely used for nuclear applications.
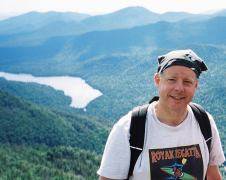
Milt Stevenson, Jr.
Syracuse, New York
2003
A. Electroless nickel phosphorus plated onto one member would not gall.
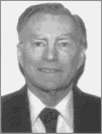
Don Baudrand
Consultant - Poulsbo, Washington
(Don is co-author of "Plating on Plastics" [on Amazon or AbeBooks affil links]
and "Plating ABS Plastics" [on Amazon or eBay or AbeBooks affil links])
2003
A. A Brinell hardness difference of 50HB may overcome galling.
Boon- Singapore
2003
Q. I understand that Nitronic 60 has good galling resistance. What metallurgical feature/quality causes this? I also understand that using materials of different hardnesses reduces galling tendency. In case of using Nitronic 60 with itself there is no difference in hardness, so why doesn't galling occur? I understand surface finish is important yet too fine a surface finish also results in galling as the atoms are able to come closer and cold weld. Is there an optimum finish i.e min and max, to avoid galling.
Thanks in advance,
Raja Setluroil drilling eqpt - Singapore
2004
Q. Where can we buy Nitronic SS Bolts to help eliminate galling - without a spray?
Jim Hannafasteners - Murrells Inlet, South Carolina
June 17, 2013
Q, A, or Comment on THIS thread -or- Start a NEW Thread