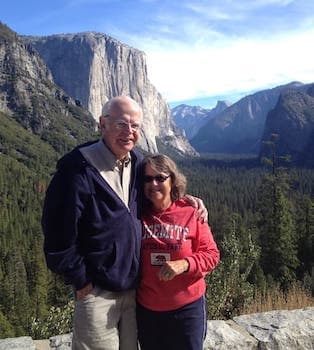
Curated with aloha by
Ted Mooney, P.E. RET
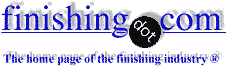
The authoritative public forum
for Metal Finishing 1989-2025
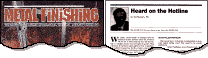
-----
FPL Etch Q&A's, Problems & Solutions
Q. Most recipes for FPL Etch of Aluminum call for a "seeding" of the chrome/sulfuric acid solution with aluminum in varying amounts.
Question : What does the "seeding" do?
G. Green- Canada
1999
A. Essentially, the pre-dissolved aluminum changes both the rate and structure of the oxide growth on the aluminum substrate. This appears to be due to differing surface reactions between the seeded etch and non-seeded etch surfaces in the rinse waters following the FPL etch. These differences are marked between clad alloys and non clad alloys. This phenomenon seems to involve the copper constituent contained in the 2000 series aluminum and is analogous to the mechanism which takes place in trace copper containing bright dip solutions. One important relationship occurs with bonding, where the adhesive bond is more durable and more bondable when seeded FPL etch solutions are used. This is because seeded FPL etch solutions produce more porous and thicker oxide layers.
Ward Barcafer, CEFaerospace - Wichita, Kansas
Q. It is my understanding that letters FPL in FPL Etch stands for the inventors of the process, Forest Products Limited. Can someone confirm?
Danny Wilson- Savannah, Georgia
2002
A. Hi Danny. Yes, that is correct. FPL Etch is covered by ASTM D2674, "Standard Methods of Analysis of Sulfochromate Etch Solution Used in Surface Preparation of Aluminum".
Regards,
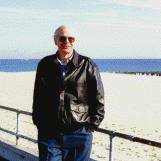
Ted Mooney, P.E.
Striving to live Aloha
finishing.com - Pine Beach, New Jersey
April 2014
The FPL in the name of FPL etch stands for Forest Products Laboratory in Madison, Wisconsin where the process was developed.
Julie B.- Madison, Wisconsin
September 12, 2023
Ed. note: This forum is intended to help build camaraderie through sharing of tips, pics, anecdotes, & opinions.
When people withhold their names, those readers who offer theirs may be less likely to engage.
Multiple threads merged: please forgive chronology errors and repetition 🙂
Etch Rate Too High
Q. I have just recently put in charge of an existing FPL etch and PAA line (per BAC5555). I understand the process ( I believe). I just need to check on an etch rate problem I am having on 2024-t3 and 7075-t6 Aluminum. High etch rates > .0004mg/surface/hour. Sulfuric/ Chromic acid bath concentrations are within specification. Bath temps & times within spec. Lap shears are within specification.
I have been told the trivalent Chrome concentration of the tank should be below 3.0 mg/L or the CR+3 will interfere with the deposit of hexavalent chromium on the surfaces (HexChrome is being converted to Trivalent Chrome). The hexavalent chrome is also acting as a buffer to sulfuric acid to reduce the etch rate. Is this all correct? Is the 3.0 mg/L correct? If too high can I get rid of it without disposal of the tank's contents?
Joe Harmuth- Connecticut, USA
2002
FPL Etch Solution Replenishment
Q. My question is in regards to FPL etch solution replenishment. How does one know when to change the solution of the FPL etch tank prior to failing a test such as wedge crack per ASTM D3762 [withdrawn]? I am currently titrating to determine and maintain sulfuric acid and sodium dichromate levels IAW BAC 5555. However, other specifications mention 2024 bare aluminum and metallic copper/copper sulphate. Is there any other testing or elements of the solution I should be monitoring?
