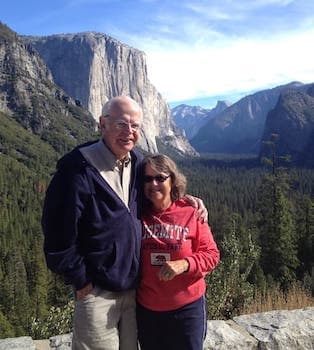
Curated with aloha by
Ted Mooney, P.E. RET
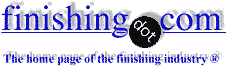
The authoritative public forum
for Metal Finishing 1989-2025
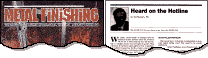
-----
Cleaning C2700 Brass in Preparation for Zinc Plating
We are having problems cleaning brass inserts made out of C2700 Brass. The parts are heat treated (annealed). We are attempting to zinc or cadmium barrel plate these inserts. We have black spots left on the I.D. of the parts and this results in poor adhesion of the plating. Can anyone help us in the precleaning of these parts well enough to plate them. Nasty bright dips are not an option
Andy Scheerplating service - Pacoima. CA
1998
1998
Sure sounds like a cleaning or activating problem --
- What do you think that the "soil" is?
- What is the cutting fluid type that is being used?
- Are these parts tumbled after machining?
- What is your current cleaning process/cycle?
- Navarre, Florida
Try a chelating cleaner (if your waste treatment system can handle it).
All our rinses are recycled through ion exchange and carbon so the chelator is no problem. Concentrated wastes are drummed for off-site disposal.
We use a product from Technic called 1508L. It's liquid, contains only a wetter and the chelator. You can run a wide range of concentrations and temperatures to fit your application. For brass, we go directly to the plating tank after clean and rinse, no acid dip is necessary. I'm sure other suppliers have similar products.
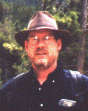
Bill Vins
microwave & cable assemblies - Mesa (what a place-a), Arizona
1998
Sir, Can anyone suggest the proper solution for cleaning and de-oxidizing beryllium. The metal in question is the head of a set of golf clubs but have a plastic insert on the back. Whatever is suggested, the cleaning dip cannot be toxic or extremely corrosive. Thank you
McGurran A J- London, Ontario, Canada
1998
As an alternative to stoddard solvents, I like the Actrel series of high purity hydrocarbons made by Exxon and distributed by Safety-Kleen. These are very pure, have extremely low odor, function essentially the same, and are available with varying flash points. Other manufacturers offer similar solvents (Phillips and Texaco I believe). A family member also uses the higher flash Actrel in his automobile repair shop's open top parts washer; it is nice to be able to wash parts and not have any of the residual odor.
Tom
Tom HandDOE - KC, Missouri
1998
Did you consider to polish in a machine called "rotofinish". The inserts would spin around in a tub filled with water, ceramic abrasive little stones (all kinds of shapes)and some soap if necessary. Otherwise you can test out some acid in water to dip in.
Johny RiskinRISKIN - Belgium
1999
Can anyone advise me regarding the following... We manufacture brass components and presently have a need of adding an acid bath to our manufacturing process. We use the following brass classification C37700. What is the best chemical composition to use for an acid bath that will assure us that the component will meet NSF Standard 61. Any help would be appreciated. I would also appreciate the name or names of the suppliers of the above.
Frank D- Ft. Lauderdale, Florida
1999
Q, A, or Comment on THIS thread -or- Start a NEW Thread