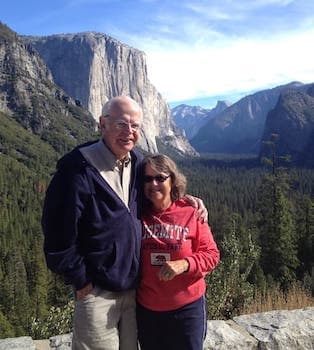
Curated with aloha by
Ted Mooney, P.E. RET
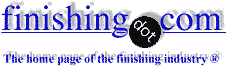
The authoritative public forum
for Metal Finishing 1989-2025
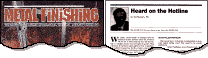
-----
Material Removal from Bright Dip
Have a part made of BeCu that was Heat treated for 2 hours at 600°-625°F. Then plated Gold / MIL-G-45204 Type 1 or 2 Grade C Class 1 ( .00005-.0001 thk ) over copper strike / MIL-C-14550 .0001 Max Thk. Problem is that upon receipt my diameters and threads major diameter were reduced by .0005-.0006 My Plater says that they cleaned the parts prior to plate, and that we should have told him about the diameters before plating. I have never had to do this before.
Question: Is .0005-.0006 too much of a material removal from conventional cleaning ( Bright Dip ) process? I think they may have been left in this dip for too long.
James Ferrick- Tewskbury, Mass, USA
2003
2003
Depending on the particular "bright dip process" being used, 0.0005-0.0006 may not be too excessive. We use a home-brewed solution consisting of nitric & sulfuric acid. I've measured a 0.016 (total- 0.008 per side)loss on a copper shaft after 30 seconds in this dip. I don't believe the proprietary peroxide-based dips are quite as aggressive.
George Brackett III- Utica, New York
I think that .0005/.0006 is definitely too much material to be removed without the plater notifying you first. Having said that, A good manufacturer of the parts will flow down requirements to the plater including any after plate dimensions that have to be held. This information should be clearly stated on the purchase order and/or drawing supplied with lot to be plated. If the parts are properly heat treated and cleaned, there should be no need to remove so much metal. It sounds like an excessive immersion time in a very aggressive bright dip. For plating on heat treated BeCu, I would recommend a heated 50% sulfuric acid 160-180 F soak for 30 minutes to loosen the heat scale. This will not remove any material provided the acid is analyzed regularly and not subject to excessive contamination. This should be followed with a solution of 75% phosphoric acid and 25% nitric acid dip at ambient temperature for 5-30 seconds. You should be able to clean the parts and remove less than .0001 in most cases. If excessive material is removed, in some cases parts may be salvaged with building up the underplating with copper or nickel to bring parts into tolerance. The customer (you) should be notified in a case like this. Another thing I would examine these parts for is etching of the base metal. Can you see irregular patterns, pitting or evidence of chemical attack that did not exist in the part as machined? This is a tell tale sign of over-etching through either poor and overly aggressive cleaning, or a botched strip operation.
Good luck solving your problem.
PeterAero-Dynamics - Massachusetts
2003
Q, A, or Comment on THIS thread -or- Start a NEW Thread