I would appreciate any info. Thanks!
Peter Blais- Glen Cove, New York
2002
A. You could try using the etch rate test from the BAC but a system of statistical procecs control on the wedge cracks, and maybe the etch rate, will probably be the best control.
Ciaron Murphy- Great Britain
Procedure for Analysis
Q. Hi,
I work for a company that makes composite aircraft propellers. We have decided to use the FPL etch process to prep our components prior to being bonded with composite resins. We have tested the FPL etch and would like to use it in production. However, before we can do that we need to develop a procedure to ensure that the bath is always in good working order. That being said, here are my questions.
We are starting to use the FPL etch process and I was wondering how you should check the solution. Is a titration process the best process? If so, what would be the procedure to check chromic acid, sulfuric acid, and aluminum? And, how do you convert the titrated result into a solution concentration?
Thanks!
Pat Stumpff- Piqua, Ohio, US
2003
A. The recognized chemical control methods for the chrome sulfuric etch (FPL) is the relative density and free chrome content. The density can be monitored by a hydrometer and is given an upper limit of 1.45-1.5 before the solution is considered to be exhausted.
The free chrome content is continuously maintained between 40-50 g/l by the regular addition of chromic acid. This is monitored by titration as follows.
Take 1 milliliter of etch and add 8-10 milliliters of specker acid. Add a few drops of diphenylaminesulphonate indicator and titrate against 0.1N ferrous ammonium sulphate (FAS)
For 1 millilitre of etch the calculation is. Titre x N(FAS)x33.3=g/l CrO3.
For stable process control the use of continual anodic oxidation should be considered.
Hamish McWillie- Northamptionshire U.K
Specker Acid, Diphenylaminesulphonate
Q. I see the titration method but cannot find specker acid or diphenylaminesulphonate. Can you please supply the CAS identification and or the supplier of these chemicals.
Gute MartinPhoenix Composite Solutions - Oscoda, Michigan
2004
A. Change the spelling to: diphenylaminesulFonate.
CAS: Barium salt: 6211-24-1
Sodium salt: 6152-67-6
- Long Beach, California, USA
Multiple threads merged: please forgive chronology errors and repetition 🙂
Q. What is the make up of specker acid. FPL Etch is becoming rare these days and I am beginning to deal with this process after twenty five years. Thanks
Dana Cote- Andover, Massachusetts, USA
August 26, 2010
A. We are just starting to use an FPL Etch here and this is the procedure that I found for controlling the solution
For Sodium Dichromate
1. Pipette
[pipettes on
eBay or
Amazon [affil links]
2 ml of acid etch to be tested into a 250 ml Ehrlenmeyer flask. Drop a magnetic stir bar into the
bottom and place on a stirrer.
2. Add 50 ml of deionized water by transfer pipette.
3. Add 12.5 ml of 10 percent H2SO4 (by pipette or buret).
4. Add 3 ml of potassium iodide [20 percent solution] (by pipette or buret).
5. Titrate with 0.1N sodium thiosulphate
⇦ this on
eBay
or
Amazon [affil links]
until a straw color appears -- do this very slowly so as not to overshoot the end-point (from buret).
6. Add 2 ml starch indicator by pipette.
7. While stirring rapidly, add 0.1N sodium thiosulphate drop-wise very slowly until the color changes to a light blue.
8. Record the number of mL of Sodium Thiosulphate used.
Sodium Dichromate(g/L)= [(mL of Sodium Thiosulphate x 4.967)/2]
For Sulfuric Acid
1.Place a stir bar in a 250 mL beaker [beakers on
eBay
or
Amazon [affil links] .
2.Transfer 0.5 mL of Etching solution by pipette or buret
3.Add 100 mL of deionized water.
4.Rinse pH electrode with deionized water and blot dry.
