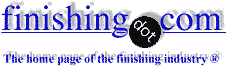
-----
Titanium Recast Layer/Alpha Case Removal
TSS is machining a titanium bearing housing from a forged, round billet. It is expected that the surface will have some recast layer or alpha-case present that will require chemical or mechanical removal. Is there a spec that details the various methods that will successfully remove this layer?
John H [last name deleted for privacy by Editor]- Cincinnati, Ohio
2003
If you are machining a forged billet, the machining operation will remove any recast layer or Alpha case. If this part is going to end up in a turbine engine, the major manufacturer will have a mandatory method to use. To the best of my out of date knowledge, metallurgical (destructive ) analysis is the normal method. Pratt and Whitney Had a blue etch anodize method as a non destructive test method, but it is very proprietary. The classified published method had a major flaw in it, which I firmly believed was intentional.
James Watts- Navarre, Florida
2003
Since posting the original question, I have learned that we will be EDM'ing certain areas of the part. That I understand is what creates the recast and/or alpha case layer. Again, I wonder whether there is an ASTM type spec or any other the covers cleaning, etching, etc of Ti to remove this contamination.
Thanks,
John H [last name deleted for privacy by Editor]- Cincinnati, Ohio
2003
2003
Go to the ASTM website (www.astm.org) and do a standards search. There are a lot of titanium standards, the following may be applicable to your situation.
ASTM B381Standard Specification for TITANIUM and TITANIUM Alloy Forgings "covers 32 grades of annealed titanium and titanium alloy forgings"
ASTM B348Standard Specification for TITANIUM and TITANIUM Alloy Bars and Billets "covers annealed titanium and titanium alloy bars and billets"
ASTM B600(2002) Standard Guide for Descaling and Cleaning TITANIUM and TITANIUM Alloy Surfaces. "Acid etching may be required following cleaning when the surface has an oxygen-contaminated layer or alpha case present." I have some familiarity with the 3rd of these standards, so will mention that it is difficult to remove very much material by acid, and titanium is subject to hydrogen embrittlement from many acids. I believe that it is safe to use nitric:hydrofluoric at > or = 5:1.
Electrochemical machining (ECM) is advantageous for removing material and leaving a smooth, defect-free surface. [Metals Handbook, Vol. 5, p. 112 (1994)]
Ken Vlach [deceased]- Goleta, California

Rest in peace, Ken. Thank you for your hard work which the finishing world, and we at finishing.com, continue to benefit from.
2003
The process you use may depend on the customer and the service conditions of your product. Alpha case removal is a standard process in the aerospace industry and the method you use is usually dictated by the prime contractor. The most common is probably a controlled nitric acid / hydrofluoric acid "pickle" -- or "etch" or "chem mill", the terminology used to describe the process is rather loose.
I suggest you obtain and review ASTM B600 "Standard Guide for Descaling and Cleaning Titanium and Titanium Alloy Surfaces", AMS2642 "Structural Examination of Titanium Alloys - Etch-Anodizing Inspection Procedure" and AMS2643 "Structural Examination of Titanium Alloys -- Chemical Etch Inspection Procedure", and the Aerospace Recommended Practices SAE ARP1331 "The Chemical Milling Process" and SAE ARP1755 "Effect of Cleaning Agents on Aircraft Engine Materials --- Stock Loss Test Method".
As a fellow Cincinnati-an, while you can order these from SAE and ASTM, they are also available from our main branch library for review and/or copying; they are extremely helpful people. The key is a "controlled etch"...it is important to monitor and control the tank chemistry and etch rate (coupons, factors such as bath temperature, solution agitation, tank size relative to your hardware and the part geometry are also critical. Be sure to preclude air entrapment and solution drainage, recesses and blind or small diameter holes...are you EDMing the surface in general or are holes or slots EDMed? Rinsing is another critical step...halogen levels (especially chorine and chlorides)need to be monitored and controlled with a final DI water rinse of probably 50,000 ohm-cm or better, and even better a final DI water spray of the same quality. Validation of the process is also critical, test pieces, whether a similarly processed coupon from the same heat lot as your production hardware, scrap or a sacrificial production part will need to be evaluated before and after etching/milling. Again, it is critical that the test piece be co-processed with your production lot...and every production lot...to validate alpha case removal. These pieces need to not only be processed through the EDMing of the lot, but also any alpha case producing step, such as heat treat, welding, brazing. Metallographic evaluation needs to be done...before and after, and at multiple magnifications, of polished metallographic specimens. Often the examination process requires customer evaluation and approval in addition to the etch process. Pre-cleaning steps--solvents such as acetone ⇦ on eBay or Amazon [affil links] Warning! Flammable! or caustic solutions are another important step to control. Also be sure to preclude any cleaning of the parts with methanol or any halogenated solvent--this includes tap water, and to handle the part with white cotton gloves after cleaning until final processing is complete (heat steps). QA procedures for positive traceability between test pieces and manufacturing lots is also important to control.

