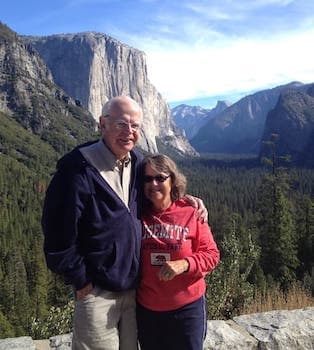
Curated with aloha by
Ted Mooney, P.E. RET
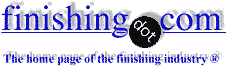
The authoritative public forum
for Metal Finishing 1989-2025
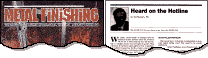
-----
Procedures for Water Break Test
Q. Is there a specific testing procedure for "Water Break Testing"? The application is on aluminum and stainless steel parts. Current guidelines such as ASTM F22 are vague and allow for a great amount of interpretation. What I am looking for is an acceptable amount of beading over a certain area, or the acceptable size of beading, etc. Any insight would be appreciated.
Ron Licari- Rio Rancho, New Mexico, USA
2002
A. Hi Ron. Something you might want to see is "Is it Clean? Testing for Cleanliness of Metal Surfaces" by Anselm Kuhn, Metal Finishing magazine, Sept. '93, pp. 25-31. It is a rather exhaustive analysis of the entire issue of testing for cleanliness.
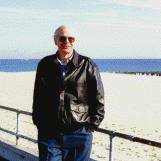
Ted Mooney, P.E.
Striving to live Aloha
finishing.com - Pine Beach, New Jersey
A. Check MIL-C-53072 [MIL-DTL-53072 [link is to free spec at Defense Logistics Agency, dla.mil]] Chemical Agent Resistant Coating (CARC) paragraph 4.3.3.1 for test method and acceptance criteria for a water-break test. You can down-load it from the ASSIST website (DODISS).
Doug HahnPRI - Mason, Ohio
Multiple threads merged: please forgive chronology errors and repetition 🙂
Q. I would like the procedures for the test method for conducting the Water Break Test. Where can I find the procedures?
Ted Duda- St Charles, Illinois
2003
A. It all depends ... if you are doing work to a particular specification, such as the MIL specs or the AMS specs used by the aerospace, sometimes (not always) they will give you a method, or specify the "time" for a water break free surface. Same goes, I'm sure, for automotive, medical or whatever (not my particular field). If your requirements are internal or commercial, you may want to refer to ASTM F21 and ASTM F22 for the "standard" water break and (more sensitive) atomizer tests.
Doug Hahn- Mason, Ohio
A. Ted, check out the ASTM standards ASTM F21, "Hydrophobic Surface Films by the Atomizer Test", and ASTM F22, "Hydrophobic Surface Films by the Water Break Test". Both are found in Volume 15.03, and ASTM is at the obvious www.astm.org website.

Lee Gearhart
metallurgist - E. Aurora, New York
A. Ted,
check Mil-C-53072 B [MIL-DTL-53072 [link is to free spec at Defense Logistics Agency, dla.mil]] "Chemical Agent Resistant Coating" paragraph 4.3.3.1.
There you will find the procedure for the "Water Break Test".
This test is part of our standard painting procedure.
Klaus P. Henz- Neuhausen, Switzerland
Q. I need to find information on the water break test. I went to check MIL-DTL-53072 [link is to free spec at Defense Logistics Agency, dla.mil] "Chemical Agent Resistant Coating" paragraph
4.3.3.1, but there was no paragraph
4.3.3.1.
- Farnborough, UK
2004
A. The section is 4.2.3.1
Tom Sikes- Mendota Heights, Minnesota
2007
A. Water Break Test should occur no later than 4 hrs after post blast cleaning. this will include most steel, not aluminum. if the water beads up then your test has failed and you must clean the surface again. if it just rolls off you should be good. if the post blasted equipment sits for more than 6 hrs before a pre treatment (wash primer) is applied you must perform the test again. If it fails, it needs to be re blasted for proper adhesion.
Stephanie Cuellar- Gatesville, Texas
December 2, 2009
Q. I would like to know the procedure for a water break test ASTM F22
Jacob Palmer- Windsor, ON, Canada
2005
Water Break Test -- Atomizer Method
Q. I work for an aerospace company that deals with NADCAP. During a recent audit we were required to institute water break testing as a means of cleanliness. During the installation we have discovered that some of our materials react differently to the water break test than others. Some have a very discernible sheeting action while others bead up immediately (despite being clean). Typically, the ones that bead up immediately are highly polished materials such as hexalloy and stainless steel.
Has anyone else experienced this? What is a sufficient way of interpreting the test on these types of surfaces? Should a different method of testing be used to determine cleanliness?
Audit Coordinator - Cleveland, Ohio, USA
May 12, 2010
A. What you have found is true. I think that it is because that the surface tension of the water is greater unto itself than it is to the metal as there is nothing for it to "grab" onto.
James Watts- Navarre, Florida
A. As James said, this phenomena has to do with a very low level of adhesion between water and substrate molecules as compared to the normal cohesion between parent water molecules. A surface that does not wet could be an indication of subsequent problems with plate adhesion.
Guillermo MarrufoMonterrey, NL, Mexico
Q. That particular test is a requirement when dealing with CARC paints. Is there another acceptable method for cleanliness when dealing with such surfaces? Thank you for your responses.
John Hunt- Cleveland, Ohio, USA
May 18, 2010
A. This is a wild guess. Try cold DI water--like refrigerator temp.
James Watts- Navarre, Florida
A. I also received a minor NCR (non-conformance) from NADCAP for the same problem despite trying to demonstrate component geometry did not assist with a water break test. I had to re-write Process Breakdown Instructions with a time frame of 45 secs in order to close it out. But must agree with the previous responses you have been given.
Nigel Gill, BSc CSci CChem MRSC MIMF- Glasgow, Scotland
Q. I have read several different ways to conduct a Water Break Test on CARC surfaces, are there any videos out there?
Brandon BrownInspector - Texas
May 5, 2011
Q. I have been looking for information regarding the water break test. I have reviewed ASTM F22 but it can be subjective. What I am looking for is if there is a minimum surface area that can be adequately tested and does the surface have to be smooth? What we are doing is to see if there are any contaminants in areas that have been mildly to moderately abraded with 220 grit sandpaper.
Joe RobertsEngineering - Spokane, Washington
September 28, 2011
A. Joe,
I'm sure there are many ways to describe or codify the water break test, but the basic principle is that you have a surface that is known to be hydrophobic (water doesn't stick to it) when clean, but the presence of various undesirables may allow water to wet the surface instead. (Or vice-versa.) It all has to do with surface tension, chemical composition on the surface, and sometimes also the microscopic physical structure of the surface. All you're really doing though, is asking does water stick to this surface when it is known to be clean, and is it doing the same thing now, regardless of surface area, smoothness, and what have you. It's not necessarily the end-all be-all test of surface cleanliness, but it works well enough for a lot of things.
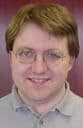
Ray Kremer
Stellar Solutions, Inc.

McHenry, Illinois
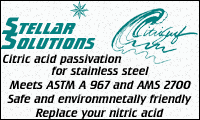
Q. Water Break Test and Atomizer test -- how do they differ?
Which is recommended for CRCA Strip before 3 microns Nickel plating?
What precautions should be taken while doing Atomiser test?
Sekhar
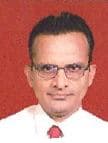
Chandrasekhar MV
- HYDERABAD, INDIA
November 20, 2012
Q, A, or Comment on THIS thread -or- Start a NEW Thread