5. Standardize the pH meter with ph 4 and 7 buffers.
6. Rinse electrodes and wipe dry.
7. Immerse electrodes in the acid solution which you have placed on a stirrer.
8. Add NaOH (0.1N) drop-wise until pH 3.5 is reached.
9. Record the number of ml of NaOH (0.1N) used.
Sulfuric Acid (g/L)=[(mL of 0.1N NaOH used x 49.04)/5]
Hopefully, this helps you a little bit.
- Eastman, Georgia, USA
November 18, 2011
Etching Paste for Aluminum Bonding with Epoxy
Q. Hi -
I have a motorsports repair application where I need to bond several aluminum sheets (6061-T6, 0.063" thick) to a steel frame using an epoxy.
The recommended aerospace surface preparation procedures for the aluminum include (1) FPL etching (chromic-sulfuric acid etch), (2) chromic acid anodize, and (3) phosphoric acid anodize. All three processes require immersion, and we do not have access to a tank large enough to immerse the aluminum panels (the largest panel is around 3 feet by 6 feet).
Additionally, only a small percentage of the aluminum sheets will actually be bonded (i.e., the area in contact with the steel frame). The large majority of each sheet will not be bonded to anything.
Is there an established etching paste that I can apply to the aluminum to selectively etch only those areas that will be bonded? For example, an "FPL paste"?
This is a high performance application, so I don't want to take chances by attempting to home-brew a paste solution.
Thank you in advance,
- Mendham, New Jersey
November 5, 2012
Storing FPL Etch Solution When Not in Use
Q. What's the best way to keep an FPL etch bath if it won't be used for several months? Is turning off the heat and covering it up sufficient?
Bart Van Rees- Sudbury, Massachusetts
July 23, 2013
A. Yes, that is fine as long as the storage area is cool and dry but well ventilated. When the time comes to use the solution again it will need to be analyzed internally and tested prior to resuming production.
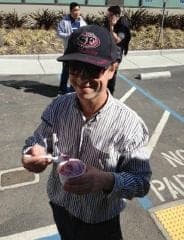
Blake Kneedler
Feather Hollow Eng. - Stockton, California
ASTM D2674.html is in error on dichromate analysis
Q. Can anyone shed light on this for me to see if this interpretation is correct?
Look at method 'C' for Dichromate analysis within the ASTM D2674 specification. They have the calculation factor wrong by half, in that it should be 24.85 x mLs x 0.1 (Thiosulphate normality).
I saw this and couldn't believe it was what it was so I made up a standard (30) gpl solution of Sodium Dichromate and got (60.1) gpl by using their calculation as below;
(12.1) mLs titer x 49.7 x 0.1N Thiosulphate = 60.14 gpl Dichromate. So either they have the mLs of sample wrong, i.e., they list (25 mL/250 then 20) mLs out which is equal to a two mL sample or they forgot to divide by the two moles of Chromate per mole of Dichromate.
Im curious if anyone can let me know if this seems correct.
Employee - Westfield, Massachusetts USA
April 22, 2014
A. Vinnie,
I would contact ASTM (astm.org/CONTACT/index.html) and have them put you in touch with the subcommittee chair for Subcommittee D14.80, which controls that standard. If you have indeed discovered an error, they should create a work item to correct it and release a revision within a year.
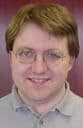
Ray Kremer
Stellar Solutions, Inc.

McHenry, Illinois
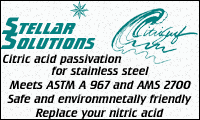
Q. I have a laboratory method that calls for seeding the FPL bath with copper II sulphate using BAC 5555 solution #1. BAC only calls for the addition of copper with solution #2 and #5. What is the effect of adding copper to solution #1?
Jennifer Heelan- Bay Point, California, USA
October 31, 2017
Q, A, or Comment on THIS thread -or- Start a NEW Thread