Never use HF anywhere unless trained!
If you do, you MUST have the antidote gel on hand for instant use!
Calcium Gluconate
for HF acid burns
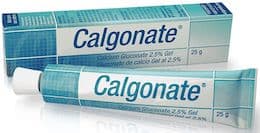
on eBay or Amazon
(affil link)
Other considerations: the control of your out-source, analysis procedures for the nitric/hydrofluoric acid and, if doing this in house, precautions in handling materials, especially the hydrofluoric acid...have your plant safety officer aware of its unique hazards (note that nitric acid needs to also be handled with respect) and consider to have calcium gluconate ointment.
available for first aid in case of HF burns ... and follow up with professional treatment. While I've thrown a lot on the table, the list of concerns is certainly not exhaustive, without knowing your "industry", processing and hardware requirements.
- Mason, Ohio
![]() |
Try an etch using ammonium persulphate+sodium fluoride, there are a number of proprietary products on the market that are made of this exact chemical combo. It etches without the risk of hydrogen embrittlement, as no actual acidic compounds are used. This particular etch will meet almost all surface requirements pertaining to titanium alloys, and stainless steels. Jeff Swayze- Kelowna, B.C., Canada 2003 John, If it is an EDM recast layer you wish to deal with I have had the best results with an hot alkaline prep to condition the "scale" and then move to an acid to remove it. We do not use HF as it just too freaky to deal with. Jon Quirt- Minneapolis, Minnesota 2003 |
Jeff, your response to Johns question was to try ammonium persulphate+sodium fluoride to remove the alpha case. I have heard this before but do not know any details. I would like to learn more about it. Can you give any examples for products on the market with this composition (commercial names or something) ? How much is the content of the two components ? What are these products normally used for ? Do you know how they work ? It would be good to know an alternative for HF/HNO3 stuff. Thanks, Christian
Dr. Christian Sauer- Hamburg, Germany
2003
A company called Turco manufactures a titanium etch based on sodium fluoride (or some other fluoride salt). I forget what the solution number is, Turco 41404104 or something like that. It is still used in a nitric solution.
I believe they distribute directly so get in touch with them. Good stuff, slower than HF+Nitric but just as controllable. No problem with hydrogen embrittlement or HF related accidents.
You'll need an Ion selective analyzer (~$2000) to determine fluoride concentration. Some pH meters have that capability with the correct probe.
William Beeson- Phoenix, Arizona
2003
Dear William, thanks for your input. I have contacted the Turco supplier and the product is Turco 4104 (so your number was close). I am currently waiting for the data sheet. Let's find out whether it works.
Thanks,
Dr. Christian SauerAerospace - Hamburg, Germany
2003
Does anyone know if one can use the SEM to evaluate whether or not the recast on EDM'd Ti 6Al-4V surfaces has been removed? If so, what is the criterion? THANKS!
DARREL L [last name deleted for privacy by Editor]- BOULDER, Colorado
2005
The alpha case is sometimes visible in a polished and etched micro-section as a white layer in an optical metallurgical microscope or a dark layer in an SEM in back-scatter mode. It can also be detected by micro-hardness indentation of a section normal to the surface. The layer is caused by oxygen diffusion into the surface and in an alpha/beta alloy like Ti-6Al-4V (Ti-64) as well as hardening and therefore embrittling the titanium it also stabilises the alpha phase near the surface (which appears white in an optical micrograph). The thickness of the alpha case depends on the exposure time, atmosphere and temperature but for typical titanium forgings it is usually less than 20 microns (metric units). The alpha case will only normally be a problem in high stress applications. The aerospace industry usually remove the alpha case by machining or chemical milling.
Malcolm Ward-Close- Farnborough, UK
2007
Chem milling will safely remove alpha case
Lynda Morris- Fort Worth, Texas
May 15, 2008
In response to the removal methods for alpha case on titanium there is another approach. Minimize the development of alpha case to begin with. There are coatings like the Ceram Guard line that block nitrogen and oxygen on titanium parts being heated to control the formation of alpha case. If no alpha case forms on the titanium parts then there is no need to remove it.
Glenn Pfendtcoating manufacturer - Florence, Kentucky
March 3, 2009
Q. How effective does the pickling using Hydrofluoric acid, H2O and nitric bath contribute to developing alpha case during solution treat when not properly cleaned?
Stephen Shin- Anaheim, California, USA
April 18, 2013
Q. At which level of the manufacturing process of fasteners is alpha case introduced, when present on the surface of a finish fasteners, screw or bolt? is this layer of alpha case caused by absorbtion of oxygen in the metal matrix, thus changing the structure? If so, if I run gas detection test to determine the amount of oxygen, will the alpha case increase the ppm of oxygen on my test results over that of a sample without alpha-case?
Miguel A Diazaircraft - Valencia California, US
June 19, 2013
Q, A, or Comment on THIS thread -or- Start a NEW Thread