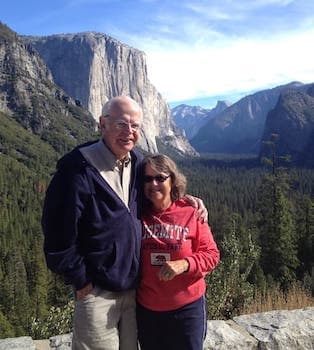
Curated with aloha by
Ted Mooney, P.E. RET
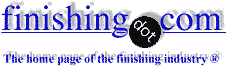
The authoritative public forum
for Metal Finishing 1989-2025
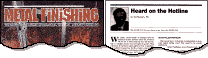
-----
Surface Roughness after Chromate
I have a small die cast zinc part that is subsequently zinc chromated to an olive drab color. Surface roughness measurements of many of these parts show them to be exceedingly rough with large variations between parts. Some of the parts also exhibit surface features that resemble "running paint". Is this condition caused by the chromating process or in the casting?
G Stanley Sangdahl- Aurora, Illinois, USA
2003
My best guess without seeing the part is that your prep cycle is removing too much zinc and exposing the silicon, aluminum and other junk that is common in zinc die casting. This exposed non-zinc is the roughness and/or bumps left on the surface. Back off on the acid dip. Alkali clean in a very mild cleaner, acid dip in 2% sulfuric acid for a very short time, just after the gassing is first visible, then be sure the chromate bath is fresh and free of impurities. Zinc, aluminum and the other junk build up in the chromate and shorten it's life.
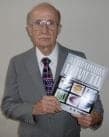
Robert H Probert
Robert H Probert Technical Services

Garner, North Carolina
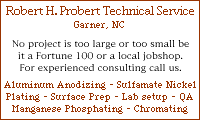
2003
Robert's advice is correct though sometimes difficult to follow. An alternative, which may cost more, is to have the parts zinc plated then chromated. This will result in a smoother surface with a uniform color of chromate film.
Gene Packmanprocess supplier - Great Neck, New York
2003
Q, A, or Comment on THIS thread -or- Start a NEW Thread